Produktion eines HSHL-Getränkeuntersetzers: Kleben (Station 2)
Autoren: Jahn Gross, Jens Schwabe
Dozent: Prof. Dr. Mirek Göbel
Wintersemester: 2021/2022
Fachsemester: 7
→ zurück zur Übersicht: [Praktikum Produktionstechnik]
→ zum Hauptartikel: [HSHL-Getränkeuntersetzer]
Einleitung
Dieses Projekt wurde in dem Praktikum „Produktionstechnik“ des Schwerpunkt-Moduls „Global Production Engineering III“ durchgeführt. Es ist Teil des 7. Semesters des Studiengangs „Mechatronik“ an der Hochschule Hamm-Lippstadt. Die Aufgabe dieses Praktikums ist der Aufbau eines automatisierten Systems mit Hilfe einer Speicherprogrammierbare Steuerung (SPS) des Unternehmens Siemens. Als Programmier-Software wird das Siemens spezifische Programm „TIA-Portal“ verwendet.
Gesamtkonzept
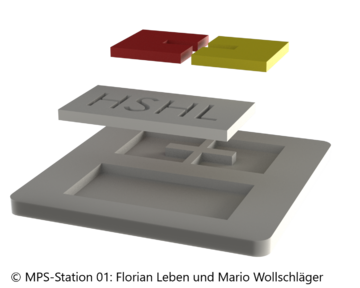
Die Gesamtaufgabe dieser Anlage ist die Produktion von HSHL-Getränkeuntersetzern, welche als Werbegeschenke dienen können. Für die Umsetzung dieses Projekts wurden vorab spezifische Anforderungen gestellt:
- Projekt soll nachhaltig sein → Weiterentwicklungs-Möglichkeiten für nachfolgende Semester
- System soll auf vier Stationen aufteilbar sein
- Getränkeuntersetzer sollen individualisierbar sein
- Nutzung des vorhandenen Förderbands der MPS-Anlage als gemeinsame Schnittstelle
In Folge dieser Anforderungen wurde das System in vier unterschiedliche Stationen aufgeteilt. Die erste Station „Kommissionierung" befasst sich mit der Bestückung des Warenträgers. Station drei „Montage“ fügt die vier einzelnen Komponenten zusammen. Die letzte Station „Verpackung“ umhüllt den fertigen Getränkeuntersetzer mit einer eigens kreierten Verpackung.
Fertigungsaufgabe
Speziell die Station „Kleben“ ist für das Auftragen eines Klebers verantwortlich. Dieser wird mittels Klebepunkte über sechs Klebedüsen in die Einkerbungen der Grundplatte gesetzt. Der Kleber sorgt für einen festen Halt der anschließend eingesetzten Einzelteile.
Umsetzung des Klebekonzepts
Aufbau der Station
Aufgrund der benötigten Sicherheitsvorkehrungen, welche für eine reale Umsetzung des Klebeprozesses nötig wären, wird dieser Prozess lediglich simuliert. Dadurch kann zumindest die Visualisierung der Klebung umgesetzt werden. Die Aufgabe der Station „Kleben“ ist intern in drei einzelnen Stationen aufgeteilt:
- Transferstation
- Transportstation
- Klebestation
Die drei Stationen werden nachfolgend näher erläutert. Für die Umsetzung dieser Stationen wurden unterschiedliche Komponenten verwendet. Diese werden in der nebenstehenden Abbildung 3 dargestellt.
Die Transferstation befasst sich mit dem Transfer des Warenträgers von dem Förderband herunter und in die Station „Kleben“ hinein. Dafür sorgt ein Druckluftzylinder, welcher auf der Oberseite des Förderschlittens angebracht ist. An dem Ende der Kolbenstange dieses Zylinders ist eine aus 3D-Druck gefertigte Entnahmenase. Diese greift in die Außenkante des Warenträgers und zieht diesen beim Einfahrvorgang mit. Somit befindet sich der Warenträger am Ende dieser Transferstation auf dem Förderschlitten.
