Modulares mechatronisches Produktionssystem (MPS): Förderband
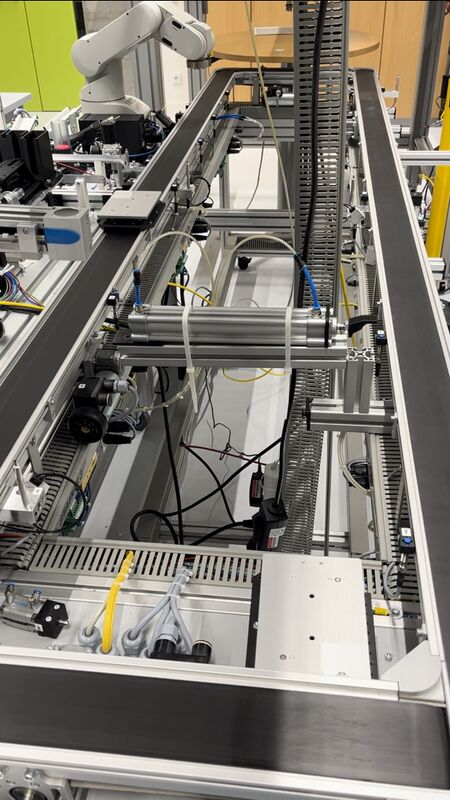
Betreuer: Prof. Dr.-Ing. Göbel
→ zurück zur Übersicht: Praktikum Produktionstechnik
Einleitung
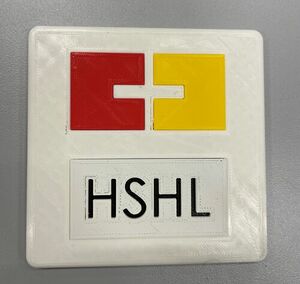
Im Rahmen des Studiengangs Mechatronik (MTR) an der Hochschule Hamm-Lippstadt wird im siebten Fachsemester das Praktikum Produktionstechnik durchgeführt. Das Praktikum ist Teil des Schwerpunktes Global Production Engineering. In dem Praktikum geht es darum den Studierenden anhand von kleinen Projekten die Möglichkeit zu bieten, das bisher Erlernte in der Praxis umzusetzen. Die hier geforderten Fähigkeiten erstrecken sich über die Konstruktion von Bauteilen und die Umsetzung dieser mittels 3D-Druck bis hin zur Programmierung von speicherprogrammierbaren Steuerungen (SPS) und dem Erstellen von elektrischen und pneumatischen Schaltplänen. In dem hier vorliegenden Artikel soll sich mit dem modularen Produktionssystem (MPS) (vgl. Abbildung 1) beschäftigt werden. Dabei wird der Fokus auf das Förderband und dessen Aufgabe gelegt.
Gesamtkonzept
Bei dem MPS handelt es sich um eine Produktionsanlage, die aus mehreren Stationen besteht. Das Gesamtkonzept ist auf der Seite Mechatronisches Produktionssystem zur Produktion eines HSHL-Getränkeuntersetzers genauer beschrieben. Als Station 0 wird das Förderband bezeichnet. Insgesamt gibt es sechs verschiedene Stationen. Die Produktionsanlage wurde ursprünglich dafür verwendet, um kleine Zylinder mit verschiedenfarbigen Kappen zu bestücken und anschließend zu sortieren. Die MPS-Anlage soll aktuell dafür verwendet werden, um HSHL-Getränkeuntersetzer (vgl. Abbilung 2) zu produzieren. Die Untersetzer sollen als Werbegeschenke dienen und werden von vier Stationen hergestellt und mit dem Förderband zwischen den einzelnen Stationen transportiert.
Die 6 verschiedene Stationen an dem Förderband sind gegen den Uhrzeigersinn nummeriert. Für das aktuelle Projekt werden 4 Stationen verwendet. Die einzelnen Bearbeitungsschritte sind nach der Bearbeitungsreihenfolge nummeriert und stimmen damit nicht mit den verwendeten Stationen an dem Förderband überein. Zusätzlich erfolgt die Ansteuerung der Station 4 zum Auswerfen der Untersetzer über die Förderbandanlage.
Station | Ursprungsstation | Aktuelle Station | Link |
---|---|---|---|
1 | Verpackung | Schweißen | Produktion eines HSHL-Getränkeuntersetzers: Schweißen (Station 2) |
2 | Kommisionieren | Kommisionieren | Produktion eines HSHL-Getränkeuntersetzers: Kommissionierung (Station 1) |
3 | Kleben | nicht verwendet | |
4 | nicht verwendet | Auswerfen der Untersetzer | |
5 | nicht verwendet | nicht verwendet | |
6 | Montage | Montage | Produktion eines HSHL-Getränkeuntersetzers: Montage (Station 3) |
Produktion eines HSHL-Getränkeuntersetzers
Die Produktion des Untersetzers erfolgt an den vier Stationen Kommissionierung, Montage, Schweißen und Auswerfen. Die Stationen sind im Kreis um das Förderband angeordnet und werden gegen den Uhrzeigersinn abgearbeitet. Dabei werden die Stationen teilweise ohne Bearbeitung durchfahren, damit diese in der richtigen Reihenfolge erfolgt. Das Zusammenspiel der Stationen steht im Vordergrund und soll stets abgestimmt werden.
