Mechatronisches Produktionssystem zur Produktion eines HSHL-Getränkeuntersetzers
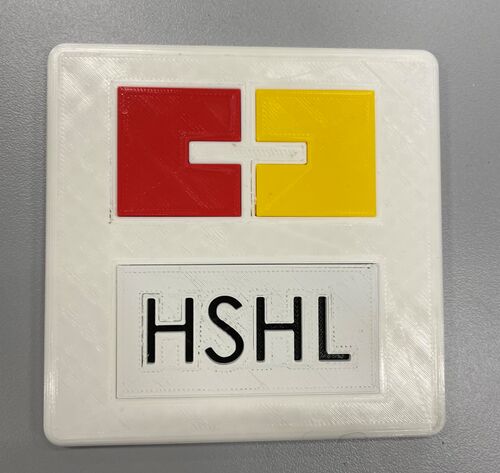
Dozent: Prof. Dr. Mirek Göbel
→ zurück zur Übersicht: Praktikum Produktionstechnik
Einleitung
Im Rahmen des Studiengangs Mechatronik der Hochschule Hamm-Lippstadt wird im 7. Fachsemester das Praktikum "Produktionstechnik", als Teil des Moduls "Global Production Engineering", durchgeführt. In diesem Praktikum geht es um die Realisierung eines mechatronischen Produktionssystems (MPS) mittels Speicher Programmierbarer Steuerung (SPS), sowie der Ansteuerung eines pneumatischen Systems für die Herstellung eines HSHL-Geträkeuntersetzers, der als Werbegeschenk genutzt werden könnte. Einige Stickpunkte wurden bereits vor der Umsetzung formuliert. Das Projekt sollte nachhaltig sein, Weiterentwicklungs-Möglichkeiten für nachfolgende Semester sollten vorgenommen werden können, das System soll auf vier Stationen aufteilbar sein und die Nutzung des vorhandenen Förderbands der MPS-Anlage als gemeinsame Schnittstelle ist Pflicht.
Gesamtkonzept
Die Produktion von HSHL-Getränkeuntersetzen als Werbegeschenk soll in vier Stationen vorgenommen.
Die Stationen sind über das bereits bestehende Förderband der MPS-Anlage miteinander verbunden. Die Stationen werden von den Teams, mit je zwei Teammitgliedern, entwickelt und aufgebaut. Das Zusammenspiel der Stationen liegt im Vordergrund und muss stets abgestimmt werden. Ziel des Praktikums ist es, den Untersetzer in den vier Stationen zu fertigen. Das Foto zeigt einen fertigen Untersetzer, der das Ausgangsprodukt der MPS-Anlage ist. Die Einzelteile wurden mit einem 3D-Drucker gedruckt.
Die vier Stationen sind folgende:
- Station 1: Kommissionierung
- Station 2: Schweißen
- Station 3: Montage
- Station 4: Auswerfen. Die Ansteuerung erfolgt über die Förderbandanlage. In der Vergangenheit war eine Station Verpackung geplant.
Datei:Planung des Gesamtkonzeptes.pptx
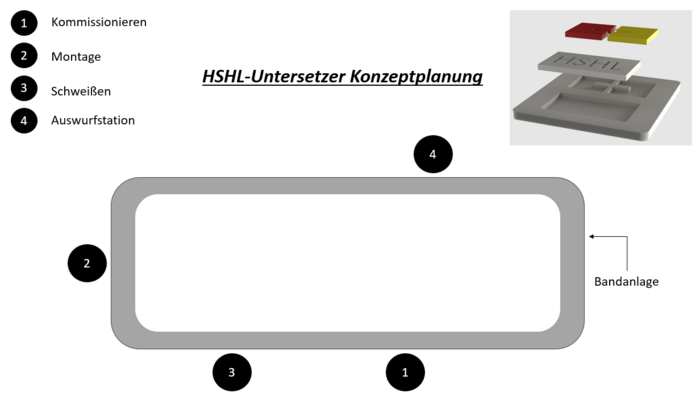
Gesamtkonzept der MPS-Anlage
Für die Kommunikation zwischen den Stationen und dem Förderband wird die SPS-Zentrale (MPS 500) verwendet. Abbildung 4 zeigt das das Konzept der MPS-Anlage.
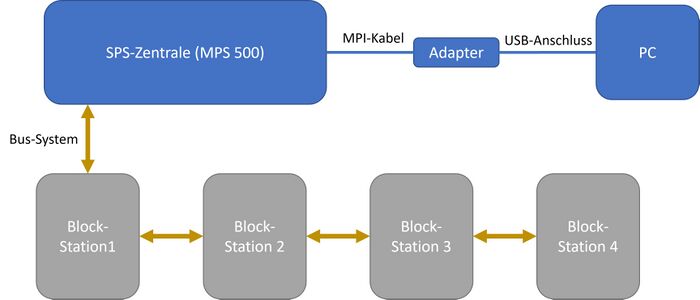
Auf der Abbildung ist zu sehen, dass die Informationsübertragung zwischen allen Stationen und SPS über ein Bussystem geschieht. Die SPS lässt sich mit dem Computer einen Adapter ansteuern. Block-Stationen 1 bis 4 beinhalten mehrere Module für die Steuerung der Aus- und Eingänge. Dies ist in der Abbildung 5 zu sehen.
