Produktion eines HSHL-Getränkeuntersetzers: Kleben (Station 2): Unterschied zwischen den Versionen
Zeile 179: | Zeile 179: | ||
<gallery widths = "300" heights = "300"> | <gallery widths = "300" heights = "300"> | ||
Datei: | Datei:Box Klebeverteilung.png| '''Ausschieber des Zylinder 2''' <br /> Dieser | ||
Datei: | Datei:Deckel_Klebeverteilung.png| '''Ausschieber des Zylinder 3''' <br /> Dieser | ||
Datei: | Datei:Spritzenhalter_hinten_2.png| '''Zylinderhalterung des Zylinder 2''' <br /> Diese | ||
Datei: | Datei:Spritzenhalter_vorne.png| '''Zylinderhalterung des Zylinder 3''' <br /> | ||
Datei: | Datei:Zylinderhalter.png| '''Verpackungsmagazin''' <br /> Dieses | ||
</gallery> | </gallery> |
Version vom 14. Januar 2023, 09:25 Uhr
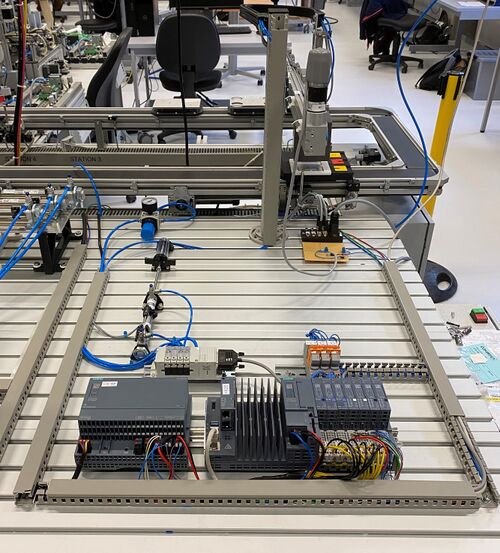
Autoren: Frederik Baune, Matthias Hernzel
Dozent: Prof. Dr. Mirek Göbel
Wintersemester: 2022/2023
Fachsemester: 7
→ zurück zur Übersicht: [Praktikum Produktionstechnik]
→ zum Hauptartikel: [HSHL-Getränkeuntersetzer]
Einleitung
Dieses Projekt wurde in dem Praktikum „Produktionstechnik“ des Schwerpunkt-Moduls „Global Production Engineering III“ durchgeführt. Es ist Teil des 7. Semesters des Studiengangs „Mechatronik“ an der Hochschule Hamm-Lippstadt. Die Aufgabe dieses Praktikums ist der Aufbau eines automatisierten Systems mit Hilfe einer Speicherprogrammierbare Steuerung (SPS) des Unternehmens Siemens. Als Programmier-Software wird das Siemens spezifische Programm „TIA-Portal“ verwendet.
Gesamtkonzept
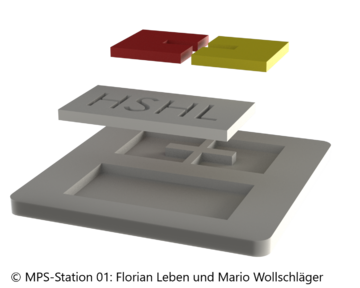
Die Gesamtaufgabe dieser Anlage ist die Produktion von HSHL-Getränkeuntersetzern, welche als Werbegeschenke dienen können. Für die Umsetzung dieses Projekts wurden vorab spezifische Anforderungen gestellt:
- Projekt soll nachhaltig sein → Weiterentwicklungs-Möglichkeiten für nachfolgende Semester
- System soll auf vier Stationen aufteilbar sein
- Getränkeuntersetzer sollen individualisierbar sein
- Nutzung des vorhandenen Förderbands der MPS-Anlage als gemeinsame Schnittstelle
In Folge dieser Anforderungen wurde das System in vier unterschiedliche Stationen aufgeteilt. Die erste Station „Kommissionierung" befasst sich mit der Bestückung des Warenträgers. Die Station zwei „Kleben“ trägt auf den Grundrahmen des HSHL-Untersetzer Klebstoff auf. Die Station drei „Montage“ fügt die vier einzelnen Komponenten zusammen. Die letzte Station „Verpackung“ umhüllt den fertigen Getränkeuntersetzer mit einer eigens kreierten Verpackung.