Aufgabe der Station
Das Förderband hat die Aufgabe, die Werkstückträger zwischen den einzelnen Stationen zu transportieren. Außerdem müssen die Werkstückträger über pneumatische Zylinder an den einzelnen Stationen gestoppt werden. Dazu befinden sich an jeder Station induktive Sensoren, die für die Programmierung verwendet werden können. Für den richtigen Produktionsablauf müssen die Station in der Reihenfolge Kommissionierung, Montage, Schweißen und Auswerfen bearbeitet werden. An der Bandanlage sind dies die Stationen 2, 6, 1 und 4. Somit müssen die Stationen teilweise ohne Bearbeitung durchlaufen werden, während an den richtigen Stationen ein Stopp zur Bearbeitung erfolgen muss. Mit den Stationen muss eine Kommunikation stattfinden, damit diese wissen wann die Bearbeitung erfolgen kann und auf der anderen Seite benötigt die Bandanlage ein Signal, wenn die Bearbeitung abgeschlossen ist.
Diese Anforderung soll realisiert werden, indem ein neues Programm für die speicherprogrammierbare Steuerung im TIA-Portal(Totally Integratet Automation-Portal) erstellt wird. Bei dem Programm TIA-Portal handelt es sich ein Programm der Firma Siemens, mit deren Hilfe eine SPS programmiert werden kann. Zudem kann eine Verbindung vom Computer zur SPS hergestellt werden und so eine Fehlersuche im Programm durchgeführt werden.
Vorgehen nach V-Modell
Um die oben genannten Anforderungen umzusetzen, wird nach dem V-Modell gearbeitet und vorgegangen. Dieses Modell wird verwendet, um dem Benutzer bei der Organisation und Durchführung des Projektes zu helfen. Dabei wird das lineare Vorgehen der einzelnen Projektphasen visualisiert. Das V-Modell beginnt mit den Anforderungen an das Projekt und führt den Nutzer bis zum Abnahmetest, welcher den Abschluss des Projektes kennzeichnet. Die einzelnen Schritte des absteigenden Pfades sind mit den gegenübergestellten Schritten des aufsteigenden Pfeils verknüpft und stellen den Zusammenhang der einzelnen Schritte da.
Anforderungsdefinition
Die Anforderungsdefinition ist dafür da, um die einzelnen Aufgaben innerhalb des Projektes festzulegen und einen Überblick zu erhalten. Zudem werden die einzelnen Aufgaben anhand der zuvor definierten Anforderungen spezifiziert und konkretisiert.
ID | Typ | Kapitel | Inhalt | Status | Ersteller | Datum |
---|---|---|---|---|---|---|
0 | I | 0 | Aufgabenstellung | |||
0 | Austausch der SPS-300 Steuerung des Förderbands durch eine moderne ET 200 SP Steuerung und Bedienung derselben über ein HMI. | Abgeschlossen | Bastian Hannappel | 09.01.2025 | ||
1 | I | 1 | In Thema einarbeiten | |||
2 | I | Funktionsweise des Systems nachvollziehen | Abgeschlossen | Bastian Hannappel | 10.10.2024 | |
3 | I | Programm im TIA Portal nachvollziehen & zu Programmierung von ET200SP im TIA Portal informieren | Abgeschlossen | Bastian Hannappel | 07.11.2024 | |
4 | I | Die ASI-Bus Funktionsweise verstehen | Abgeschlossen | Bastian Hannappel | 10.10.2024 | |
5 | I | Die Funktionsweise der Simatic ET200SP verstehen | Abgeschlossen | Bastian Hannappel | 07.11.2024 | |
6 | I | 2 | SPS-300 auf Simatic ET 200SP Updaten | |||
7 | I | Programm auf Testboard für ET 200SP testen | Abgeschlossen | Bastian Hannappel | 14.11.2024 | |
8 | A | Die SPS-300 ausbauen und dabei Leitungen beschriften | Abgeschlossen | Bastian Hannappel | 14.11.2024 | |
9 | A | Die ET 200SP einbauen, verdrahten & anschließen | Abgeschlossen | Bastian Hannappel | 14.11.2024 | |
10 | I | 3 | Software / Programmierung | |||
11 | A | Das Bestehendes Programm für ET200SP adaptieren | Abgeschlossen | Bastian Hannappel | 21.11.2024 | |
12 | A | Das Programm auf ET200SP Laden | Abgeschlossen | Bastian Hannappel | 21.11.2024 | |
13 | A | Die Funktionsweise testen und in Betrieb nehmen | Abgeschlossen | Bastian Hannappel | 19.12.2024 | |
14 | A | Falls nötig: Funktionsweise erweitern | Abgeschlossen | Bastian Hannappel | 19.12.2024 | |
15 | A | 4 | HMI Programmieren und in Anlage Implementieren | |||
16 | I | Mit bereits vorhandenen HMI-Dateien im Ordner auseinander setzen | Abgeschlossen | Bastian Hannappel | 12.12.2024 | |
17 | I | Dokumentation der verwendeten HMI nachvollziehen | Abgeschlossen | Bastian Hannappel | 07.11.2024 | |
18 | A | Entwicklung/Programmierung im TIA Portal | Abgeschlossen | Bastian Hannappel | 19.12.2024 | |
19 | A | Implementierung auf Gesamtanlage | Abgeschlossen | Bastian Hannappel | 19.12.2024 | |
20 | A | Inbetriebnahme der gesamten Anlage muss fehlerfrei erfolgen | Abgeschlossen | Bastian Hannappel | 19.12.2024 | |
21 | A | Eine Halterung für HMI herstellen | Nicht mehr realisierbar | Bastian Hannappel | ||
22 | I | 5 | Dokumentation | |||
23 | A | Vorhandene Dokumente müssen gesichtet und ggf. aktualisiert werden | Abgeschlossen | Bastian Hannappel | 09.01.2025 | |
24 | A | Das Wiki muss gepflegt und aktualisiert | Abgeschlossen | Bastian Hannappel | 09.01.2025 | |
25 | A | Dokumentation der Schnittstellen und weiterer relevanter Informationen muss erfolgen | Abgeschlossen | Bastian Hannappel | 09.01.2025 | |
26 | A | Tätigkeitsbericht muss regelmäßig gepflegt werden | Fortlaufend | Bastian Hannappel | Fortlaufend |
Legende bei Typ: I = Info, A = Anforderung
Funktionaler Systementwurf
Im funktionalen Sytsementwurf werden die einzelnen Schnittstellen visualisiert und ihre Beziehungen dargestellt. Dies hilft zu Beginn des Projektes einen Überblick zu erhalten und Ordnung in den Aufbau zu bringen (vgl. Abbildung 4). Zusätzlich erleichtert es das weitere Vorgehen.

