Modulares mechatronisches Produktionssystem (MPS): Station Roboter: Unterschied zwischen den Versionen
Keine Bearbeitungszusammenfassung |
|||
Zeile 11: | Zeile 11: | ||
Version vom 1. Februar 2022, 12:45 Uhr
Autor:
WS2019: Mareen Rehberg und Carolin Mohs
WS2021: Timo Malchus und Stefan Großecoßmann (beide: Erweiterung Akkumanagement-System)
WS2021: Dominik Schroeer und Nils Hartmann (beide: Inbetriebnahme Robotermontage)
Betreuer: Prof. Dr.-Ing. Göbel
Erweiterung Akkumanagement-System
Motivation
Die Ziele hinter dem Akkumangement-System sind, die Ausfälle des Stromnetzes, welche durch verschiedene hochschulinterne Tests immer wieder zu erwarten sind, zu eliminieren. Um solche Situationen zu überbrücken, wurde eine Umschalteinrichtung zwischen Netzteil und Akku entwickelt.
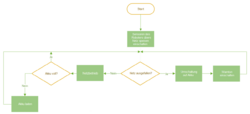
Als Ausfallsituationen sind folgende Ereignisse mit den dazugehörigen Ausfallzeiten zu erwarten:
- RCD-Test (1 Stunde)
- "Black-out-Tests" als hochschulinterne Stromabschaltung (3-4 Stunden)
- Stromausfall (15 Sekunden bis zur Betriebsbereitschaft des Diesel-Notstromaggregats)
Diese Akku-Management-Einheit soll im Netzbetrieb die Positionssensoren mit Spannung versorgen und den eingebauten Akku bei Bedarf, also nur im entladenden Zustand, laden. Fällt das Netz aus, soll automatisch auf Akkubetrieb umgeschaltet werden. Dabei gilt es eine verzögerungsfreie Umschaltung zu gewährleisten und nach außen eine akustische Warnung abzugeben (siehe Abb. 4). Diese soll dem Bediener aufzeigen, dass das Netz ausgefallen ist und die Positionssensoren jetzt nur noch eine begrenzte Zeit mit Spannung versorgt werden können, es sei denn, der Netz wird wieder aktiviert. Falls jemand den Stecker des Netzteils gezogen hat, ist die akustische Warnung ein Zeichen dafür, die Aktion sofort rückgängig zu machen.
Anforderungen zusammengefasst:
- Lückenlose Umschaltung zwischen Netz- und Akkubetrieb
- Aufladen des Akkus nur bei Bedarf
- Akkukapazität für mindestens vier Stunden
- Akku-Überwachung (Tiefentladeschutz, Überspannungsschutz, etc.)
- Ausgangsspannung: konstante 4,3V DC
- akustische Warnung bei Verlust der Netzspannung
Entwicklung der elektrotechnischen Einheit
Um die Anforderungen zu erfüllen wurde zuerst überlegt, wie so etwas kompakt, einfach und kostengünstig zu realisieren sein könnte. Dabei wurde entschieden, dass sich eine 5V-Ladeplatine in Kombination mit 3,7-Li-Ion-Akkus eignen würde. Diese Ladeplatine sollte auch die Umschaltung zwischen Netz und Akku übernehmen. Des Weiteren sollte ein zweites Netzteil, welches in einem zweiten Stromkreis mit einer anderen Fehlerstrom-Schutzeinrichtunng (RCD) betrieben wird, eingebaut werden. Dadurch können die Ausfallzeiten bei einem RCD-Test, die durch den Akku überbrückt werden würden, weiter verringert werden. Somit wird ein Netzteil an den "normalen" Stromkreis und das zweite an den EDV-Stromkreis (zu erkennen an den roten Steckdosen), siehe Abb. 5, angeschlossen. Mithilfe von zwei Schottky-Dioden, welche sich für den besonders geringen Spannungsabfall auszeichnen, wurde der Anschluss der beiden Netzteile ausgeführt. Die Pluspole der beiden Netzteile wurden über diese Schottky-Dioden zusammengeführt (siehe Abb. 6), die Minuspole können einfach miteinander verbunden werden. Durch den Einsatz der Dioden wird verhindert, dass die Spannung des einen Netzteils in das zweite Netzteil durchschlägt.