Dieser Förderschlitten sitzt auf dem Förderer. Letzterer sorgt in der Transportstation für den Transport des Warenträgers innerhalb der Station „Kleben“. Mit Hilfe des Förderers wird der Warenträger von dem Bereich des Förderbands weiter in die Station gefahren. Die Endlage dieses Förderers stellt die Position für die letzte Station dar. Folglich befindet sich der Warenträger nach Beendigung des Transportprozesses unterhalb des Schutzkäfigs.
Die letzte Station mit dem Namen "Klebestation" erfüllt die eigentliche Aufgabe dieser Gesamtstation. Es simuliert mit einem Aufsetzen der Klebedüsen den geforderten Klebeprozess. Dieser Prozess wird mit Hilfe eines zweiten Druckluftzylinders realisiert. Dieser befindet sich an dem oberen Ende des Befestigungsgalgens. Der Galgen wurde aus 45x45mm Boschprofilen zusammengebaut. Dafür wurde ein Winkel in die obere Ecke des Galgens gesetzt, um die beiden Querbalken zu verbinden. Der benötigte Zylinder ist mit einem weiteren Winkel an dem Querbalken des Galgens angebracht worden. An dem Ende der Zylinderstange wird der Schutzkäfig mittels eines Lochs in der Deckenplatte des Käfigs befestigt.
Sobald der Warenträger unterhalb des Schutzkäfigs befördert wurde, fährt der Schutzkäfig über den Druckluftzylinder herunter. An dieser Stelle wird der Klebeprozess gestartet. Damit eine zusätzliche Visualisierung stattfindet, wurde eine Meldeleuchte in dieser Klebestation integriert. Diese beginnt zu leuchten, sobald der Schutzkäfig heruntergefahren wurde. Dadurch soll dem Bediener eine separate optische Warnung vermittelt werden, um ihn vor möglichen Gefahren zu schützen.
Nachdem die Klebesimulation beendet wurde fährt der Zylinder in seine hintere Endlage und die Meldeleuchte beendet den Leuchtprozess. Sobald der Schutzkäfig an seiner oberen Endposition angelangt ist, fährt der Förderer samt Warenträger an den Bereich des Förderbands zurück. Mit Hilfe des Druckluftzylinders wird der Warenträger auf das Förderband gedrückt. An dieser Position angekommen fährt der Warenträger über das Förderband zur nächsten Station. Der Zylinder verharrt jedoch in seiner ausgefahrenen Endlage, um den nächsten Warenträger aufnehmen zu können.
Aufbau des Schutzkäfigs
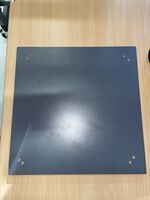
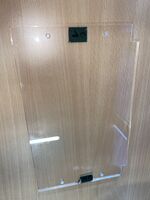
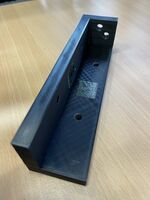
Der Schutzkäfig ist das ausschlaggebende Sicherheitselement dieser Umsetzung und demnach essenziell für dieses Klebekonzept. Nachfolgend wieder der Aufbau dieses Schutzkäfigs samt aller eingesetzten Komponenten beschrieben.
Bevor der Schutzkäfig konzipiert werden konnte, wurden vorab die selbst aufgestellten Anforderungen an diesen Käfig definiert:
- (1a) Der Schutzkäfig darf nicht mehr als 5kg wiegen, damit er problemlos von dem Druckluftzylinder verfahren werden kann
- (2a) Der Benutzer darf zu keinem Moment in den Klebeprozess fassen können
- (3a) Der Klebeprozess soll von außen sichtbar sein
Mit Hilfe dieser Anforderungen wurden die Materialien des Schutzkäfigs ausgesucht. Dabei wurde soweit möglich auf Metall verzichtet, um ein geringes Gesamtgewicht zu erzeugen (vgl. 1a). Die Deckenplatte des Schutzkäfigs (Abbildung 4) besteht aus einer 5mm dicken Kunststoffplatte. Die Maße der Deckenplatte umfassen 300x300mm, welche gleichzeitig die Außenmaße des Schutzkäfigs widerspiegeln. In diese Kunststoffplatte wurden jeweils zwei Löcher in die Ecken-Bereiche gebohrt. Diese dienen später für die Verbindungspunkte der Deckenplatte mit den Käfigsäulen (Abbildung 6).