Technischer Systementwurf
Der technische Systementwurf (vgl. Abbildung 5) spezifiziert das Layout der Anlage und zeigt alle Schnittstellen auf. Zudem dient er als Gesamtübersich für die Anordnung der einzelnen Bauteile, wie zum Beispiel Stopper oder Lichtschranke. Zusätzlich werden die Schnittstellen genauer definiert, wie beispielsweise die Verbindung zu den einzelnen Stationen.
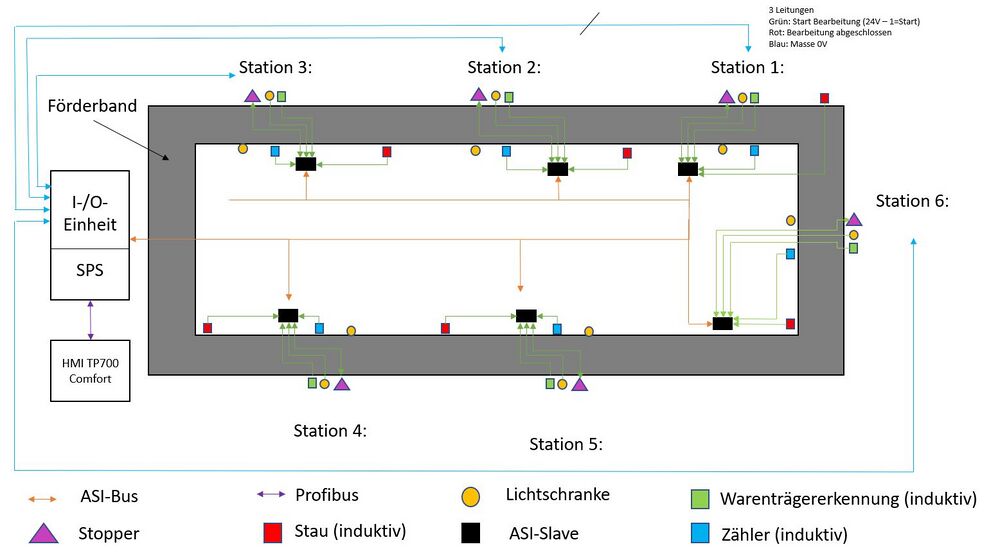
Komponentenspezifilation
In der Komponentenspezifikation befindet sich eine Variablentabelle mit allen Ein- und Ausgangsadressen der SPS. Die Ein- und Ausgänge, die über den ASI-BUS verbunden sind, werden im Programm wie normale Ein- und Ausgänge behandelt. Das ASI-Modul bekommt wie eine normale Ein- und Ausgangsbaugruppe einen Adressbereich.
AS-i Adresse | Operand | Betriebsmittel-kennzeichnung | Kommentar | |
---|---|---|---|---|
Eingänge ASI | ||||
2 | I3.4 | -10B1 | Werkstückträger Station 1 | |
2 | I3.5 | -10B2 | Stau Station 1 | |
2 | I3.6 | -10B3 | Lichtschranke Station 1 | |
2 | I3.7 | -10B4 | Zähler Station 1 | |
5 | I4.0 | -20B1 | Werkstückträger Station 2 | |
5 | I4.1 | -20B2 | Stau Station 2 | |
5 | I4.2 | -20B3 | Lichtschranke Station 2 | |
5 | I4.3 | -20B4 | Zähler Station 2 | |
8 | I6.4 | -30B1 | Werkstückträger Station 3 | |
8 | I6.5 | -30B2 | Stau Station 3 | |
8 | I6.6 | -30B3 | Lichtschranke Station 3 | |
8 | I6.7 | -30B4 | Zähler Station 3 | |
11 | I7.0 | -40B1 | Werkstückträger Station 4 | |
11 | I7.1 | -40B2 | Stau Station 4 | |
11 | I7.2 | -40B3 | Lichtschranke Station 4 | |
11 | I7.3 | -40B4 | Zähler Station 4 | |
14 | I9.4 | -50B1 | Werkstückträger Station 5 | |
14 | I9.5 | -50B2 | Stau Station 5 | |
14 | I9.6 | -50B3 | Lichtschranke Station 5 | |
14 | I9.7 | -50B4 | Zähler Station 5 | |
17 | I10.0 | -60B1 | Werkstückträger Station 6 | |
17 | I10.1 | -60B2 | Stau Station 6 | |
17 | I10.2 | -60B3 | Lichtschranke Station 6 | |
17 | I10.3 | -60B4 | Zähler Station 6 | |
Eingänge | ||||
I0.0 | Automatik Start | |||
I0.1 | Autoamtik Stopp | |||
I0.2 | Station 2 fertig (rote Leitung) | |||
I0.3 | Station 3 fertig (rote Leitung) | |||
I0.4 | Station 6 fertig (rote Leitung) | |||
I0.5 | 24 V | |||
I0.6 | Controller ON | |||
I0.7 | Station 1 fertig (rote Leitung) | |||
Ausgänge ASI | ||||
3 | Q3.0 | -10B5 | Stopper Station 1 | |
6 | Q5.4 | -20B5 | Stopper Station 2 | |
9 | Q6.0 | -30B5 | Stopper Station 3, verwendet für Auswerfzylinder Station 4 | |
12 | Q8.4 | -40B5 | Stopper Station 4 | |
15 | Q9.0 | -50B5 | Stopper Station 5 | |
18 | Q11.4 | -60B5 | Stopper Station 6 | |
Ausgänge | ||||
Q0.0 | -SH4 | Licht Automatik Ein | ||
Q0.1 | -SH5 | Licht Automatik Aus | ||
Q0.2 | Startfreigabe Station 2 (grüne Leitung) | |||
Q0.3 | -H1 | Fehler | ||
Q0.4 | Startfreigabe Station 3 (grüne Leitung) | |||
Q0.5 | Startfreigabe Station 6 (grüne Leitung) | |||
Q0.6 | Startfreigabe Station 1 (grüne Leitung) | |||
Q0.7 | Motor EIN |
Außerdem wurde in der Komponentenspezifikation ein Programmablaufplan für das Förderband erstellt, um die anschließende Programmierung zu vereinfachen. Dazu wurde ein genereller Ablauf erstellt (siehe Abbildung 6), sowie ein Ablaufplan für den jeweiligen Stationsablauf an den einzelnen Stationen (siehe Abbildung 7). Dieser ist an allen Stationen identisch.
