Modulares mechatronisches Produktionssystem (MPS): Station Roboter
- zurück zur Seite: Praktikum Produktionstechnik
- zurück zur Seite: Mechatronisches Produktionssystem zur Produktion eines HSHL-Getränkuntersetzers
Wichtige weiterführende Artikel:
- zum Artikel: Industrieroboter Mitsubishi RV-2AJ
- zum Artikel Produktion eines HSHL-Getränkeuntersetzers: Schweißen (Station 2)
Systemübersicht
Die gesamte Station der Robotermontage eines pneumatischen Zylinders besteht aus zwei einzeln auf fahrbaren Gestellen montierten Tischen. Da die Station nur aus der Kombination beider funktioniert, sind diese fest miteinander verbunden. Auf der linken Hälfte befindet sich der Hauptakteur: Der Roboter. In dem Arm integriert ist ein Farbsensor zur Erkennung der Werkstückfarbe. In Gelb zu sehen ist die Zuführrutsche, über die das Werkstück in den lila umrandeten Entnahmebereich gelangt. Von der Entnahme aus wird der Grundkörper in den blauen Bereich der Werkstückmontage transportiert. Die für die Montage benötigten Teile befinden sich in den jeweiligen Magazinen. Das Kolbenmagazin ist im braun umrandeten Bereich, während sich die Deckelentnahme im grünen und die Federentnahme im Schwarzen Rechteck befinden. Nach erfolgreicher Montage wird der Zylinder über die in weiß gekennzeichnete Rutsche an die nachfolgende Station weitergegeben.
Die Kennzeichnung der Sensoren sind:
Sensoren | |
---|---|
- B1 | Sensor am Greifer (Farberkennung) |
- B2 | Sensor Orientierung (integriert im Modul Werkstückmontage) |
- Part_Av | Sensor Part Available (Grundkörper in Zuführrutsche) |
- 1B1 | Federzylinder ausgefahren |
- 1B2 | Federzylinder eingefahren |
- 2B1 | Deckelzylinder eingefahren |
- 2B2 | Deckelzylinder ausgefahren |
- B1 (auf Modulhälfte mit Magazinen) | Deckel in Abholposition (ja/nein) |
- B2 (auf Modulhälfte mit Magazinen) | Deckelmagazin leer |
- B3 (auf Modulhälfte mit Magazinen) | Feder in Abholposition |
- IP_FI | Folgestation frei |
Aktoren | |
---|---|
- 1M1 | Federzylinder verfahren |
- 2M1 | Deckelzylinder verfahren |
- IP_N_FO | Station belegt |
Roboter Mitsubishi RV-2AJ
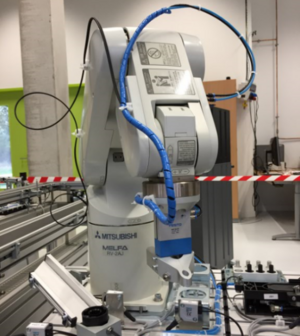
Für die Einrichtung und Bedienung des Roboters gibt es einen eigenen Artikel: Industrieroboter Mitsubishi RV-2AJ.
Betriebsdruck: 600 kPa (6 bar)
Spannungsversorgung: 24 V DC, 4,5 A
Alle Komponenten, Verschlauchungen und Verkabelungen sind eindeutig gekennzeichnet, so dass ein Wiederherstellen aller Verbindungen problemlos möglich ist.
Funktion und Referenzdaten
Die Aufgabe der Station Roboter ist es:
- Die Materialbeschaffenheit eines Werkstückes festzustellen,
- Werkstücke aus einer Aufnahme zu entnehmen,
- Die Werkstücke an eine Montageposition zu transportieren und orientiert abzulegen,
- Werkstücke zu einem Magazin zu transportieren und sie dort abzulegen oder
- Die Werkstücke an eine Folgestation weiter zugeben.
Zum Transport der Werkstücke wird ein Vertikal-Knickarmroboter eingesetzt. Es handelt sich hierbei um einen industriellen Roboter mit 5 Achsen. Die Wiederholgenauigkeit der Roboterpositionierung beträgt ± 0,02 mm. Die maximale Geschwindigkeit beträgt 2200 mm/s. Eine Endstellungs- und Überlastüberwachung ist integriert. Die maximale Reichweite des Roboterarms beträgt 410 mm.
Das Modul Rutsche dient zum Transportieren oder Lagern der Werkstücke. Durch die variable Einstellung von Neigung und Höhe ist dieses Modul universell einsetzbar. In der Station Roboter wird das Modul Rutsche zur Zuführung des Werkstückes zum Modul Aufnahme verwendet. Das Werkstück immer über die Rutsche der Aufnahme zuführen. Es darf nicht von Hand in die Aufnahme gelegt werden!
In das Modul Aufnahme werden bei der Station Roboter Werkstücke über die Rutsche eingelegt. Die Werkstücke werden in der Aufnahme von einem optischen Reflex-Lichttaster erkannt.