Fertigungsaufgabe
Speziell die Station „Kleben“ ist für das Auftragen eines Klebers verantwortlich. Dieser wird mittels Klebepunkte über vier Klebedüsen in die Einkerbungen der Grundplatte gesetzt. Der Kleber sorgt für einen festen Halt der anschließend eingesetzten Einzelteile.
Vorgehensweise nach V-Modell
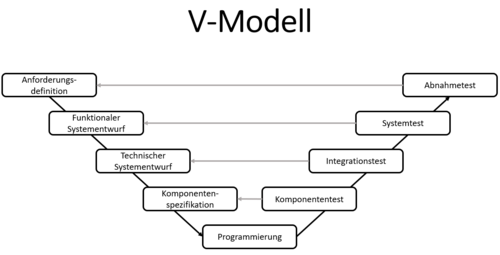
Das V-Modell wird eingesetzt, um dem Benutzer bei der Organisation und Durchführung eines anstehenden Projekts zu helfen. Es visualisiert das lineare Vorgehen der einzelnen Projektphasen. Angefangen bei den Anforderungen des Projekts begleitet es den Benutzer bis schlussendlich der Abnahmetest das erfolgreiche Abschließen des Projekts bestätigt. Dabei sind die einzelen Schritte des absteigenden Pfades mit den korrespondierenden Schritte des aufsteigenden Pfades sinnhaftig miteinander verknüft und bauen aufeinader auf.
Anforderungsdefinition
Innerhalb der Anforderungsdefinition werden die Aufgaben des Projekts festgelegt und anhand von festgelegten Anforderungen spezifiziert. Bei der Anforderungsdefinition wurden unter anderem folgende Aspekte definiert:
- Geometrie & Gewicht der Station und der einzelnen Komponenten
- Aufbau der Station
- Verwendete Software und Werkzeuge
- Sicherheit und wie diese gewährleistet wird
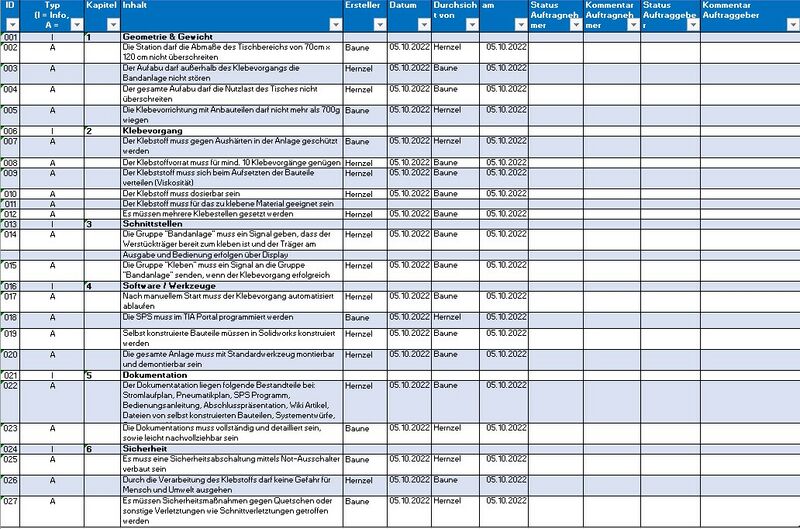
Funktionaler Systementwurf
Der funktionale Systementwurf gliedert sich in zwei Bereiche. Zum einen wird das grobe Gesamtkonzept der Station abgebildet und zum anderen wird der Ablauf eines Klebvorgangs mit Hilfe eines Ablaufplans beschrieben
Datei:PAP StationKleben.pdf)|170px|mini]]
Konzept
In der Abbildung xy ist das Konzept der Station "Kleben" dargestellt. Das Konzept kann in folgende Teile zerlegt werden:
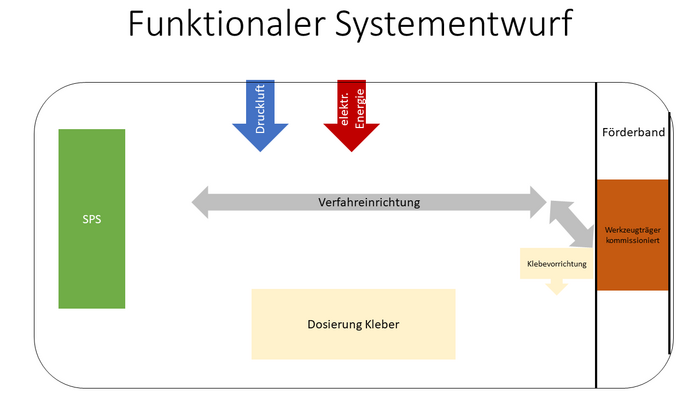
SPS
Die speicherprogrammierbare Steuerung arbeitet nach dem "EVA-Prinzip". Eingänge von Sensoren werden gelesen und verarbeitet. Die SPS schaltet und steuert die Aktoren
des Konzepts. In diesem Fall steuert die SPS die Dosierung des Klebers, die Verfahreinheit und die Klebevorrichtung.