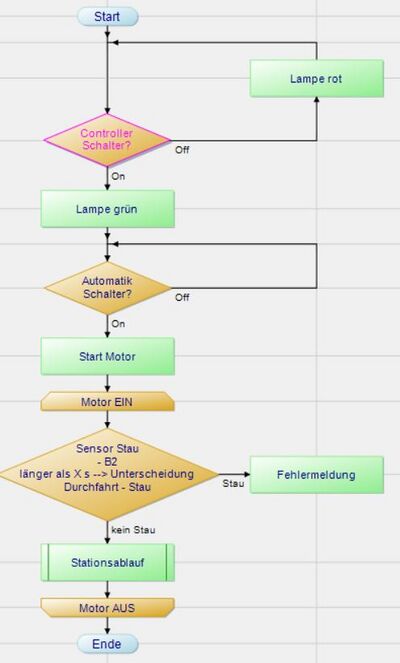
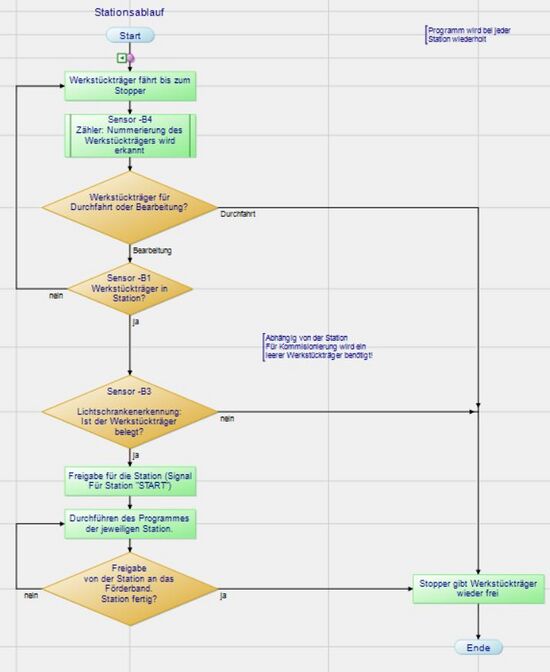
Programmierung
Als Ausgangszustand war eine SPS300 in der Anlage verbaut, welche durch eine ET200SP ausgetauscht wurde. Da beide im TIA Portal projektiert werden, konnten die Programminhalte weitesgehend übernommen werden. Um das Förderband zu steuern, wird auf eine Siemens ET200SP CPU1515 und ein ASI-Modul mit dem CM AS-i Master ST_1 zurückgegriffen. Nach einer Gerätekonfiguration wurde die SPS über die Ethernet-Schnittstelle mit dem PC verbunden. Die SPS wurde im TIA-Portal Projektiert. Eine Schritt für Schritt Anleitung für die Projektierung wurde ebenfalls im Praktikum erstellt und ist hier zu finden: Siemens SPS ET200SP CPU1515SP PC2 und HMI TP700 Comfort - Projekt erstellen - Schritt fuer Schritt
Anschließend wurden alle Schnittstellen, wie die ASI-Kommunikation und alle anderen Ein- und Ausgänge angelegt und getestet. Nachdem alle Schnittstellen eingerichtet waren und auf ihre Funktion überprüft wurden, wurden die Programmbausteine aus dem alten Programm übernommen (siehe Abbildung 8).
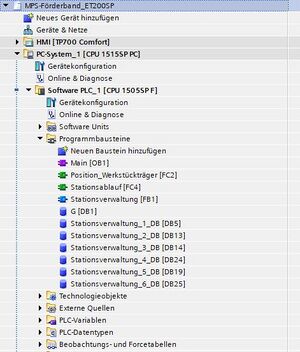
Die Programmstruktur startet mit dem Main Baustein, dazu gehört das Ansteuern des Motors und die Aufrufe der weiteren Funktionen. Darüber hinaus verfügt jede Station über eine eigene Funktion. Über diese ruft jede Station die Funktionen "Position_Werkstückträger" und "Stationsverwaltung" auf. Dadurch müssen zum Beispiel Änderungen bei dem Stationsablauf nur in der einen Funktion geändert werden und nicht in jeder der Funktionen der Stationen.