Die Seitenscheiben des Schutzkäfigs (Abbildung 5) wurden aus 5mm dicken Plexiglas-Scheiben gefertigt (vgl. 3a). Diese Plexiglas-Scheiben sind 260mm breit und 165mm hoch. An den oberen Ecken der Scheibe wurden Aussparungen eingefügt. Diese sorgen für ein lückenloses Zusammenfügen der Seitenscheiben mit den Käfigsäulen. An den Seiten der Scheiben wurden jeweils zwei Bohrungen mit M4 Gewinden eingefügt. Über diese Gewinde können die Käfigsäulen mit den Scheiben verbunden werden, ohne zusätzliche Muttern verwenden zu müssen. Folglich wird kein extra Gewicht für diese Verbindungspunkte nötig.
Die Käfigsäulen des Schutzkäfig-Konzepts wurden zuvor mit dem CAD Programm „Solid Works“ konstruiert und mit Hilfe eines 3D-Druckers produziert. Diese Käfigsäulen sind somit extrem leicht und gleichzeitig sehr stabil. In die Seitenflächen dieser Käfigsäulen wurden jeweils zwei Durchgangslöcher gebohrt. Wie zuvor erwähnt wird über diese Löcher eine Verbindung mit den Seitenscheiben hergestellt. In die Deckenfläche der Säulen wurden ebenfalls zwei Durchgangslöcher gebohrt. Diese dienen als Verbindungspunkte mit der Deckenplatte. Dabei wurden bewusst zwei Löcher gesetzt, um eine zusätzliche Verdrehsicherheit der Käfigsäulen hinzuzufügen.
In Abbildung 8 ist der fertig aufgebaute Schutzkäfig dargestellt. Durch die transparenten Plexiglas-Scheiben ist die Beobachtung des Klebekonzepts möglich (vgl. 2a). Zusätzlich kann der Benutzer zu keiner Zeit an die Klebedüsen fassen, da der Käfig rundum geschlossen ist. Dadurch wird ein dauerhafter Schutz des Benutzers gewährleistet. Aufgrund der Tatsache, dass der Schutzkäfig aus den Materialien Kunststoff und Plexiglas besteht, liegt er gewichtstechnisch unter der Maximalgrenze von 5kg. Somit kann er problemlos von dem Druckluftzylinder verfahren werden. Folglich sind alle Anforderungen des Käfigs erfüllt.
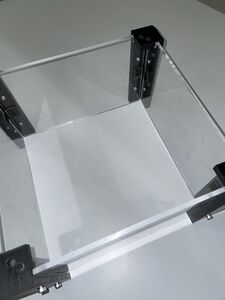
Vorgehensweise nach V-Modell
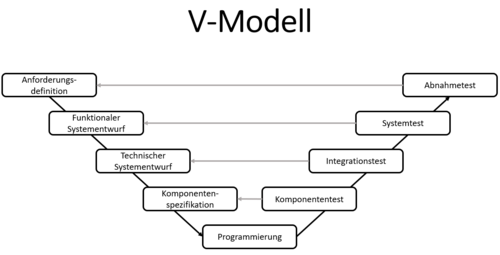
Das V-Modell wird eingesetzt, um dem Benutzer bei der Organisation und Durchführung eines anstehenden Projekts zu helfen. Es visualisiert das lineare Vorgehen der einzelnen Projektphasen. Angefangen bei den Anforderungen des Projekts begleitet es den Benutzer bis schlussendlich der Abnahmetest das erfolgreiche Abschließen des Projekts bestätigt.