Verfahreinheit
Die Verfahreinheit bewegt die Klebevorrichtung über den Werkzeugträger und senkt die Klebevorrichtung ab. Um Kollisionen mit der Bandanlage zu vermeiden wird die ^
Klebevorrichtung nach dem Klebevorgang von der Bandanlage wegbewegt.
Dosierung Kleber
In der Teilaufgabe "Dosierung" wird der Klebstoff für einen Klebvorgang portioniert und zur Klebvorrichtung befördert.
Klebevorrichtung
In der Klebevorrichtung wird der dosierte Kleber in mehrere Klebeströme aufteilt und an die entsprechenden Klebepunkte geleitet.
Ablaufplan
Bei der Erstellung wurde bewusst auf Unterprogramme verzichtet, um alle Funktionen auf einer Ebene sichtbar zu halten. Der Klebevorgang beginnt für jeden neuen Untersetzter wieder von Beginn, sodass der hier dargestellt Ablauf einen Durchgang darsetllt. Der Ablauf wird also immer wieder zyklisch durchlaufen sobald ein neuer Werkstückträger an die Station kommt.
Nachfolgend ist der zyklische Ablauf vereinfacht dargestellt:
1) Der Werkstückträger erreicht die Station Kleben und gibt das Signal den Vorgang zu starten
2) Die Verfahreinheit fährt die Klebevorrichtung über das Förderband.
3) Die Klebevorrichtung wird abgesenkt bis sie kurz über dem Untersetzer schwebt.
4) Der Klebstoff wird dosiert und zum Untersetzer befördert.
5) Die Klebevorrichtung fährt wieder hoch und die Verfahreinheit fährt wieder in Die Grundstellung zurück.
6) Es wird ein Signal an die Bandanlage ausgegeben, dass der Werkstückträger weiterbefördert werden kann.
Hinweis: Falls der Klebstoff in der Spritze leer werden sollte kann der aktuelle Klebevorgang noch beendet werden und anschließend wird die Steuerung ausgesetzt und es wird eine Störung ausgegeben.
Auf der Basis dieses PAPs, welcher im Grunde einen Grafcet darstellt, erfolgt die Programmierung der SPS (siehe Abschnitt "Programmierung"). Mittels der SPS werden alle Funktionen der Station verwaltet.
Technischer Systementwurf
Beim technischen Systementwurf werden nun alle Beziehungen der Systeme untereinander klar. Ebenso werden die einzelnen Konzepte zur Umsetzung der gesamten Anlage dargestellt. Aus Abbildung xxx geht hierbei hervor, dass eine SPS als zentrales Steuerungselement fungiernen soll. Alle Sensorsignalen bzw. Inputsignale werden in der SPS eingelesen und verarbeitet. Analog dazu werden die Signale für alle Ausgänge von der SPS wieder ausgegeben und an die Aktoren übermittelt. Zu den Sensoren gehören drei mal je zwei Endlagen für PickALpha und zwei Pneumatikzylinder, sowie ein Signal von der Förderbandanlage. Die Ausgänge sind zum einen die Ansteuerung der Pneumatikzylinder, sowie die drei Relais um den PickAlpha im Vorwärts- und Rückwärtslauf zu betreiben. Ebenso ein Ausgnagssignal für die Bandanlage für die Information wenn ein Werkstück fertig bearbeitet ist.