Alle Daten, die in dem Projekt verwendet werden, sind in einem globalen Datenbaustein "G" angelegt (siehe Abbildung 9 und 10). Dazu wurden für die Daten spezielle Datentypen angelegt. Durch diese Datentypen kann ein einheitliches System erzeugt werden und Änderungen müssen erneut nur an einer Stelle, nämlich bei dem Datentyp, durchgeführt werden.

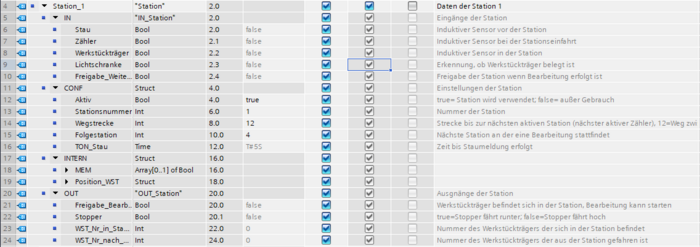
Die Station Förderband kann für die Programmierung in die einzelnen Stationen aufgeteilt werden. Jede Station ist für die Funktionsweise des Förderbandes identisch, da dieses die Werkstückträger liefert, die Signale zur Bearbeitung an die Station sendet und anschließend den Werkstückträger weiterfahren lässt. Dadurch ergibt sich, dass der Ablauf bei jeder Station derselbe ist und sich nur in der Bezeichnung der verwendeten Variablen unterscheidet. Lediglich Station 4 stellt eine Ausnahme dar, da an dieser der Auswurfzylinder angesteuert wird. Die Ansteuerung erfolgt in der Hardware über den Stopper-Zylinder der Station 3, dessen Pneumatikleitungen an den Auswurfzylinder angeschlossen sind.
Der Ablauf bei einer Station sieht exemplarisch so aus:
- Werkstückträger befindet sich in Bewegung auf dem Förderband und bewegt sich auf Station zu
- Zähler der Station erkennt Nummer des Werkstückträgers
- Programm erkennt, ob Bearbeitung in der Station stattfinden soll
- Werkstückträger wird durch Stopper-Zylinder an der Station angehalten oder durchgelassen
- Bei Bearbeitung: Signalweitergabe an die Station, für Start der Bearbeitung
- Warten auf Signal von Station, dass Bearbeitung abgeschlossen ist
- Erhalt des Signals, danach Einfahren des Stopper-Zylinders
- Weiterfahrt des Werkstückträgers
- Ausfahren des Stopper-Zylinders, damit der nächste Werkstückträger gestoppt werden kann
Zusatz: Sollte ein Stau innerhalb der Anlage erkannt werden, so wird zur Warnung das entsprechende Bit aus Abbildung 9 gesetzt.
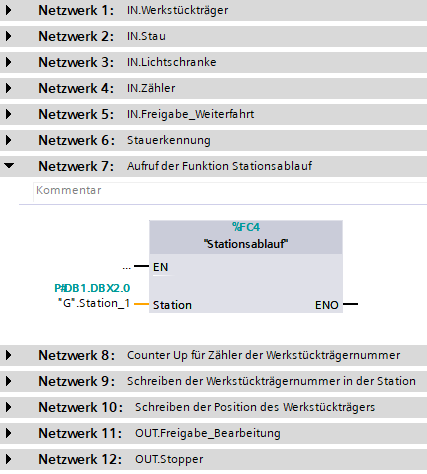
In der Funktion jeder Station wird der allgemeine Stationsablauf aufgerufen (siehe Abbildung 11).
Außerdem befinden sich in den Stationen die Verarbeitung der Ein- und Ausgänge, die Stauerkennung und 3 Netzwerke für die Erkennung der Werkstückträgernummer und das Schreiben der Position.
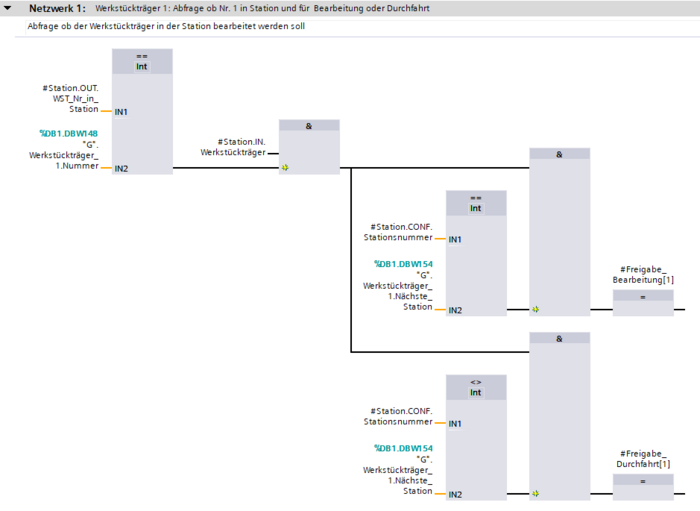
In dem Netzwerk 1 des Stationsablaufs findet die Abfrage statt, ob der Werkstückträger in der jeweiligen Stationen bearbeitet wird oder ob dieser durch die Station durchfährt (siehe Abbildung 12). Die gleiche Programmierung gibt es für den Werkstückträger 2 und 3 in identischer Form in Netzwerk 2 und 3.