Der Greifer ist am Roboterarm montiert. Als Antrieb für den Greifer wird ein pneumatischer Parallelgreifer eingesetzt. Die Greiferbacken sind so konstruiert, dass der Greifer drei Greifpositionen besitzt. Außengreifer und Mittelgreifer werden zum Transport der Werkstücke Grundkörper und Deckel eingesetzt. Mit dem Kolben-/Federgreifer werden die Kolben oder die Feder gegriffen. Ein optischer Reflex-Lichttaster (Lichtleiter) in einem der Greiferbacken wird zur Farberkennung der Werkstücke eingesetzt.
Im Modul Montageaufnahme werden die Werkstücke montiert. Ein Bolzen in der Werkstückaufnahmeposition „Montage“ sorgt für eine gegen Verdrehung gesicherte Positionierung des Werkstückes. In der Position „Umgreifen“ wird der Grundkörper abgesetzt, damit der Roboter zur Ermittlung der Orientierung umgreifen kann. Der Referenzpunkt wird beim Teachen des Roboters angefahren. Alle weiteren Positionen werden vom Referenzpunkt aus im Roboterprogramm berechnet. Mit einem Reflex-Lichttaster wird die Orientierung der Werkstücke Grundkörper und Deckel geprüft.
Das Modul Magazin dient zur Lagerung runder Werkstücke. Ein Schieber verhindert beim Entnehmen des Rohres aus dem Halter, dass die Werkstücke herausfallen. Im Fallrohr des Moduls Magazin können bis zu 8 Werkstücke gespeichert werden.
Ablaufvoraussetzungen
Startvoraussetzung:
- Ein Werkstück in der Aufnahme
Ausgangsstellung:
- Roboterarm in Grundstellung
- Greifer geöffnet
Ablauf starten:
- Spannungsversorgung und Druckluftversorgung überprüfen.
- Werkstücke an Übergabestellen von Modulen oder Stationen vor dem Richten von Hand entnehmen.
- Der Roboter steht in der Grundposition.
- Ein Werkstück über die Rutsche in das Modul Aufnahme gleiten lassen.
- Ablauf der Station Roboter starten: MODE Schalter am Steuergerät in die Position AUTO (Op) stellen. Mit dem Taster CHANG.DISP die Programm-Menüanzeige wählen. Mit den Tasten UP und DOWN die Programmnummer selektieren. Servospannungsversorgung durch Drücken des Tasters SVO ON einschalten. Taster START am Steuergerät drücken.
(HINWEIS: Der Ablauf kann durch Drücken des NOT-AUS Tasters oder durch Drücken des STOP Tasters jederzeit unterbrochen werden).
(HINWEIS: Bei einer Kombination mehrerer Stationen gilt: Richten der einzelnen Stationen erfolgt entgegen dem Materialfluss).
Umsetzung/Entwicklung des Roboterprogramms
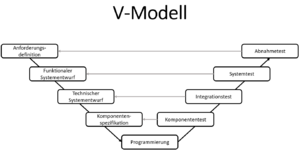
Um eine ungeordnete Arbeitsweise zu verhindern, wurde das Vorgehen nach dem V-Modell (vgl. Abbildung 8) geplant und durchgeführt. Dies versichert eine strukturelle Herangehensweise und Bearbeitung des Projektes.
Alle Dateien und Dokumente wurden für die Arbeit während und nach des Projektes in SVN gespeichert.
Anforderungsdefinition
In der Anforderungsdefinition werden als erster Schritt alle Tätigkeiten und Aufgaben definiert, die während des Projektes bearbeitet werden sollen. Die Strukturierung ist hierbei sehr entscheidend. Damit die gesamte Liste übersichtlich wird, bietet es sich an verschiedene Teilbereiche des Gesamtprojektes zu erstellen und die damit verbundenen Einzelaufgaben zu verbinden. Die Anforderungen in unserem Projekt wurden wie folgt gegliedert:
- Aktuelle Lage beurteilen
- Anlage in Betrieb nehmen
- Schnittstellen
- Software/Werkzeuge
- Dokumentation
Die Datei der Anforderungsdefinition kann hier gefunden werden.
Funktionaler Systementwurf
Der funktionale Systementwurf stellt die Zusammenhänge in dem mechatronischen System ganz grob dar. Ohne gewisse Schnittstellen zu definieren wird bei ihm klar, wie welche Einzelkomponente mit anderen Komponenten und dem Gesamtsystem in Verbindung steht. Darüber hinaus sind alle Bauteile, die mit diesem System zusammen stehen aufgelistet.