Die akustische Warnung erfolgt mit einem Summer, der über ein Relais geschaltet wird. Dies Relais ist beim Netzbetrieb dauerhaft aktiviert und unterbricht dann den Stromkreis zum Summer. Fällt das Netz nun aus, fällt das Relais ab und schließt den Stromkreis. Der Summer wird nun über den Akku mit Spannung versorgt. Ein Versuchsaufbau auf dem Breadboard ist in Abb. 6 zu sehen.
Eine Herausforderung für das Gesamtsystem war die niedrige Spannung der nur zum Teil geladenen Akkus. Dies Ausgangsspannung der Ladeplatine sollte eigentlich konstante 4,2V DC betragen, doch bei entleerten Akkus fiel diese auf bis zu 3,5V DC ab. Um das Problem zu beheben kommt ein Step-up-Wandler (DC/DC-Wander) zum Einsatz, der die Spannung, unabhängig von der Eingangsspannung bis minimal 0,9V DC, wieder auf konstanten 5V DC anhebt. Im Anschluss sorgt eine Diodenschaltung für einen Spannungsfall von 0,7V DC, sodass die angestrebten konstanten 4,3V DC dauerhaft erhalten bleiben.
Weiterhin sind verschiedenen Kondensatoren zur Glättung und Pufferung der Ausgangsspannung verbaut worden. Um die Konnektivität zwischen den einzelnen Modulen Akku, Steuerplatine, Ein- und Ausgänge zu gewährleisten, wurden MKDSN-Klemmen (Schraubklemmen) in Kombination mit Aderleitungen verwendet. So lassen sich die Module schnell und einfach voneinander trennen und einzeln testen.
Im Folgenden sind der Testaufbau mit dem Summer auf dem Breadboard, sowie die erstellten Aufbau- und Lötpläne für die Steuerplatine dargestellt.
Strombedarf & Kapazitätsberechnung
Um die Stromausfälle zu Überbrücken wird auf den Akku umgeschaltet. Der Akku muss so dimensioniert sein, dass er mindestens vier Stunden die Positionssensoren und den Summer versorgen kann.
Strombedarf der einzelnen Bauteile:
- Positionssensoren Roboter: ca. 400 mA
- Summer: ca. 30 mA
Damit wird ein Gesamtstrombedarf von 430 mA gebraucht. Der Wirkungsgrad der Akkus (aufgrund von Alterung, Selbstentladung etc.) wird auf 0,8 geschätzt. Mithilfe der nachfolgenden Formel soll die minimale Akkukapazität berechnet werden.
Für das Akkumangement-System sollen zwei 3,7V Li-Ion Akkus mit je 2600 mAh zum Einsatz kommen. Mit diesen Werten soll die Laufzeit überprüft werden beziehungsweise berechnet werden, wie lange das System akkubetrieben laufen würde. Die Variable n steht hier für die Anzahl an Akkus.
Mit der verfügbaren Kapazität wird das entwickelte System die oben genannten Ausfallzeiten überstehen.
Durchführung des Integrations- und Systemtests
Nachdem die Komponententests erfolgreich waren, konnte der Integrationstest durchgeführt werden. Mithilfe eines Oszilloskops wurde die Umschaltzeit, sowie der Verlauf der Gleichspannung überprüft. Die Umschaltzeit war gleich null, d.h. ein Einbrechen der Spannung war nicht erkennbar. Außerdem ist die Gleichspannung, dank der Kondensatoren, nur noch leicht wellig. Daraufhin konnte die Steuerplatine noch obrigem Plan (Abbildung 7+8) gelötet werden. Diese Platine wurde anschließend mit den anderen Komponenten verdrahtet. Nun konnte der Systemtest, der in Abb. 9 dargestellt ist, durchgeführt werden. Dieser war erfolgreich, d.h. es wurden alle Anforderungen erfüllt. Im Folgenden konnten die verschiedenen Einheiten in das dafür konzipierte Gehäuse, welches im kommenden Kapitel vorgestellt wird, eingebaut werden.