Anforderungsdefinition
Innerhalb der Anforderungsdefinition werden die Aufgaben des Projekts festgelegt und anhand von festgelegten Anforderungen spezifiziert. Bei der Anforderungsdefinition wurden unter anderem folgende Aspekte definiert:
- Geometrie & Gewicht der Station und der einzelnen Komponenten
- Aufbau der Station
- Verwendete Software und Werkzeuge
- Sicherheit und wie diese gewährleistet wird
Funktionaler Systementwurf
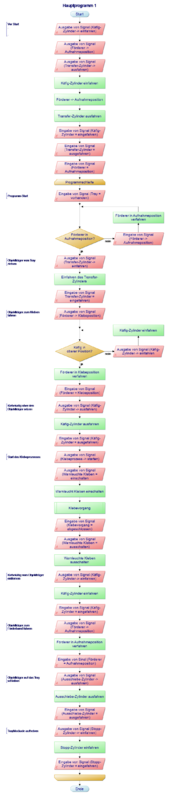
Im funktionalen Systementwurf werden die zu erfüllenden Funktionen der Anlage in einem Programmablaufplan (PAP) gegliedert. Hierfür wurde das Programm "PAP-Designer genutzt. Bei der Erstellung wurde bewusst auf Unterprogramme verzichtet, um alle Funktionen auf einer Ebene sichtbar zu halten. Schematisch ist die Reihenfolge, in der die Funktionen abgearbeitet werden, angepasst an die drei Hauptstationen, aus denen die Station 2 besteht (siehe Abschnitt 2.1 Aufbau der Station). Nachfolgend ist der funktionale Ablauf vereinfacht dargestellt:
- Entnahme des Objektträgers von dem gemeinsamen Förderband der MPS-Anlage
- Zylinder und Förderer in die "Aufnahme-Position" verfahren
- Warten auf das Signal des induktiven Sensors, dass ein Objektträger vorhanden ist
- Objektträger mittels Zylinder auf den Förderer ziehen
- Freigabe für den nächsten Abschnitt
- Transfer des Objektträgers von der Aufnahme des Objektträgers zum Klebeprozess
- Sicherstellen, dass der Zylinder, der den Schutzkäfig hält, in der oberen Position ist
- Förderer in die Position "Kleben" verfahren
- Freigabe für den nächsten Abschnitt
- Durchführung des Klebeprozesses
- Sicherstellen, dass der Transfer-Zylinder und der Förderer in der "Klebe-Position" stehen
- Käfigzylinder in die "Klebe-Position" verfahren
- Meldeleuchte einschalten
- Klebedauer abwarten
- Meldeleuchte ausschalten
- Käfig-Zylinder in die obere Position verfahren
- Freigabe für den nächsten Abschnitt
- Rücktransfer des Objektträgers vom Klebeprozess zur Einspeisung auf das gemeinsame Förderband der MPS-Anlage
- Sicherstellen, dass der Zylinder, der den Schutzkäfig hält, in der oberen Position ist
- Förderer in die Position "Aufnahme" verfahren
- Freigabe für den nächsten Abschnitt
- Einspeisung des Objektträgers auf das gemeinsame Förderband der MPS-Anlage
- Sicherstellen, dass der Förderer in der Aufnahme-Position ist
- Aufnahme-Zylinder in die "Aufnahme-Position" verfahren
- Objektträger mittels Zylinder auf das gemeinsame Förderband der MPS-Anlage schieben
- Freigabe für den nächsten Abschnitt
- Warten auf neuen Objektträger
Der ausführliche PAP befindet sich unter dem folgenden Link: [Vollständiger PAP]
Auf der Basis dieses PAPs erfolgt die Programmierung der SPS (siehe Abschnitt "Programmierung"). Mittels der SPS werden alle Funktionen der Station verwaltet.
Technischer Systementwurf
Der technische Systementwurf spezifiziert die Funktionen des Systems weiter und legt die Schnittstellen der einzelnen Stationen fest. Dabei wurde für den Entwurf der Station „Kleben“ zwischen allgemeinen und stationsabhängigen Schnittstellen unterschieden. Zusätzlich wurden die einzelnen Signale und Befehle zwischen der jeweiligen Station und der SPS festgelegt. Diese wurden in der folgenden Komponentenspezifikation weiterbearbeitet.