Des Weiteren wird aus dem technischen Systementwurf deutlich wie die pneumtischen Schlatkreise aufgebaut sind. Die Druckluftversorgung speist zunächst eine zentrale Ventilinsel. Von dieser aus werden dann durch die zuvor beschriebene SPS die Pneumatikzylinder entsprechend angesteuert.
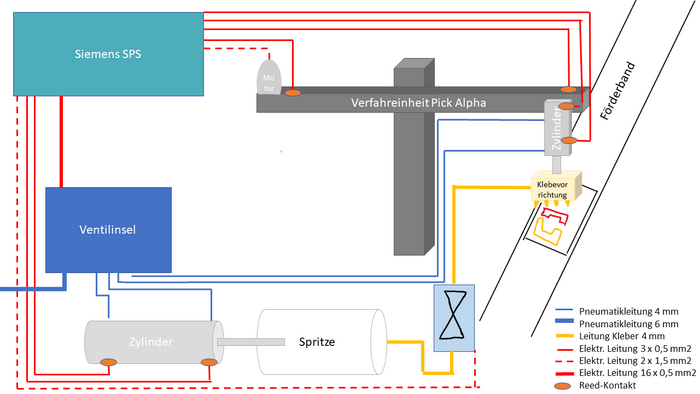
Um den Klebeprozess innerhalb der MPS-Anlage möglichst einfach und effizient umzusetzten sollte nun ein Konzept ausgearbeitet werden, was den Klebstoff auf den kommissionierten Warenträger aufträgt. Das Konzept wurde zunächst in mehrere verschiedene kleinere Systeme runtergebrochen:
1) Die Klebedosierung
Um den Klebstoff in einem präzisen und wiederholbaren Art und Weise durchzuführen wurde ein entsprechendes Konzept ausgearbeitet. Um dies zu gewährleisten wurde ein Pneumatikzylinder mit der Hubstange einer Spritze verbunden (siehe Abbildung xxx). Am Ende der Spritz wurde ein Schlauchanschluss befestigt, an welchem ein einfacher pneumatik Schlauch weiter bis zur Bandanlage mit den zu klebenden Bauteilen führte. Somit kann der Kleber mittels pneumatischer Beaufschlagung des Zylinders aus der Spritze zum Zielort gedrückt werden. Die stärke bzw. Geschwindigkeit des Klebstoffstrom kann hierbei über die Drosselrückschagventile des Zylinders justiert werden.
2) Die Klebevorrichtung
Die Klebevorrichtung soll als eine Art Verteilstation fungieren (siehe Abbildung xxx). Der Kleber kommt von der zuvor beschiebenen Klebedosage und gelangt an der oberen Seite in die Klebevorrichtung. Der Klebstoffstrom teilt sich hierbei auf und an der Unterseite treten dann an mehreren Stellen der Klebstoff aus Düsen aus. Somit soll eine bessere HAftung der einzelnen Bauteile des HSHL-Untersetzters gegeben sein.
3) Der Transport des Klebers & Klebevorrichtung
Mittels dem zu Verfügung gestellten PickAlpha wird die Klebevorrichtung und respektive der geförderte Kleber von der Station bis über das Förderband bewegt. Anschließend soll diese dann auf das Band präzise abgelassen werden. Dieses Konzept wird deshalb verfolgt, da so keine aufwendiger Transprot des Werkstückträger vom Förderband zur Station mehr gegeben ist, sondern der ganze Klebevorgang auf das Förderband verlagert wird. Somit sollte der Aufbau einfacher und der Ablauf zuverlässiger werden.