Entwicklung der mechanischen Einheit
Die mechanische Einheit wurde entwickelt, um die Steuer- und Akkuplatine leichter zu "händeln". Beide Komponenten können so leicht transportiert und gelagert werden. Außerdem bietet das Gehäuse Schutz vor Staub und ähnlichen Einflüssen von außen. Das mit einem CAD-Programm erstellte 3D-Druck-Gehäuse hat einen zweistöckigen Aufbau. Im unteren Teil ist die Steuerplatine mit dem Relais untergebracht. Die Platine wird dort auf vier dafür vorgesehene Sockel geschraubt, um einen festen Sitz zu garantieren. An den Wänden befinden sich Stützen, auf die, eine mit einer Auskerbung versehene Mittelplatte, gelegt werden kann. Darüber wird die Akkueinheit untergebracht. Die Auskerbung der Mittelplatte ist für die Verbindungsleitungen zwischen Steuerplatine und Akku vorgesehen. Geschlossen wir der Kasten mit einem Deckel, der mit vier Schrauben befestigt werden kann. Zu Designzwecken wurde dieser mit dem HSHL-Logo versehen.
An den Seitenwänden des Kastens sind Kabelverschraubungen angebracht. Diese dienen als Zugentlastung und staubfreien Trennung für die Netzteil-Leitungen und die Versorgungsleitung der Positionssensoren. Im Ergebnis ist der Schaltkasten eine gute Möglichkeit, die entwickelte Schaltung fest montiert und kompakt zu bewegen und dieses Akkumanagement-System einzusetzen.
Ergebnis
Zusammenfassend ist die Funktion des Akkumanagement-Systems vollständig gegeben. Als letzten Schritt müsste dieses System von einer Folgegruppe noch an den Roboter angeschlossen und in Betrieb genommen werden.
Stückliste
Für die meisten nachfolgend aufgelisteten Bauteile gibt es unter dem angegebenen Link ein Datenblatt. Für die restlichen Bauteile ist jeweils ein Datenblatt im SVN abgelegt.
Artikel | Anzahl | Anbieter | Artikelbezeichnung | Einzelpreis | Link |
DEBO3 3.7LI 1.0A Entwicklerboards - Ladeplatine für 3,7V Li-Akkus, Micro-USB, 1A | 1 | Reichelt | DEBO3 3.7LI 1.0A | 1,85€ | https://www.reichelt.de/de/de/entwicklerboards-ladeplatine-fuer-3-7v-li-akkus-micro-usb-1a-debo3-3-7li-1-0a-p291401.html?trstct=pos_0&nbc=1&&r=1 |
AKKU 22703 Li-Ion-Akku, 18650, 3,7 V, 2600 mAh, inkl. MicroUSB Ladebuchse | 2 | Reichelt | AKKU 22703 | 9,99€ | https://www.reichelt.de/li-ion-akku-18650-3-7-v-2600-mah-inkl-microusb-ladebuchse-akku-22703-p277525.html?&trstct=pos_1&nbc=1 |
KEYSTONE 1049 Batteriehalter für 2x 18650 | 1 | Reichelt | KEYSTONE 1049 | 5,10€ | https://www.reichelt.de/batteriehalter-fuer-2x-18650-keystone-1049-p213372.html?&trstct=pos_8&nbc=1 |