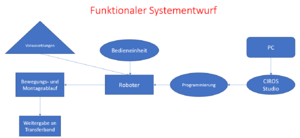
Am Anfang steht der Computer als Schnittstelle zu dem Menschen. Auf diesem Rechner muss das Programm CIROS Studio installiert sein. Mithilfe dieser Entwicklungsumgebung kann der Bediener eine eigene Syntax oder einen bestehenden Programmcode auf den Roboter laden. Nach Überspielen des Programms kann dies nun über die Bedieneinheit des Roboters gestartet werden. Um das Programm durchlaufen lassen zu können, sind bestimmte Voraussetzungen nötig:
- Magazine gefüllt
- Modul Montage und Roboter in Grundstellung
- Werkstück in Aufnahmeposition
Bei Erfüllen dieser Punkte startet der Bewegungs- und Montageablauf selbstständig. Ist der Zylinder fertig montiert, wird er über die Weitergaberutsche an das Transferband übergeben.
Die Datei des funktionalen Systementwurfs kann hier gefunden werden.
Technischer Systementwurf
Der technische Systementwurf steht für den Entwurf der technischen Realisierung. In ihm wird das System detailliert zerlegt und Schnittstellen definiert. Es ergeben sich einzelne Komponenten aus dem Gesamtsystem. Neben der genauen Bezeichnung der Schnittstellen werden hier auch die Art von Informations-, Daten-, oder Stoffflüssen benannt. Das grundlegende Zusammenspiel der aufgezeiten Einzelbausteine (vgl. Abbildung 10) ist identisch mit dem des funktionalen Systementwurfs.
Die Datei des technischen Systementwurfs kann hier gefunden werden.
Komponentenspezifikation
Für die Definition von Aufgaben, innerem Aufbau, Verhalten und anderen spezifischen Dingen ist die Komponentenspezifikation da. Hier werden sowohl Eingänge und Ausgänge definiert, als auch einzelne Bauteile der Komponenten spezifiziert. Somit kann der Roboter in verschiedene Elemente aufgeteilt werden. Es gibt zunächst einmal den Roboter selber mit seinen Versorgungs- und Kommunikationsanschlüssen, aber in der Baugruppe Roboter auch seinen einzeln aufzuführenden Greifer. Darüber hinaus gehören zu ihm die Untergruppen des Interface, des Netzteils, des Steuergeräts und der Teaching Box.
Auch das gesamte Stationsmodul wird in der Komponentenspezifikation in zwei Bereiche aufgeteilt. Das Roboter Handling beinhaltet die Punkte der Werkstückaufnahme und der am Roboter integrierten Sensorik. Dem Modul der Robotermontage hingegen werden die verschiedenen Magazine und die Rutsche zur Weitergabe an das Transferband zugeordnet. Als letzte Komponente steht noch die Schnittstelle zum menschlichen Bediener: Der PC. Hier wird einmal zwischen der Programmierumgebung CIROS Studio und dem eigentlichen Programmcode unterschieden und spezifiziert.
Ebenfalls der Programmablauf wird genau beschrieben. Jeder Bewegungsschritt und Abfragepunkt wird detailliert aufgeführt. Sind die Grundvoraussetzungen erfüllt, erkennt der Roboter das Werkstück in der Aufnahmeposition. Nachdem er dies nun gegriffen hat, legt er es in die Montagevorrichtung und prüft die Farbbeschaffenheit. Nach diesem Schritt wird über den Orientierungssensor geprüft, wo sich die Auskerbungen am Boden befinden. So wird gewährleistet, dass der Zentrierstift in der Montagevorrichtung richtig in den Grundkörper greift. Die Kolbenabholung erfolgt nach dem Einsetzen auf den Zentrierstift. Je nach Farbe des Werkstücks wird entweder ein großer oder ein kleiner Kolben aus der Magazinpalette abgeholt. Der zum Grundkörper passende Kolben wird nun eingesetzt. Der nächste Schritt ist nun die Abholung der Feder. Diese wird von der Aufnahmeposition am Magazin gegriffen und eingesetzt. War dieser Schritt erfolgreich, wird ein Deckel abgeholt. Dieser wird gegriffen und auf den vorgefertigten Zylinder gesetzt. Durch die bekannte Orientierung wird der Deckel passend verdreht und rastet ein. Der Zylinder ist komplett montiert. Als abschließender Schritt wird der Zylinder nun gegriffen und über die Rutsche an das Transferband weiter gegeben.
Als wichtige Einheit zum Verständnis der nachfolgenden Dokumentation dient die sogenannte Ria-Box. Dieses Modul zeigt alle Ein- und Ausgangssignale des Roboters an und dient somit als eine Art Verteiler. Im weiteren Verlauf ist in Abbildung 17 das Aussehen der Ria-Box zu sehen.
Die Dateien der Komponentenspezifikation können hier gefunden werden.
Programmierung
Die Programmierung ist der Schlüsselkomponente für alle Bewegungen und Abläufe des Roboters. In ihr werden neben den Programmschritten auch die Ein- und Ausgänge initialisiert. Über das Festo eigene Portal namens CIROS kann der Bediener über eine RS232-Schnittstelle eine Verbindung zum Roboter herstellen. Nach erfolgreichem Verbinden kann ein lauffähiges Programm auf den Roboter geladen werden. Ein kleines Handout zum CIROS-Programm inklusive einer ersten Anleitung zum Bespielen des Roboters kann hier gefunden werden.