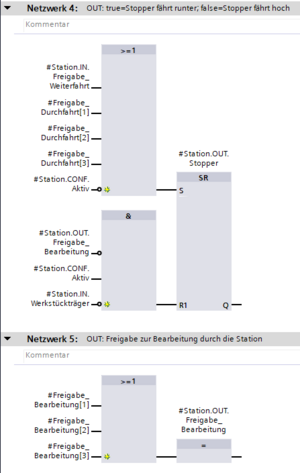
In dem Netzwerk 4 des Stationsablaufs wird der Stopper-Zylinder der jeweiligen Station gesteuert (siehe Abbildung 13). Das Netzwerk 5 gibt die Freigabe für die Station zur Bearbeitung.
Programmierung HMI
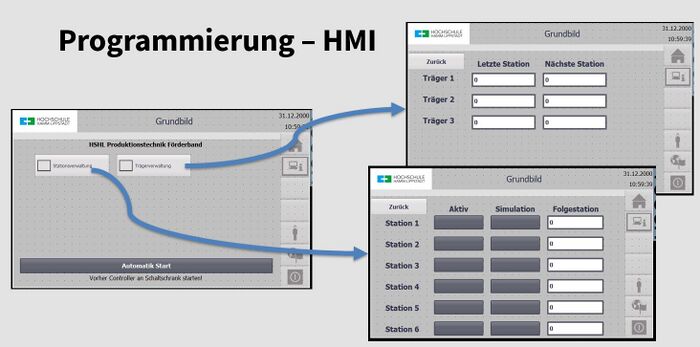
Um die Bedienung der Anlage zu vereinfachen und dem Bediener einen aktuellen Überblick zu ermöglichen, wurde eine HMI TP700 Comfort von Siemens installiert. Diese Mensch-Maschine-Schnittstelle (HMI) ist via Profinet mit der SPS (Speicherprogrammierbare Steuerung) vernetzt. Auf dem Startbildschirm der HMI, auch Hauptbildschirm genannt, kann der Automatikmodus aktiviert und zu verschiedenen Unterseiten navigiert werden. Dazu zählen standardmäßig generierte Systemansichten, ein Administrationsbereich sowie Systeminformationen. Speziell für diese Anlage wurden zudem ein Werkzeugträger und eine Stationsverwaltung eingerichtet. Hier lassen sich Stationen aktivieren oder deaktivieren, eine Stationssimulation starten (falls keine reale Anlage angebunden ist) und die Reihenfolge der Stationen bestimmen. Die Trägerverwaltung bietet einen Überblick über die aktuellen Positionen der Träger und die nächste anzufahrende Station.
Komponententest
Innerhalb des Komponententests sollen die verwendeten Komponenten auf ihre Funktionsfähigkeit geprüft werden. Bei den Sensoren wurde immer bis zur SPS getestet und die Aktoren wurden über die SPS angesteuert. Dadurch konnte neben der eigentlichen Funktion der Komponenten ebenfalls die Schnittstelle überprüft werden.
Dazu wurden folgende Aktoren getestet:
- Ansteuerung der Motoren zur Bewegung des Förderbands
- Stopper-Zylinder der einzelnen Stationen
- Auswurfzylinder an der Station 4 (Ansteuerung über nicht verwendeten Stopper-Zylinder der Station 3)
Folgende Sensoren wurden getestet:
- Induktive Sensoren zur Werkstückträgererkennung in den Stationen
- Induktive Sensoren zur Stauerkennung vor den Stationen
- Induktive Sensoren als Zähler zur Erkennung der Werkstückträgernummer
Integrationstest
Mithilfe des Integrationstests soll das Zusammenspiel mehrere Komponenten getestet werden. Dadurch können Fehler in der Schaltung, der Programmierung, der Mechanik und der Pneumatik identifiziert werden. Es ist wichtig, das Zusammenspiel aller Teilbereiche zu betrachten, da diese später auch alle zusammenarbeiten sollen.
Für den Integrationstest wurde das Förderband durch die Motoren in Bewegung versetzt und ein Werkstückträger durchlief anschließend alle Stationen. Hierbei ist aufgefallen, dass die Höhen der induktiven Sensoren teilweise nicht passte. Bei manchen induktiven Sensoren wurden die Werkstückträger aufgrund einer zu tiefen Positionierung nicht erkannt, da die Entfernung zum Metall des Werkstückträgers zu groß war. Andere Sensoren waren etwas zu hoch montiert, wodurch die Werkstückträger angestoßen sind oder den Sensor leicht berührten.
Systemtest
Im Systemtest wird die gesamte Anlage getestet. Dafür wurde das neu erstellte Programm in die SPS geladen und die Anlage gestartet.
Es konnten mehrere Punkte beobachtet werden:
- An den Stationen passte teilweise die Positionierung von dem induktiven Sensor zur Werkstückträgererkennung und dem Stopper-Zylinder nicht. Dadurch fuhr der Stopper bereits hoch, obwohl der Werkstückträger den Stopper noch nicht vollständig passiert hat.
- Der induktive Zähler Sensor an Station 6 war falsch positioniert, wodurch zwei Werkstückträgernummern gezählt wurden. Dies bereitete Probleme bei der Abfrage, ob der Werkstückträger bearbeitet werden muss.
- Zwischenzeitlich funktionierte die Abfolge der Bearbeitung nicht korrekt. Bei mehr als einem Werkstückträger kam es zu Problemen.
In dem Systemtest konnten verschiedene Fehler entdeckt werden, die anschließend gelöst werden konnten, sodass der Systemtest erfolgreich abgeschlossen werden konnte.