Komponentenspezifikation
Nachdem die Schnittstellen und zu verwendenden Komponenten festgelegt wurden, müssen diese in der Komponentenspezifikation detaillierter betrachtet werden. Für die Schnittstelle Station und SPS wurden die einzelnen Ein- und Ausgänge definiert. Zusätzlich wurden die Spannungen und Ströme ermittelt. Diese erleichtern die spätere Verdrahtung der SPS, indem die Anschlussklemmen bereits vordefiniert werden.
Die Komponentenspezifikation wurde dabei auf die drei Stationen Transfer, Transport und Kleben aufgeteilt, wobei die benötigten Komponenten jeder Station festgelegt wurden. Des Weiteren wurde die SPS und die Versorgungseinheiten als zusätzliche Komponenten aufgenommen und durch sämtliche Ein-, Ausgänge und Bauteile definiert.
Programmierung
Die Programmierung der Siemens-SPS erfolgte über das Programm "TIA-Portal". Gewählt wurde die Programmiersprache "FUP".
Wie ein Projekt im TIA-Portal angelegt werden kann und wie anschließend die Programmerstellung mit der Programmiersprache "FUP" erfolgen kann, wird in einem Tutorial anhand eines Beispiels erklärt. Dieses Tutorial befindet sich in dem SVN-Ordner der Station Kleben: Tutorium-Handout_SPS Programmierung TIA Portal.
Als Basis für die Erstellung des Programms für die Station Kleben wurde der zuvor beschriebene PAP genutzt. Zu unterscheiden sind die Bausteine für die Ansteuerung der vier Aktoren:
- Ansteuerung des "Aufnahme-Zylinders"
- Ansteuerung des "Käfig-Zylinders"
- Ansteuerung des "Förderers" (siehe hierzu: Ansteuerung einer Schrittmotorachse mit SPS und HMI)
- Ansteuerung der "Meldeleuchte"
Für diese vier Aktoren wurden Bausteine in der Programmieroberfläche erzeugt und in dem Hauptprogramm "main" zusammengeführt. Erstellt wurden die logischen Verkettungen innerhalb der Bausteine nach den Ausführungen in dem oben genannten Tutorial. Die Abbildung 13 zeigt Beispielhaft ein Netzwerk des Bausteins zur Ansteuerung des Aktors "Aufnahme-Zylinder".
Komponententest
Innerhalb des Vorgangsschritts „Komponententest“ sollen die verwendeten Komponenten auf ihre Funktionsfähigkeit untersucht werden. Aufgrund fehlender Komponenten (durch Lieferungsverzug) konnte dieser Schritt in der Projektbearbeitung nicht mehr realisiert werden. Nachfolgend wird eine beispielhafte Testung eines Pneumatikzylinders beschrieben.
Testung eines Pneumatikzylinders:
- Befestigung des Zylinders an einer steifen, unnachgiebigen Oberfläche
- Verschlusskappen der Zylindereingänge entfernen
- Ventilanschlüsse einschrauben
- Drosseln der Ventilanschlüsse auf einen geringen Durchgangsfluss einstellen
- Druckluftschläuche in die Ventilanschlüsse einführen
- Druckluftschläuche in die Versorgungseinheit einführen Versorgungseinheit vorher auf Sperrstellung stellen
- Sperrstellung der Versorgungseinheit langsam drehen, um Luftzufuhr zu generieren
- Verfahrrichtung der Kolbenstange kontrollieren
- Verfahrgeschwindigkeit und -verhalten der Kolbenstange kontrollieren
Die Testung gilt als erfolgreich, sobald die Kolbenstange der vorhergehenden Schaltung entspricht und die Stange ruckelfrei und ohne Geräuschentwicklung verfährt.