Als Programmiersprache können entweder MELFA-BASIC IV oder MOVEMASTER COMMAND verwendet werden. Um die Funktionalität des Steuergerätes in vollem Umfang zu nutzen, sollte mit den MELFA-BASIC-IV-Befehlen gearbeitet werden. Als Ursprungsprogramm wurde das Programm 2 von Andreas Hopf gewählt. Dieses Programm beinhaltet ausschließlich die Steuerung des Roboters, die zur Montage eines Zylinders notwendig ist.
In der Projektdatei [1] befindet sich das komplette, lauffähige Programm inklusive der Positionsliste um einen Zylinder zu fertigen. Sowohl in der alten Programmsyntax, als auch in der Positionsliste mussten einige Änderungen vorgenommen werden. Die optimierten Teaching-Positionen können der Abbildung 13 entnommen werden. Die dort genannten Punkte können als Referenz für alle weiteren Programmierungen verwendet werden.
In der geschriebenen Syntax ist es ebenfalls wichtig, Vektoren oder Initialisierungen anzupassen. Da es im Programmabschnitt der Deckelmontage zu einigen Problemen kam, wurde der Vektor T30 auf 45 erhöht. Die vorher angegebene Größe von 30 reichte nicht aus, um den Deckel bei der Montage bis in die Verriegelung zu drehen. Nach der Anpassung konnte der Deckel erfolgreich montiert werden. (vgl. Abbildung 14)
Neben der Anpassung das Drehwinkels war es notwendig, die Initialisierung der Sensoren zu ändern. Mit welcher Bitziffer der jeweilige Sensor initialisiert werden muss, hängt von der Verdrahtung in der Ria-Box ab. Problem: Sobald Eingang 1 an dieser Box von 0 auf 1 schaltet, bleibt der Roboter sofort stehen und schaltet die Servomotoren aus. Aufgrund dessen wurde über eine neue Verdrahtung der Sensor der Farberkennung auf einen anderen Eingang gelegt. Dabei ist zu beachten, dass der gewählte Eingang auch in der Initalisierung (vgl.Abbildung 15) identisch mit der bei Ansprechen des Sensors aufleuchtenden Diode in der Ria-Box ist.
Die Aufteilung der Dioden kann hier nachgeschlagen werden. Die originale Verdrahtung und Belegung der Sensoren auf dieser Box ist im Handbuch auf Seite 30 aufgeführt. Laut diesem Dokument ist der Eingang 6 nicht belegt. In der mitgelieferten Programmierung wurde allerdings der Part-Available-Sensor zur Erkennung eines Werkstückes in der Startrutsche auf diesem Eingang initialisiert. Deshalb wurde auch hier die Verdrahtung verändert. Auf dem E/A-Terminal kann man durch Aufleuchten der Dioden testen, auf welchem Anschluss die jeweiligen Sensoren liegen. Dafür müssen die Sensoren lediglich einen Gegenstand detektieren. Spricht der Sensor an, so leuchtet die jeweilige Diode auf dem genannten Terminal inklusive dem dazugehörigen Eingangsbit auf der Ria-Box.
Die veränderten Bits sind:
- Sensor am Greifer (Farberkennung): BIT,12
- Sensor Orientierung (im Montagemodul): BIT,2 (wie im Original)
- Sensor Part-Available: BIT,10
Komponententest
Nachdem alle Verkabelungen und Verdrahtungen ordentlich verlegt wurden, folgte nun der Komponententest. In diesem Segment testet man die Funktion der einzelnen Komponenten. Durch die abgeschlossene Installation des CIROS-Programmes auf die neuen Betriebssysteme konnte in vollem Umfang mit dem Programm gearbeitet werden. Sowohl Computer als auch das Programm inklusive der Verbindung zum Roboter konnten somit einen erfolgreichen Komponententest vermelden.
Im Bereich des Montagemoduls musste der Sensor am Greifer justiert werden. Der Test zeigte, dass alle Sensoren funktionsfähig sind und ihre Detektion erfolgreich ausführen. Allein der Farberkennungssensor musste nachgestellt werden. Um eine zuverlässige Arbeit zu gewährleisten war es erforderlich, dass er bei den roten und silbernen Werkstücken anschlägt, bei den schwarzen Grundkörpern jedoch nicht. Durch Justieren des Sensors mit einem kleinen Schlitz-Schraubendreher (vgl. Abbildung 18) konnte dies so eingestellt werden. Die Druckluftzylinder zum Ausschieben der Federn und der Deckel waren ebenfalls intakt. Mithilfe der Möglichkeit, die Ventile über den blauen Schieber auf der Ventil-Oberseite zu verstellen, verfuhren die Zylinder in die jeweilige Endlage. Der Roboter konnte sein Programm durchlaufen und einen Zylinder fertigen. Da das Programm die Ansteuerung der Zylinder und der Bedientaster am Montagemodul nicht vorsieht, waren diese außer Funktion. Es muss also manuell sicher gestellt sein, dass jeweils eine Feder und ein Deckel sich in Abholposition befindet. Auch der Grundkörper muss von Hand in die Zuführrutsche gegeben werden. So ist es möglich, in Summe 8 Zylinder nacheinander automatisch durch den Roboter zu fertigen und der Nachfolgestation weiter zu geben.