Anmerkung: Für die Produktion des HSHL-Untersetzers werden nur vier Stationen benötigt. Die zwei verbleibenden Stationen wurden am Förderband nicht abgebaut. Lediglich der Stopper-Zylinder an der Station 3 wurde abgebaut, da dessen Ansteuerung für den Auswurfzylinder an Station 4 verwendet wird. An der Station 5 ist der Stopper-Zylinder noch verbaut. Bei dem Start der Anlage fährt der Stopper-Zylinder dauerhaft runter, wodurch keine Beeinflussung der passierenden Werkstückträger mehr stattfinden kann.
Abnahmetest
Bei dem Abnahmetest soll es sich um den letzten Test innerhalb des Projektes handeln. Dieser Test wird nicht durch die bearbeitende Gruppe selbst durchgeführt, sondern von außenstehenden Personen. Diese Personen sollen sich mit der vorliegenden Anlage nicht auskennen und die Handhabung dieser testen und so etwaige Fehler aufdecken. Der Abnahmetest wurde innerhalb des Praktikums am 16.01.2024 erfolgreich durchgeführt.
Inbetriebnahme
Als erstes wurde die Anlage nach Quickstart-Anleitung [1] der vorherigen Gruppenarbeiten gestartet. Folgende Schritte sind dort für das Förderband vorgesehen:
Vorbereiten der Anlage
- Alle Werkstückträger leeren
- Alle Not-Aus Schalter entriegeln
Einschalten der Anlage
- Druckluftversorgung herstellen (Kugelhahn / Wartungseinheiten öffnen)
- Spannungsversorgung herstellen (FI / Steckerleiste einschalten)
- Hauptschalter am Fließband einschalten und "Controller on" betätigen
Starten der Anlage
- "Automatic on" betätigen
Inbetriebnahmeprotokoll/"Abnahme-Testanleitung"
Schritt Nr. | Beschreibung | Ausgangszustand | Aktion(en) | Erwartetes Ergebnis | Ergebnis | Bewertung | Bemerkung |
---|---|---|---|---|---|---|---|
Einschalten 1 | Vorbereitung der Anlage | Anlage befindet sich im Zustand des letzen Durchlaufs | Entfernen aller Werkstückträger vom Förderband; Not-Aus nicht ausgelöst | Förderband ist im Ausgangszustand leer, alle Werkstückträger sind entfernt; Not-Aus nicht ausgelöst | Förderband leer, keine Werkstückträger, Not-Aus nicht ausgelöst | i.O. | |
Einschalten 2 | Signalüberprüfung | Spannungsversorgung abgeschaltet, Druckluft abgedreht | Überprüfung der Signale | Keine anliegenden Signale an der Anlage | Keine Signale erkennbar | i.O. | |
Einschalten 3 | Ausgangszustand der Sensoren prüfen | Druckluftzylinder ausgefahren, Lichtschranken auf selber Höhe, Induktive Sensoren fest verbaut | Überprüfen der Sensoren | "Druckluftzylinder ausgefahren, Lichtschranken auf selber Höhe, Induktive Sensoren fest verbaut" | Status der Sensoren korrekt | i.O. | |
Einschalten 4 | Überprüfen des Förderbandes | Förderband frei von Fremdkörpern | Überprüfen der Anlage auf Fremdkörper | Keine Fremdkörper vorhanden, z.B. auf dem Förderband | Förderband frei | i.O. | |
Einschalten 5 | Werkstückträger einlegen | Werkstückträger nicht auf dem Förderband und leer | Werkstückträger auf das Förderband legen | Definierte Anzahl an Werkstückträgern befindet sich auf dem Förderband | vier Werkstückträger befinden sich auf dem Förderband | i.O. | |
Einschalten 6 | Druckluftzufuhr herstellen | Druckluftventil abgestellt | Druckluftversorgung herstellen (Kugelhahn öffnen) | Druckluftzufuhr an der Anlage aktiv | Druckluftzufuhr hergestellt | i.O. | |
Einschalten 7 | Spannungsversorgung herstellen | Hauptschalter ist ausgeschaltet | Hauptschalter betätigen | Spannungsversorgung liegt an | Spannungsversorgung hergestellt | i.O. | |
Einschalten 8 | Controller einschalten | Controller ausgeschaltet, Controller off leuchtet | Controller on betätigen | Leuchtmelder Controller on leuchtet | Controller eingeschaltet | i.O. | |
Einschalten 9 Variante 1 | Automatikbetrieb starten | Automatikbetrieb stoppen/gestoppt | Schalter an Schaltkasten Automatikbetrieb Ein betätigen | Automatikbetrieb startet, Leuchtmelder Automatikbetrieb Ein leuchtet | Leuchtmelder Automatikbetrieb leuchtet | i.O. | |
Einschalten 10 | Not-Aus-Schalter testen | Not-Aus nicht betätigt | Not-Aus drücken | Anlage hält an | Not aus hält anlage an | i.O. | |
Einschalten 9 | Automatikbetrieb starten | Automatikbetrieb stoppen/gestoppt | HMI-Schalter Automatikbetrieb Ein betätigen | Automatikbetrieb startet, Leuchtmelder Automatikbetrieb Ein leuchtet | Automatikbetrieb ist gestartet | i.O. | |
Einschalten 11 | Funktionsweise Förderband | Förderband fängt langsam an sich zu drehen | Beobachtung | Förderbänder drehen sich alle und in die gleiche Richtung | Förderbänder drehen sich korrekt | i.O. | |
Einschalten 12 | Funktionsweise Pneumatikzylinder (Stopper) | Zylinder ausgefahren, Zylinder wird eingefahren, wenn Werkstückträger erkannt, Zylinderstellung entsprechend HMI | Beobachtung | Zylinder fährt ein | Zylinder sind eingefahren | i.O. | |