Integrationstest
Durch den Integrationstest sollen mehrere Komponenten im Zusammenspiel miteinander getestet werden. Dadurch können Fehler des Schaltungsaufbaus oder in der Programmierung des SPS-Programms identifiziert werden. Aufgrund der Tatsache, dass einige Komponenten nicht zeitgemäß eingetroffen sind, konnte dieser Projektschritt nicht realisiert werden. Im Genauen sind zwei 3D-Druckteile und drei bestellte Komponenten nicht zeitgemäß eingetroffen. Die fehlenden 3D-Druckteile sind die Traverse (siehe Stückliste) und die Führungssäule (siehe Stückliste). Aufgrund der Maße dieser Komponenten konnten beide nicht durch den Filament-Drucker der Hochschule erzeugt werden. Des Weiteren befand sich der 3D-Drucker mit größerer Druckfläche im Störmodus. Die bestellten Komponenten setzen sich aus den vier Drosselrückschlagventilen, einem Druckregelventil und vier Näherungsschaltern (Abbildungen dieser Komponenten befinden sich in der Stückliste) des Herstellers FESTO zusammen. Der Schutzkäfig konnte trotz der fehlenden Komponenten zusammengebaut werden. Ein Aufbau der Druckluftversorgung war aufgrund der fehlenden Komponenten noch nicht sinnvoll. Sobald die Komponenten eingetroffen sind kann dieser Aufbau erfolgen.
Ergebnis
Wie zuvor erwähnt ist der Gesamtaufbau der Station „Kleben“ nicht umsetzbar gewesen. Dennoch konnten die essenziellen Grundsteine für eine erfolgreiche Realisierung gelegt werden. Somit konnte das Gesamtkonzept des Klebeprozesses aufgestellt und definiert werden. Des Weiteren ist die Programmierung des SPS-Programms finalisiert, sodass es einsatzfähig ist. Der Aufbau der Station wurde soweit möglich ebenfalls umgesetzt. Somit konnte der Förderer samt Förderschlitten aufgebaut, der Befestigungsgalgen zusammengebaut und mit dem passenden Druckluftzylinder versehen werden. Des Weiteren wurde die SPS auf dem Stationstisch aufgebaut. Zusätzlich wurden Kabelführungen für eine folgende Verdrahtung der Komponenten integriert. Das essenzielle Element dieses Klebekonzepts, der Schutzkäfig, konnte ebenfalls vollumfänglich aufgebaut werden. Dieser kann somit an der Kolbenstange des platzierten Zylinders befestigt werden.
Ausblick
Die noch anstehenden Aufgaben für eine gesamte Umsetzung des Klebekonzepts wurde bereits in den vorherigen Abschnitten erläutert. Zusätzlich ergeben sich jedoch weitere Ansätze und Modifizierungsmöglichkeiten dieses Klebekonzepts für nachfolgende Semester. Diese definieren sich wie folgt:
- Realisierung des Klebekonzepts durch die Verwendung von echten Klebedüsen und -schläuchen
- Integration einer Sirene zur akustischen Warnung der Durchführung eines Klebekonzepts
- Programmierung und Integrierung eines Not-Aus-Knopfs zur sofortigen Abschaltung bei etwaigen Problemen Erhöhung der Sicherheit der Station
- Einbindung eines Mechanismus zur Entfernung des übrigen Klebers der Klebedüsen
Verwendete Software
- Solid Works: Konstruktion der 3D-Druckteile und Erstellung benötigter Zeichnungen
- MS PowerPoint: Aufstellung des Konzepts, Erstellung des technischen Systementwurfs
- MS Excel: Erstellung der Anforderungsdefinition, Komponentenspezifikation