Integrationstest
Wie in dem vorherigen Abschnitt beschrieben, bezieht sich das auf den Roboter geladene Programm ausschließlich auf die Ansteuerung des Roboters und nicht auf die gesamte Anlage. Dieser Grund lässt somit einen Integrationstest und alle nachfolgenden Testpunkte nicht zu.
Ergebnis
Das Endergebnis von zahlreichen Stunden und Bemühungen im Rahmen dieses Praktikums kann sich sehen lassen. Alle Fehlercodes des Roboters wurden beseitigt und gelöscht. Man kann den Roboter nun komplett von Hand oder voll automatisch verfahren. Die Montage eines Zylinders konnte realisiert werden. Ebenfalls die Anbindung an die Nachfolgestation wurde erfolgreich durchgeführt. Ordnerstrukturen, Dokumentationen und Unterlagen wurden strukturiert und übersichtlich geordnet. Alles was man für das Erreichen unseres Endstandes braucht steht in diesem Wiki-Artikel. Zur Visualisierung kann man die Montage eines Zylinders hier noch einmal sehen:
Info: Dieses Video ist vor der ordentlichen Kabelverlegung entstanden.
Ablaufbeschreibung:
1. Werkstück in Montageaufnahme -> Abholung des Werkstücks
2. Grundkörper in Montagevorrichtung legen und Farberkennung durchführen
3. Grundkörper aufnehmen und Orientierungsmessung durchführen
4. Grundkörper in Montagevorrichtung einsetzen (Zentrierstift muss in den vorgesehenen Stellen des Grundkörpers sitzen)
5. Abholung des richtigen Kolbens mit anschließender Montage
6. Abholung der Feder (vorhergehendes Prüfen, ob Feder sich an der Abholposition befindet)
7. Einsetzen der Feder
8. Abholung des Deckels (vorhergehendes Prüfen, ob der Deckel sich an der Abholposition befindet)
9. Orientierungsmessung des Deckels
10.Montage des Deckels (Nasen am Deckel müssen richtig in den Grundkörper packen)
11.Aufnahme des fertigen Zylinders und Weitergabe an die nächste Station
Problemdiagnose Input 1
Im Verlaufe dieses Artikels wurde auf den Fehler des Input 1 hingewiesen. Sobald auf diesem Eingangsbit Signal geschaltet wird, stoppt der Roboter mit seinem Programmdurchlauf und schaltet die Servos ab. Um die Ursache dieses Problems enger eingrenzen zu können, wurde ein einfaches Beispielprogramm geschrieben. Mit diesem Programm konnte sichergestellt werden, dass der Fehler nicht an der Programmier-Syntax liegt. Mithilfe der Positionsliste wurde einfach zwischen der Grundposition und der Abholposition des Grundkörpers verfahren. Ohne dass in dieser Programmierung ein Eingang initialisiert wurde, konnte trotzdem der Fehler bei Ansprechen des Input 1 beobachtet werden. Im Originalfall befindet sich auf diesem Eingang der Greifersensor zur Farberkennung. Allerdings erscheint der Fehler auch dann, wenn ein anderer Sensor auf diesen Input gelegt wird und Signal durchschaltet. Es liegt also definitiv am Input 1. Dies kann man optisch auf der Ria-Box beobachten. Sobald die LED von Input 1 aufleuchtet, wird Signal durchgeschaltet und der Roboter bleibt stehen. Die Originalbelegung aller Eingänge kann hier auf Seite 12 gefunden werden.
Des Weiteren wurden verschiedene Kabelbäume zwischen dem E/A-Terminal auf der Robotermontagestation und der Ria-Box eingebaut, um einen Fehler im Kabelbaum ausschließen zu können. Die Erkenntnis daraus ist, dass durch unterschiedliche Verpinnung im Stecker der Input 1 garnicht mehr erreicht werden kann. Daher wurde der Originalkabelbaum wieder eingebaut.
Ausblick
Um die volle Funktionalität dieser Station auszunutzen, muss ein lauffähiges Programm auf den Roboter gespielt werden, was nicht nur den Roboter, sondern auch die Magazine der Federn und der Deckel, sowie das Bedienfeld mit der Start- und Resettaste ansteuert. Das originale Programm, welches bei Auslieferung enthalten ist, kann hier gefunden werden. Um dies zu nutzen, muss die veränderte Verdrahtung der Sensoren wieder rückgängig gemacht werden, da alle Ein- und Ausgänge der Ria-Box benötigt werden. Weiterhin ist zu klären, warum der Roboter sich bei Ansprechen von Eingang 1 sofort ausschaltet.