Einschalten 13 | Funktionsweise induktive Sensoren | Kein Werkstückträger: Induktive Sensoren nicht aktiv; Werkstückträger: Induktive Sensoren aktiv | Beobachtung; Werkstückträger über induktive Sensoren bewegen | Signallämpchen am induktiven Sensor leuchtet bei Erkennung | Signallampe leuchtet | i.O. | |
Einschalten 14 | HMI Funktionen testen (Werkstückträgerverwaltung & Stationsverwaltung | Anlage gestartet | Beobachtung; Änderungen vornehmen und reale Funktion überprüfen | Stationen und Werkzeugträger verhalten sich wie in HMI einprogrammiert | Stationenszylinder können gesteuert werden | i.O. | |
Ausschalten 1 | Automatikbetrieb stoppen | Automatikbetrieb ist eingeschaltet | Automatikbetrieb aus betätigen als Button an Gehäuse oder auf HMI | Automatikbetrieb stoppt, Leutmelder Automatikbetrieb aus leuchtet | Automatikbetrieb gestoppt | i.O. | |
Ausschalten 2 | Controller ausschalten | Controller eingeschaltet, Controller on leuchtet | Controller off betätigen | Leuchtmelder Controler off leuchtet | Controller gestoppt | i.O. | |
Ausschalten 3 | Spannungsversorgung abschalten | Hauptschalter ist eingeschaltet | Hauptschalter ausschalten | Keine Spannung mehr an der Anlage vorhanden, Leuchtmelder alle ausgeschaltet | Spannung an der Anlage ausgeschaltet | i.O. | |
Ausschalten 4 | Druckluft abschalten | Druckluft an Anlage vorhanden | Druckluftversorgung abstellen | Keine Druckluft mehr an der Anlage vorhanden | Druckluft abgedreht | i.O. | |
Ausschalten 5 | Entnahme der Werkstückträger | Werkstückträger auf dem Förderband vorhanden, ggf. in unterschiedlichen Stadien der Produktion | Werkstückträger entnehmen | Förderband ohne Werkstückträger | Keine Werkstückträger auf dem Förderband | i.O. |
Ergebnis
Zum Ende des diesjährigen Praktikums konnte das Förderband mit einer neuen SPS wieder in Betrieb genommen werden. Dazu gehörte der Einbau einer neuen, leistungsfähigeren SPS, die Gewährleistung eines störungsfreien Betriebs mit mehreren Werkstückträgern sowie die Optimierung der Stationsreihenfolge und der exakten Positionierung der Werkstückträger auf dem Förderband. Darüber hinaus wurden grundlegende HMI-Bilder entwickelt und implementiert, um die Bedienung und Überwachung des Systems zu vereinfachen und zu verbessern. Ein weiterer bedeutsamer Beitrag war die Erstellung eines detaillierten Wiki-Artikels, der eine schrittweise Anleitung bietet, um zukünftigen Nutzern und Betreuern der Anlage einen präzisen Leitfaden an die Hand zu geben. Diese Verbesserungen und die Dokumentation sorgen für eine gesteigerte Effizienz und Benutzerfreundlichkeit des Förderbandsystems.
Lessons Learned
Während des Praktikums lag der Fokus intensiv auf der Auseinandersetzung mit der ET200SP und ihrer Programmierung im TIA-Portal. Besonders herausfordernd gestaltete sich dabei das korrekte Projektieren der ET200SP, was durch die Existenz verschiedener Versionen der SPS und die Notwendigkeit, die IP-Adresse korrekt zuzuweisen, erschwert wurde. Auch die Integration der HMI gestaltete sich nicht immer einfach, konnte jedoch schlussendlich erfolgreich umgesetzt werden.
Ausblick
Die derzeitige Anlage befindet sich in einem funktionalen Zustand, bietet allerdings Raum für weitere Optimierungen und Verbesserungen. Ein wesentlicher Schritt nach vorne wäre die Erweiterung der Funktionalitäten der HMI, um den Nutzern mehr Einstellungsmöglichkeiten und somit eine flexiblere Handhabung der Anlage zu ermöglichen. Darüber hinaus liegt ein signifikantes Potenzial in der vollständigen Integration aller vorhandenen Stationen. Obwohl die notwendigen Leitungen bereits verlegt sind, sind noch nicht alle Stationen in Betrieb. Die Aktivierung und Einbindung dieser Stationen in das Gesamtsystem würde die Effizienz und Produktivität der Anlage erheblich steigern und zu einer umfassenderen Nutzung der vorhandenen Ressourcen führen. Diese Schritte bilden aussichtsreiche Ziele für die nächste Entwicklungsphase der Anlage.
Verwendete Software
- MS PowerPoint:Erstellung des funktionalen und technischen Systementwurfs und der Komponentenspezifikation
- MS Excel: Erstellung einer Anforderungsdefinition
- PAP Designer: Erstellen eines Programmablaufplans
- Siemens TIA-Portal: Erstellung des neuen Programms
Unterlagen
Projektieren der ET200SP: Siemens SPS ET200SP CPU1515SP PC2 und HMI TP700 Comfort - Projekt erstellen - Schritt fuer Schritt
Die Unterlagen zum Förderband befinden sich gesammelt in SVN.
→ zurück zur Übersicht: Praktikum Produktionstechnik
Programmierung von Siemens Simatic S7 Anlagen unter Step7
Literatur
- ↑ Funktion: Datei:Quick-Start-Anleitung MPS500.pdf (Originaldatei), Studentenarbeit im GPE Praktikum, erstellt bei vorheringen Gruppenarbeiten
Alle nicht mit Quellen versehenen Abbildungen sind eigene Abbildungen.