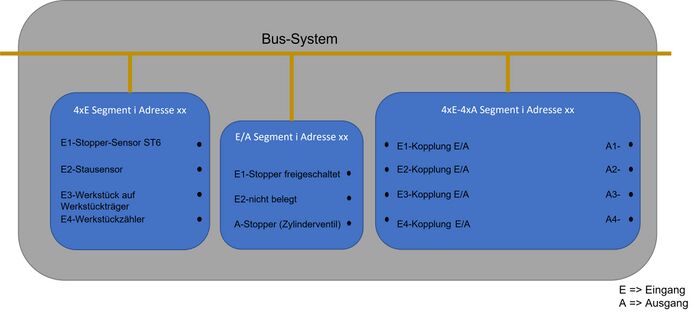
In jedem Block befinden sich drei Module. Das 4xE Segment für die Station i mit der Adresse xx ist für Eingänge geeignet. Es nimmt die Signale von den Sensoren und leitet die zur SPS über das Bussystem weiter. Die Signale werden in SPS bearbeitet und je nach Bedarf werden an E/A Segment oder an 4xE-4xA Segment wieder gesendet. E/A Segment ist für Steuerung des Druckluftzylinders geeignet, der den Schlitten auf dem Förderband hält. Das E/A Segment hat auch zwei Eingänge. Einer davon ist für die Erkennung vom Zustand des Zylinderkolbens. Das 4xE-4xA Segment hat vier Eingänge und vier Ausgänge. Diese sind Geräte außerhalb des Systems MPS 500 (z.B. ET 200SP). Weitere Informationen über MPS 500-Architektur finden Sie hier.
Bandanlage:
Die Bandanlage ist für den Transport der Werkstückträger zwischen den Stationen verantwortlich. An dem Förderband sind 6 verschiedene Stationen vorhanden, die gegen den Uhrzeigersinn nummeriert sind. Für das aktuelle Projekt werden 4 Stationen verwendet. Die einzelnen Bearbeitungsschritte sind nach der Bearbeitungsreihenfolge nummeriert und stimmen damit nicht mit den verwendeten Stationen an dem Förderband überein. Zusätzlich erfolgt die Ansteuerung der Station 4 zum Auswerfen der Untersetzer über die Förderbandanlage.
An den einzelnen Stationen werden die Werkstückträger über pneumatische Zylinder gestoppt. Zudem befinden sich an jeder Station induktive Sensoren, die für die Programmierung verwendet werden können. Für den richtigen Produktionsablauf werden die Stationen in der Reihenfolge Kommissionierung, Montage, Schweißen und Auswerfen bearbeitet werden. An der Bandanlage sind dies die Stationen 2, 6, 1 und 4. Somit müssen die Stationen teilweise ohne Bearbeitung durchlaufen werden, während an den richtigen Stationen ein Stopp zur Bearbeitung erfolgen muss. Mit den Stationen findet dabei eine Kommunikation statt, damit diese wissen, wann die Bearbeitung erfolgen kann und auf der anderen Seite benötigt die Bandanlage ein Signal, wenn die Bearbeitung abgeschlossen ist.
Kommissionierung:
Die Station der Kommissionierung schiebt die 3 Einlegebauteile und die Grundplatte des HSHL Untersetzers mit Hilfe einer SPS Steuerung, Druckluft und vier einfachrückwirkenden Pneumatikzylindern auf die Grundplatte für den Werkstückträger. Diese Grundplatte wird dann nachdem Bestücken mit einem zwifachwirkenden Pneumatikzylinder auf den Werkstückträger geschoben.
Schweißen:
Die Station des Schweißens verbindet die Einlegebauteile stoffschlüssig mit der Grundplatte. Der Mitsubishi Melfa Roboter sorgt durch die Führung eines Heißluftlötkolben dafür, dass entlang der Kontur der Bauteile eine Schmelze entstehen kann und so die Verbindung entsteht. Passend zu dem Untersetzer wird so der technische Zusammenhang und eine wasserdichte Lösung geboten. Das Schweißprogramm wurde per Teach-Verfahren dem Roboter einprogrammiert und kann automatisiert abgefahren werden. Auf Basis von Parameter-Tests wurden die Schweißproben auf Festigkeit, Optik und Wasserdichtigkeit ausgiebig getestet und somit die technisch besten Parameter hinsichtlich Temperatur und 3D Druck Füllrate ausfindig gemacht.
Montage:
Die Montagestation besteht aus einem 4 Achsenroboter, einer SPS und einer Basler-Kamera. An dem 4 Achsenroboter ist ein Vakuumsaugreifer befestigt. Der Roboter wird mit der Programmiersprache V+ von ACE Omron programmiert. Die Montagestation bestückt die Grundplatte des HSHL Untersetzers mit den 3 Einlegebauteilen. Die Basler-Kamera kann zur visuellen Kontrolle des Montageprozesses und gegebenfalls zur Montage auf dem bewegten Belt genutzt werden. Allerdings konnten diese Funktionen nicht programmiert werden, da die Kamerakalibrierung nicht abgeschlossen werden konnte.