Lessons Learned
- Projektplanung
- strukturierte Vorgehensweise nach V-Modell
- Roboter-Programmierung
- Projektdokumentation
Aufgaben für die Zukunft:
- Auslieferungsprogramm auf den Roboter laden und so abändern, dass keine Fehlercodes ausgegeben werden und das Programm lauffähig ist
- Abschaltung durch Signaleingang bei Input 1 beseitigen
- Verdrahtung wieder in den Originalzustand versetzen
- Integrations-, System- und Abnahmetest durchführen
Erweiterung um ein Akkumanagement-System
Motivation
Die Ziele hinter dem Akkumangement-System sind, die Ausfälle des Stromnetzes, welche durch verschiedene hochschulinterne Tests immer wieder zu erwarten sind, zu eliminieren. Um solche Situationen zu überbrücken, wurde eine Umschalteinrichtung zwischen Netzteil und Akku entwickelt. Das vorher verwendete Netzteil versorgt zwar die Positionssensoren dauerhaft mit Spannung und muss nicht ausgetauscht werden, wie die Batterie, aber aufgrund der Stromnetzabhängigkeit ist die Versorgung während der folgenden Ausfallsituationen nicht gegeben. Deswegen wurde ein intelligentes Akkumanagementsystem entwickelt.
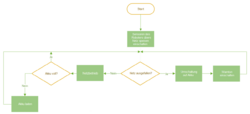
Als Ausfallsituationen sind folgende Ereignisse mit den dazugehörigen Ausfallzeiten zu erwarten:
- RCD-Test (1 Stunde)
- "Black-out-Tests" als hochschulinterne Stromabschaltung (3-4 Stunden)
- Stromausfall (15 Sekunden bis zur Betriebsbereitschaft des Diesel-Notstromaggregats)
Diese Akku-Management-Einheit soll im Netzbetrieb die Positionssensoren mit Spannung versorgen und den eingebauten Akku bei Bedarf, also nur im entladenden Zustand, laden. Fällt das Netz aus, soll automatisch auf Akkubetrieb umgeschaltet werden. Dabei gilt es eine verzögerungsfreie Umschaltung zu gewährleisten und nach außen eine akustische Warnung abzugeben (siehe Abb. 19). Diese soll dem Bediener aufzeigen, dass das Netz ausgefallen ist und die Positionssensoren jetzt nur noch eine begrenzte Zeit mit Spannung versorgt werden können, es sei denn, der Netz wird wieder aktiviert. Falls jemand den Stecker des Netzteils gezogen hat, ist die akustische Warnung ein Zeichen dafür, die Aktion sofort rückgängig zu machen.
Anforderungen zusammengefasst:
- Lückenlose Umschaltung zwischen Netz- und Akkubetrieb
- Aufladen des Akkus nur bei Bedarf
- Akkukapazität für mindestens vier Stunden
- Akku-Überwachung (Tiefentladeschutz, Überspannungsschutz, etc.)
- Ausgangsspannung: konstante 4,3V DC
- akustische Warnung bei Verlust der Netzspannung
Entwicklung der elektrotechnischen Einheit
Um die Anforderungen zu erfüllen wurde zuerst überlegt, wie so etwas kompakt, einfach und kostengünstig zu realisieren sein könnte. Dabei wurde entschieden, dass sich eine 5V-Ladeplatine in Kombination mit 3,7-Li-Ion-Akkus eignen würde (siehe Abb. 21 Mitte). Diese Ladeplatine sollte auch die Umschaltung zwischen Netz und Akku übernehmen. Des Weiteren sollte ein zweites Netzteil (das gleiche Schaltnetzteil), welches in einem zweiten Stromkreis mit einer anderen Fehlerstrom-Schutzeinrichtunng (RCD) betrieben wird, eingebaut werden. Dadurch können die Ausfallzeiten bei einem RCD-Test, die durch den Akku überbrückt werden würden, weiter verringert werden. Somit wird ein Netzteil an den "normalen" Stromkreis und das zweite an den EDV-Stromkreis (zu erkennen an den roten Steckdosen), siehe Abb. 20, angeschlossen. Mithilfe von zwei Schottky-Dioden (siehe Abb. 3 Dioden oben links), welche sich für den besonders geringen Spannungsabfall auszeichnen, wurde der Anschluss der beiden Netzteile ausgeführt. Die Pluspole der beiden Netzteile wurden über diese Schottky-Dioden zusammengeführt (siehe Abb. 21), die Minuspole können einfach miteinander verbunden werden. Durch den Einsatz der Dioden wird verhindert, dass die Spannung des einen Netzteils in das zweite Netzteil durchschlägt.
Die akustische Warnung erfolgt mit einem Summer, der über ein Relais geschaltet wird, zu sehen in Abb. 25. Dies Relais ist beim Netzbetrieb dauerhaft aktiviert und unterbricht dann den Stromkreis zum Summer. Fällt das Netz nun aus, fällt das Relais ab und schließt den Stromkreis. Der Summer wird nun über den Akku mit Spannung versorgt. Ein Versuchsaufbau auf dem Breadboard ist in Abb. 21 zu sehen.