1N 5817 Schottkydiode, 20 V, 1 A, DO-41 | 2 | Reichelt | 1N 5817 | 0,05€ | https://www.reichelt.de/schottkydiode-20-v-1-a-do-41-1n-5817-p41848.html?&trstct=pos_0&nbc=1 |
GOOBAY 59029 Universal-Schaltnetzteil, 3 - 12 V, 1500 mA | 2 | Reichelt | GOOBAY 59029 | 11,20€ | https://www.reichelt.de/universal-schaltnetzteil-3-12-v-1500-ma-goobay-59029-p312479.html?&trstct=pos_2&nbc=1 |
KEPO KPMB-G2345L1-K6440 Miniatur Summer | 1 | Conrad Electronics | 715020 - YD | 1,61€ | https://www.conrad.de/de/p/kepo-kpmb-g2345l1-k6440-miniatur-summer-geraeusch-entwicklung-70-db-spannung-4-5-v-dauerton-1-st-715020.html |
2x USB Step Up Spannungsregler DC 0.9-5V auf 5V 600mA Boost Converter Modul | 1 | ebay | - | 3,95€ | https://www.ebay.de/itm/353437318551 |
1 Kanal Relais Relai 5V/230V Raspberry Pi Modul Channel Relay Arduino ESP8266 DI | 1 | ebay | - | 3,80€ | https://www.ebay.de/itm/154734331033?hash=item2406e28499:g:x8sAAOSwLvRhrJwm |
MKDSN-Klemmen, Kabelverschraubungen, Streifenrasterplatine, Schrauben, 3D-Druck, Kondensatoren, Gleichrichterdioden, Kabelbrücken | k.A. | HSHL | - | - | - |
Manuelle Bedienung
Um die Positionen des Roboters zu teachen muss der Roboter mit der Hand verfahren werden. Machen Sie sich mit der Robotersteuerung vertraut und verfahren Sie die Achsen.
Um den Roboter zu Verfahren muss der Totmanschalter auf der Rückseite der Teachbox in Stellung 1 sein (leicht reindrücken aber nicht durchdrücken).
Bilder sind in der Beschreibung vorhanden [6].
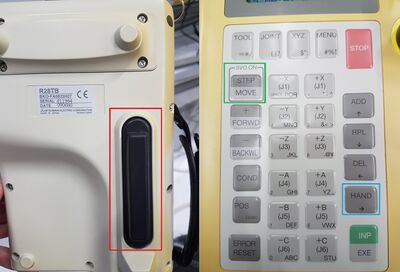
Tasten | Achsen |
---|---|
Totmanschalter & STEP/MOVE & X +/- (J1) | Roboterarm auf Sockel drehen |
Totmanschalter & STEP/MOVE & Y +/- (J2) | 1. Gelenk verfahren |
Totmanschalter & STEP/MOVE & Z +/- (J3) | 2. Gelenk verfahren |
Totmanschalter & STEP/MOVE & B +/- (J5) | 3. Gelenk verfahren |
Totmanschalter & STEP/MOVE & C +/- (J6) | Greifer drehen |
HAND & C +/- | Greifer öffnen/schließen |
Totmanschalter & STEP/MOVE & C +/- | Geschwindigkeit einstellen |
Hinweis:
Die Geschwindigkeit sollte geringer bleiben, damit eine Kollision rechtzeitig verhindert werden kann.
Literatur
- ↑ Datei: Datei:Programmablaufplan Akkumanagment.zip
- ↑ Datei: Datei:Technischer Systementwurf Akkumanagement.pptx (Originaldatei)
- ↑ Datei: Datei:Akkumangement Breadboard Fritzing.fzz (Originaldatei)
- ↑ Datei: Datei:Akkumangement Streifenrasterplatine Fritzing.fzz (Originaldatei)
- ↑ 5,0 5,1 Datei: Datei:CAD-Files Schaltkasten Akkumanagement.zip (Originaldateien)
- ↑ Datei: Datei:Manuelle Bedienung MPS.pdf