4) Die Steuerung der Anlage
Um die Dosierung des Klebers, die Steuerung des Pickalpha's sowie jedliche anderen Aktoren des Systems zu steueren und ab auch die Sensordaten auszuwerten wird die Anlage mittels Siemens SPS gesteuert.Dabei empfängt diese 7 Eingange und gibt SIgnale an 6 AUsgänge wieder aus. Welche diese sind ist in der Anschlusstabelle (Abbildung xxx) zu sehen.
Komponentenspezifikation
Nachdem die Schnittstellen und zu verwendenden Komponenten festgelegt wurden, müssen diese in der Komponentenspezifikation detaillierter betrachtet werden. Für die Schnittstelle Station und SPS wurden die einzelnen Ein- und Ausgänge definiert. Zusätzlich wurden die Spannungen und Ströme ermittelt. Diese erleichtern die spätere Verdrahtung der SPS, indem die Anschlussklemmen bereits vordefiniert werden.
Die Komponentenspezifikation wurde dabei auf die drei Stationen Transfer, Transport und Kleben aufgeteilt, wobei die benötigten Komponenten jeder Station festgelegt wurden. Des Weiteren wurde die SPS und die Versorgungseinheiten als zusätzliche Komponenten aufgenommen und durch sämtliche Ein-, Ausgänge und Bauteile definiert.
Entwicklung
Mechanik
Folgende Bauteile wurden mit Solid Works erstellt und mit einem FDM Drucker hergestellt.
-
Ausschieber des Zylinder 2
Dieser -
Ausschieber des Zylinder 3
Dieser -
Zylinderhalterung des Zylinder 2
Diese -
Zylinderhalterung des Zylinder 3
-
Verpackungsmagazin
Dieses
Elektrik
Programmierung
Um die gesamte Anlage zu steueren wird auf eine Siemens SPS ET200 zurückgegriffen. Nach einer anfänglichen Erstinbetriebnahme wurde die SPS mit dem auf dem PC installierten TIA Portal verbunden und das Programm programmiert.
Bei der Programmierung stellt sich zunächst die Schwierigkeit in welchem Funktionsbaustein das Programm geschrieben werden sollte. Die Auswahl fiel hierbei allerdings auf eine Schrittkettenprogrammierung. Dafür sprachen zum einen, dass die Station einen zyklischen Ablauf besitzt, welcher mittels Schrittketten sehr gut abgebildet werden kann. Zum anderen wurde zuvor im funktionalen/technischen Systementwurf der Ablauf sehr nahe eines Grafcets entworfen. Da die Schrittkettenprogrammierung im Grunde einen solchen Grafcet abbildet war es somit einfach diesen Ablaufplan in einem Programm abzubilden.
Der eigentlichen Ablauf der Schrittkette sieht fertiggestellt somit folgernder maßen aus:
1. Alle Bauelemente fahren in Grundstellung
2. Der Picklpha fährt über das Förderband aus.
3. Die Klebevorrichtung wird auf den kommissionierten Warenträger abgesenkt.
4. Der Dosierzylinder fährt aus und beaufschlagt Druck auf den Kleber.
5. Das Magnetventil öffnet für 2 Sekunden und der Kleber kann fließen.
6. Das Magnetventil schließt.
7. Die Klebevorrichtung wird wieder angehoben
8. Der Pickalpha fährt wieder in Grundstellung zurück
Zusatz: Sollte vor oder während eine Klebevorgangs der Klebstoffvorrat in der Spritze kritsch niedrig werden, gibt die Steuerung einen Fehler aus und fährt wieder in Grundstellung. Ein Weiterbetrieb ist dann erst möglich sobald Klebstoff augefüllt worden ist. Aktive Zyklen können jedoch aufgrund einer einkalkulierten Reserve noch beendet werden.
Komponententest
Innerhalb des Vorgangsschritts „Komponententest“ sollen die verwendeten Komponenten auf ihre Funktionsfähigkeit untersucht werden. Aufgrund fehlender Komponenten (durch Lieferungsverzug) konnte dieser Schritt in der Projektbearbeitung nicht mehr realisiert werden. Nachfolgend wird eine beispielhafte Testung eines Pneumatikzylinders beschrieben.