Eine Herausforderung für das Gesamtsystem war die niedrige Spannung der nur zum Teil geladenen Akkus. Dies Ausgangsspannung der Ladeplatine sollte eigentlich konstante 4,2V DC betragen, doch bei entleerten Akkus fiel diese auf bis zu 3,5V DC ab. Um das Problem zu beheben kommt ein Step-up-Wandler (DC/DC-Wander) zum Einsatz, der die Spannung, unabhängig von der Eingangsspannung bis minimal 0,9V DC, wieder auf konstanten 5V DC anhebt. Im Anschluss sorgt eine Diodenschaltung (siehe Abb. 23) für einen Spannungsfall von 0,7V DC, sodass die angestrebten konstanten 4,3V DC dauerhaft erhalten bleiben.
Weiterhin sind verschiedene Kondensatoren zur Glättung und Pufferung der Ausgangsspannung verbaut worden. Um die Konnektivität zwischen den einzelnen Modulen Akku, Steuerplatine, Ein- und Ausgänge zu gewährleisten, wurden MKDSN-Klemmen (Schraubklemmen) in Kombination mit Aderleitungen verwendet. So lassen sich die Module schnell und einfach voneinander trennen und einzeln testen.
Im Folgenden sind der Testaufbau mit dem Summer auf dem Breadboard, sowie die erstellten Aufbau- und Lötpläne für die Steuerplatine dargestellt.
Strombedarf & Kapazitätsberechnung
Um die Stromausfälle zu überbrücken, wird auf den Akku umgeschaltet. Der Akku muss so dimensioniert sein, dass er mindestens vier Stunden die Positionssensoren und den Summer versorgen kann.
Strombedarf der einzelnen Bauteile:
- Positionssensoren Roboter: ca. 400 mA
- Summer: ca. 30 mA
Damit wird ein Gesamtstrombedarf von 430 mA gebraucht. Der Wirkungsgrad der Akkus (aufgrund von Alterung, Selbstentladung etc.) wird auf 0,8 geschätzt. Mithilfe der nachfolgenden Formel soll die minimale Akkukapazität berechnet werden.
Für das Akkumangement-System sollen zwei 3,7V Li-Ion Akkus mit je 2600 mAh zum Einsatz kommen. Mit diesen Werten soll die Laufzeit überprüft werden beziehungsweise berechnet werden, wie lange das System akkubetrieben laufen würde. Die Variable n steht hier für die Anzahl an Akkus.
Mit der verfügbaren Kapazität wird das entwickelte System die oben genannten Ausfallzeiten überstehen.
Durchführung des Integrations- und Systemtests
Nachdem die Komponententests erfolgreich waren, konnte der Integrationstest durchgeführt werden. Mithilfe eines Oszilloskops wurde die Umschaltzeit, sowie der Verlauf der Gleichspannung überprüft. Die Umschaltzeit war gleich null, d.h. ein Einbrechen der Spannung war nicht erkennbar. Außerdem ist die Gleichspannung, dank der Kondensatoren, nur noch leicht wellig, also ca. +/- 0,1 V DC. Daraufhin konnte die Steuerplatine noch obrigem Plan (Abbildung 22+24) gelötet werden. Diese Platine wurde anschließend mit den anderen Komponenten verdrahtet. Nun konnte der Systemtest, der in Abb. 24 dargestellt ist, durchgeführt werden. Dieser war erfolgreich, d.h. es wurden alle Anforderungen erfüllt. Im Folgenden konnten die verschiedenen Einheiten in das dafür konzipierte Gehäuse, welches im kommenden Kapitel vorgestellt wird, eingebaut werden.
Entwicklung der mechanischen Einheit
Die mechanische Einheit wurde entwickelt, um die Steuer- und Akkuplatine leichter zu "händeln". Beide Komponenten können so leicht transportiert und gelagert werden. Außerdem bietet das Gehäuse Schutz vor Staub und ähnlichen Einflüssen von außen. Das mit einem CAD-Programm erstellte 3D-Druck-Gehäuse hat einen zweistöckigen Aufbau. Im unteren Teil ist die Steuerplatine mit dem Relais untergebracht. Die Platine wird dort auf vier dafür vorgesehene Sockel geschraubt, um einen festen Sitz zu garantieren. An den Wänden befinden sich Stützen, auf die, eine mit einer Auskerbung versehene Mittelplatte, gelegt werden kann. Darüber wird die Akkueinheit untergebracht. Die Auskerbung der Mittelplatte ist für die Verbindungsleitungen zwischen Steuerplatine und Akku vorgesehen. Geschlossen wir der Kasten mit einem Deckel, der mit vier Schrauben befestigt werden kann. Zu Designzwecken wurde dieser mit dem HSHL-Logo versehen.
An den Seitenwänden des Kastens sind Kabelverschraubungen angebracht. Diese dienen als Zugentlastung und staubfreien Trennung für die Netzteil-Leitungen und die Versorgungsleitung der Positionssensoren. Im Ergebnis ist der Schaltkasten eine gute Möglichkeit, die entwickelte Schaltung fest montiert und kompakt zu bewegen und dieses Akkumanagement-System einzusetzen.