- PapDesigner: Erstellung des funktionalen Systementwurfs
- Siemens TIA-Portal V15.1: Erstellung des SPS-Programms
- TinyCAD: Erstellung der Schaltpläne
Verwendete Hardware
→ siehe Stückliste
Verwendete Komponenten der Station Kleben:
Funktion | Bezeichnung | Material | Hersteller | Anzahl | Preis | Beschreibung | Bild |
---|---|---|---|---|---|---|---|
Mechanik | - | Kunststoff | Eigenherstellung | 1 | - | Deckenplatte-Schutzkäfig | ![]() |
Mechanik | - | Plexiglas | Eigenherstellung | 4 | - | Seitenscheiben - Schutzkäfig | ![]() |
Mechanik | 3D-Druckteil | 3D-Druck-PLA Filament | Eigenherstellung | 4 | - | Käfigsäulen - Schutzkäfig | ![]() |
Mechanik | Bosch-Profil | - | Bosch | 2 | - | 45x45mm 4Kant-Boschprofil Datenblatt | ![]() |
Mechanik | 3D-Druckteil | 3D-Druck-PLA Filament | Eigenherstellung | 6 | - | Klebedüsen - Schutzkäfig | ![]() |
Mechanik | 3D-Druckteil | 3D-Druck-PLA Filament | Eigenherstellung | 1 | - | Traverse - Schutzkäfig | ![]() |
Mechanik | 3D-Druckteil | 3D-Druck-PLA Filament | Eigenherstellung | 1 | - | Förderer - Adapterplatte | ![]() |
Mechanik | 3D-Druckteil | 3D-Druck-PLA-Filament | Eigenherstellung | 4 | - | Führungssäule | ![]() |
Pneumatik | Normzylinder DSBC-Q-32-200-D3-PPVA-N3 | - | Festo | 1 | - | Doppeltwirkender Zylinder-32mm Kolben M6 Außengewinde, 200mm Hub-verdrehsicher- Datenblatt | ![]() |
Pneumatik | Normzylinder DSBC-Q-32-150-D3-PPVA-N3 | - | Festo | 1 | - | Doppeltwirkender Zylinder-32mm Kolben M6 Außengewinde, 150mm Hub-verdrehsicher- Datenblatt | ![]() |
Pneumatik | Ventilinsel VP10-VI | - | Festo | 1 | 347,98€ | 10P-10-2E-IC-N-A-GG+H2D Datenblatt | ![]() |
Pneumatik | Drossel-Rückschlagventil GRLA-1/8-QS-6-D | - | Festo | 4 | - | Abluft-Drossel-Rückschlagfunktion-einschraubbar-185l/min-0,2-10bar Datenblatt | ![]() |
Pneumatik | Druckregelventil LR-1/4-DB-7-MINI | - | Festo | 1 | - | Mini-44mm-Drehknopf mit Arretierung-Sekundärlüftung-mit Manometer Datenblatt | ![]() |
Elektrik | SPS | - | SIEMENS | 1 | - | 6EP7133-6AE00-0BN0 Datenblatt | ![]() |
Elektrik | Näherungsschalter SMT-8M-A-PS-24V-E-2,5-OE | - | Festo | 4 | - | T-Nut-magnetoresistiv-Schließer-Positionsmessung Datenblatt | ![]() |
Elektrik | Förderer | - | Igus | 1 | - | Schrittmotorachse Datenblatt | ![]() |
Literaturverzeichnis
- ↑ https://wiki.hshl.de/wiki/index.php/Ampel-Demonstrator/ V-Modell Projekt Ampeldemonstrator
- ↑ https://catch.app/itm/v1%7C124881444190%7C425961454533
- ↑ https://www.festo.com/de/de/a/1463250/?q=1463250~:festoSortOrderScored&identCode1=DSBC-Q-32-200-D3-PPVA-N3
- ↑ https://www.festo.com/de/de/a/1463250/?q=1463250~:festoSortOrderScored&identCode1=DSBC-Q-32-200-D3-PPVA-N3
- ↑ https://www.festo.com/de/de/a/18200/?q=18200~:festoSortOrderScored&identCode1=10P-10-2E-IC-N-A-GG%2BH2D
- ↑ https://www.festo.com/de/de/a/193144/
- ↑ https://www.festo.com/de/de/a/539682/?q=539682~:festoSortOrderScored
- ↑ https://www.elektromax24.de/Siemens-Stromversorgung-SIMATIC-ET-200SP-PS-1phasig-DC-24V-5A?gclid=EAIaIQobChMI6fz8jbjh9QIVyO5RCh2WQwYGEAQYFiABEgKfZ_D_BwE
- ↑ https://www.festo.com/de/de/a/574335/
- ↑ https://www.igus-cad.com/default.aspx
→ zurück zum Hauptartikel: [Praktikum Produktionstechnik]