Testung eines Pneumatikzylinders:
- Befestigung des Zylinders an einer steifen, unnachgiebigen Oberfläche
- Verschlusskappen der Zylindereingänge entfernen
- Ventilanschlüsse einschrauben
- Drosseln der Ventilanschlüsse auf einen geringen Durchgangsfluss einstellen
- Druckluftschläuche in die Ventilanschlüsse einführen
- Druckluftschläuche in die Versorgungseinheit einführen → Versorgungseinheit vorher auf Sperrstellung stellen
- Sperrstellung der Versorgungseinheit langsam drehen, um Luftzufuhr zu generieren
- Verfahrrichtung der Kolbenstange kontrollieren
- Verfahrgeschwindigkeit und -verhalten der Kolbenstange kontrollieren
Die Testung gilt als erfolgreich, sobald die Kolbenstange der vorhergehenden Schaltung entspricht und die Stange ruckelfrei und ohne Geräuschentwicklung verfährt.
Komponente | Status | Datum | getestet von |
Induktiver Sensor am Förderband | nicht getestet | ||
Doppeltwirkender Druckluftzylinder 200mm | nicht getestet | ||
Doppeltwirkender Druckluftzylinder 150mm | nicht getestet | ||
Reedkontakte | nicht getestet | ||
Drosselrückschlagventile | nicht getestet | ||
Druckminderer mit Manometer | nicht getestet | ||
SPS-Netzteil | nicht getestet | ||
Schrittmotorachse | nicht getestet |
Integrationstest
Systemtest
Abnahmetest
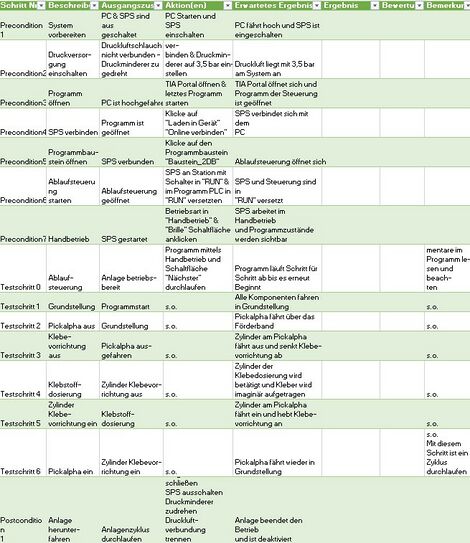
Nachdem die Station Kleben fertiggestellt wurde und alle Bauteile konstruiert, sowie montiert wurden und die gesamte Steuerung programmiert und verbunden worden ist, folgt nun der Abnahmetest. In diesem Test ist noch beschrieben wie ein erster Testlauf der gesamten Anlage durchgeführt werden kann. Jeder Schritt ist hierbei genau beschrieben. Der Test unterteilt sich im Detail in drei Hauptschritte:
1) Zu Beginn werden alle Schritte beschrieben um die Anlage in Betrieb zu nehmen. Dazu zählt zum Beispiel die Druckluftversorgung herzustellen, die SPS zu starten und das TIA Portal bzw. Programm zu öffnen.
2) Im Haupteil werden dann alle programmtechnischen Abläufe beschrieben und das Programm wird einmalig Schritt für Schritt durchlaufen. Dabei kann der Tester jede Funktion der Steuerung nachvollziehen und ebenso überprüfen und verifizieren. Dank des Handbetriebs werden alle Schritte der Schrittkette in dem Tempo ausgeführt in dem der Tester diese nachvollziehen bzw. kontrollieren kann.
3) Zu Schluss werden dann wieder alle Systeme runtergefahren und die elektrische sowie pneumatische Versorgung wird gekappt.
Ergebnis
Zum Ende des diesjährigen Praktikums wurde bereits eine nahezu vollständig funktionierende Anlage konstruiert. Vollständig in Betrieb sind somit schon die Klebstoffdosierung, die Ablaufsteuerung, die Ansteuerung des PickAlpha's sowie die Ansteuerung der Zylinder mittels Ventilinsel sowie die Einbindung aller Sensoren. Das System kann bereits eine reibungslosen "Trockenlauf" absolvieren in dem der Durchgang eines Zyklus bis auf die tatsächliche Ausgabe des Klebers erfolgt.