Ergebnis
Zusammenfassend ist die Funktion des Akkumanagement-Systems vollständig gegeben. Als letzten Schritt müsste dieses System von einer Folgegruppe noch an den Roboter angeschlossen und in Betrieb genommen werden.
Stückliste
Für die meisten nachfolgend aufgelisteten Bauteile gibt es unter dem angegebenen Link ein Datenblatt. Für die restlichen Bauteile ist jeweils ein Datenblatt im SVN abgelegt.
Artikel | Anzahl | Anbieter | Artikelbezeichnung | Einzelpreis | Link |
DEBO3 3.7LI 1.0A Entwicklerboards - Ladeplatine für 3,7V Li-Akkus, Micro-USB, 1A | 1 | Reichelt | DEBO3 3.7LI 1.0A | 1,85€ | https://www.reichelt.de/de/de/entwicklerboards-ladeplatine-fuer-3-7v-li-akkus-micro-usb-1a-debo3-3-7li-1-0a-p291401.html?trstct=pos_0&nbc=1&&r=1 |
AKKU 22703 Li-Ion-Akku, 18650, 3,7 V, 2600 mAh, inkl. MicroUSB Ladebuchse | 2 | Reichelt | AKKU 22703 | 9,99€ | https://www.reichelt.de/li-ion-akku-18650-3-7-v-2600-mah-inkl-microusb-ladebuchse-akku-22703-p277525.html?&trstct=pos_1&nbc=1 |
KEYSTONE 1049 Batteriehalter für 2x 18650 | 1 | Reichelt | KEYSTONE 1049 | 5,10€ | https://www.reichelt.de/batteriehalter-fuer-2x-18650-keystone-1049-p213372.html?&trstct=pos_8&nbc=1 |
1N 5817 Schottkydiode, 20 V, 1 A, DO-41 | 2 | Reichelt | 1N 5817 | 0,05€ | https://www.reichelt.de/schottkydiode-20-v-1-a-do-41-1n-5817-p41848.html?&trstct=pos_0&nbc=1 |
GOOBAY 59029 Universal-Schaltnetzteil, 3 - 12 V, 1500 mA | 2 | Reichelt | GOOBAY 59029 | 11,20€ | https://www.reichelt.de/universal-schaltnetzteil-3-12-v-1500-ma-goobay-59029-p312479.html?&trstct=pos_2&nbc=1 |
KEPO KPMB-G2345L1-K6440 Miniatur Summer | 1 | Conrad Electronics | 715020 - YD | 1,61€ | https://www.conrad.de/de/p/kepo-kpmb-g2345l1-k6440-miniatur-summer-geraeusch-entwicklung-70-db-spannung-4-5-v-dauerton-1-st-715020.html |
2x USB Step Up Spannungsregler DC 0.9-5V auf 5V 600mA Boost Converter Modul | 1 | ebay | - | 3,95€ | https://www.ebay.de/itm/353437318551 |
1 Kanal Relais Relai 5V/230V Raspberry Pi Modul Channel Relay Arduino ESP8266 DI | 1 | ebay | - | 3,80€ | https://www.ebay.de/itm/154734331033?hash=item2406e28499:g:x8sAAOSwLvRhrJwm |
MKDSN-Klemmen, Kabelverschraubungen, Streifenrasterplatine, Schrauben, 3D-Druck, Kondensatoren, Gleichrichterdioden, Kabelbrücken | k.A. | HSHL | - | - | - |
Literatur
- ↑ https://wiki.hshl.de/wiki/index.php/Ampel-Demonstrator/ V-Modell Projekt Ampeldemonstrator
- ↑ https://svn.hshl.de/svn/MTR_GPE_Praktikum/trunk/Fachthemen/MPS_Anlage/Modul%205%20Roboter/Datenblaetter/034035_EA_Terminal.pdf/ Datenbatt E/A-Terminal
- ↑ https://svn.hshl.de/svn/MTR_GPE_Praktikum/trunk/Fachthemen/MPS_Anlage/Modul%205%20Roboter/Bedienungsanleitungen/665122_Roboter_Anschaltbox.pdf/Bedienungsanleitung Ria-Box
- ↑ Datei: Datei:Programmablaufplan Akkumanagment.zip
- ↑ Datei: Datei:Technischer Systementwurf Akkumanagement.pptx (Originaldatei)
- ↑ Datei: Datei:Akkumangement Breadboard Fritzing.fzz (Originaldatei)
- ↑ Datei: Datei:Akkumangement Streifenrasterplatine Fritzing.fzz (Originaldatei)
- ↑ Datei: Datei:Aufbau des Systemtests.pptx (Originaldatei)
- ↑ Hochspringen nach: 9,0 9,1 Datei: Datei:CAD-Files Schaltkasten Akkumanagement.zip (Originaldateien)