Einzig kleinere Ergänzungen wie der Einbau von Düsen in die Klebervorrichtung, sowie ein Testdurchlauf mit echtem Kleber sind noch durchzuführen. Alle für diese AUfgaben benötigten Teile wurden größtenteils bereits bestellt wurden jedoch noch nicht geliefert. Ebenso ist im SVN eine Anweisung erstellt in der genau beschrieben ist, welche Arbeiten noch zu erledigen sind, sobald alle Bauteile vorhanden sind, um die Anlage gänzlich fertig zu stellen.
Ausblick
Erfreulicherweise konnte die Anlage der Station Kleben somit nach dieser Umsetztung testweise in Betrieb genommen werden. Grundsätzlich funktioniert die ANlage also auch schon bereits, jeodch sind noch kleine Ergänzungen nötig, sowie ggf. noch ein paar Erweiterungen die die ANlage zusätzlich noch verbessern würden. Zu diesen zählen unter anderem:
1.) Eine Installation eines Magnetventils im Klebstoffstrom. Dieser hätte den Vorteil, dass der Zeitpunkt und ebenso die Zeitspanne, in welcher der Kleber auf den Untersetzter gespritzt wird genau definiert werden kann. Somit würde es kein Nachlaufen des Klebers oder ein zu frühes Austreten von diesem vorliegen.
2.) Ein weitere Aufgabe ist es ein passendes Adapterstück in die Spritze zu schrauben um den Pneumatikschlauch an diesem zu befestigen, welcher den Kleber dann erfolgreich an die Klebevorrichtung leiten würde.
3.) Ebenso können an der unteren Seite der Klebevorrichtung noch vier diesen eingebaut werden, sodass der Kleber präzise und emmissionsarm auf die Untersetzter aufgetragen werden kann.
4.) Außerdem muss die gesamte Anlage im Zusammenspiel mit allen anderen Stationen genau ausgerichtet werden, Das bedeutet, dass alle Endlage und die Station selber so ausgerichtet werden, dass der Klebevorrgang reibungslos abläuft und alle Bauteile berührungslos ein und ausfahren können.
5.) Ein weitere sehr wichtiger Punkt ist der Entwurf und die Fertigung eines Gehäuses/Befestigung für die Schutzbeschaltung des Motors. DIe Schaltung ist zurzeit noch lose auf dem Montagetisch angeordnet un benötigt zwangsläufig ein Gehäuse um den Bediener zu schützen und um einen zuverlässigen Betrieb zu ermöglichen.
6.)Ein weiteres To-Do ist es, ein HMI-Panel in das System zu integrieren. Es wurde bereits ein Halter zusammen mit den anderen Stationen entworfen und gefertigt, jedoch muss das Panel noch eingebaut werden, sowie in die Steuerung eingebunden werden.
7.) Ein letzte und wohl schlussendlich abschließende Aufgabe ist es einen realen Testdurchlauf mit einem ausgewählten Klebstoff durchzuführen. Eine passender Klbstoff wurde bereits gefunden, sodass nur noch die tatsächliche Tauglichkeit dieses Kleber überprüft werden muss. Möglich Probleme könnten die Verklebung von Bauteilen sein oder die ordnungsgemäße Förderung durch das gesamte Klebstoffsystem.
Verwendete Software
- Solid Works: Konstruktion der 3D-Druckteile und Erstellung benötigter Zeichnungen
- MS PowerPoint: Aufstellung des Konzepts, Erstellung des technischen Systementwurfs
- MS Excel: Erstellung der Anforderungsdefinition, Komponentenspezifikation
- PapDesigner: Erstellung des funktionalen Systementwurfs
- Siemens TIA-Portal V15.1: Erstellung des SPS-Programms
- TinyCAD: Erstellung der Schaltpläne
Verwendete Hardware
→ siehe Stückliste
Verwendete Komponenten der Station Kleben:
Funktion | Bezeichnung | Material | Hersteller | Anzahl | Preis | Beschreibung | Bild |
---|---|---|---|---|---|---|---|
Mechanik | - | Kunststoff | Eigenherstellung | 1 | - | Deckenplatte-Schutzkäfig | ![]() |
Mechanik | - | Plexiglas | Eigenherstellung | 4 | - | Seitenscheiben - Schutzkäfig | ![]() |
Mechanik | 3D-Druckteil | 3D-Druck-PLA Filament | Eigenherstellung | 4 | - | Käfigsäulen - Schutzkäfig | ![]() |
Mechanik | Bosch-Profil | - | Bosch | 2 | - | 45x45mm 4Kant-Boschprofil | ![]() |
Mechanik | 3D-Druckteil | 3D-Druck-PLA Filament | Eigenherstellung | 6 | - | Klebedüsen - Schutzkäfig | ![]() |
Mechanik | 3D-Druckteil | 3D-Druck-PLA Filament | Eigenherstellung | 1 | - | Traverse - Schutzkäfig | ![]() |
Mechanik | 3D-Druckteil | 3D-Druck-PLA Filament | Eigenherstellung | 1 | - | Förderer - Adapterplatte | ![]() |
Mechanik | 3D-Druckteil | 3D-Druck-PLA-Filament | Eigenherstellung | 4 | - | Führungssäule | ![]() |
Pneumatik | Normzylinder DSBC-Q-32-200-D3-PPVA-N3 | - | Festo | 1 | - | Doppeltwirkender Zylinder-32mm Kolben M6 Außengewinde, 200mm Hub-verdrehsicher | ![]() |
Pneumatik | Normzylinder DSBC-Q-32-150-D3-PPVA-N3 | - | Festo | 1 | - | Doppeltwirkender Zylinder-32mm Kolben M6 Außengewinde, 150mm Hub-verdrehsicher | ![]() |
Pneumatik | Ventilinsel VP10-VI | - | Festo | 1 | 347,98€ | 10P-10-2E-IC-N-A-GG+H2D | ![]() |
Pneumatik | Drossel-Rückschlagventil GRLA-1/8-QS-6-D | - | Festo | 4 | - | Abluft-Drossel-Rückschlagfunktion-einschraubbar-185l/min-0,2-10bar | ![]() |
Pneumatik | Druckregelventil LR-1/4-DB-7-MINI | - | Festo | 1 | - | Mini-44mm-Drehknopf mit Arretierung-Sekundärlüftung-mit Manometer | ![]() |
Elektrik | SPS | - | SIEMENS | 1 | - | 6EP7133-6AE00-0BN0 | ![]() |
Elektrik | Näherungsschalter SMT-8M-A-PS-24V-E-2,5-OE | - | Festo | 4 | - | T-Nut-magnetoresistiv-Schließer-Positionsmessung | ![]() |
Elektrik | Förderer | - | Igus | 1 | - | Schrittmotorachse | ![]() |
Lessons Learnd
Literaturverzeichnis
- ↑ https://wiki.hshl.de/wiki/index.php/Ampel-Demonstrator/ V-Modell Projekt Ampeldemonstrator
- ↑ https://catch.app/itm/v1%7C124881444190%7C425961454533
- ↑ https://www.festo.com/de/de/a/1463250/?q=1463250~:festoSortOrderScored&identCode1=DSBC-Q-32-200-D3-PPVA-N3
- ↑ https://www.festo.com/de/de/a/1463250/?q=1463250~:festoSortOrderScored&identCode1=DSBC-Q-32-200-D3-PPVA-N3
- ↑ https://www.festo.com/de/de/a/18200/?q=18200~:festoSortOrderScored&identCode1=10P-10-2E-IC-N-A-GG%2BH2D
- ↑ https://www.festo.com/de/de/a/193144/
- ↑ https://www.festo.com/de/de/a/539682/?q=539682~:festoSortOrderScored
- ↑ https://www.elektromax24.de/Siemens-Stromversorgung-SIMATIC-ET-200SP-PS-1phasig-DC-24V-5A?gclid=EAIaIQobChMI6fz8jbjh9QIVyO5RCh2WQwYGEAQYFiABEgKfZ_D_BwE
- ↑ https://www.festo.com/de/de/a/574335/
- ↑ https://www.igus-cad.com/default.aspx
→ zurück zum Hauptartikel: [Praktikum Produktionstechnik]