Produktion eines HSHL-Getränkeuntersetzers: Kommissionierung (Station 1)
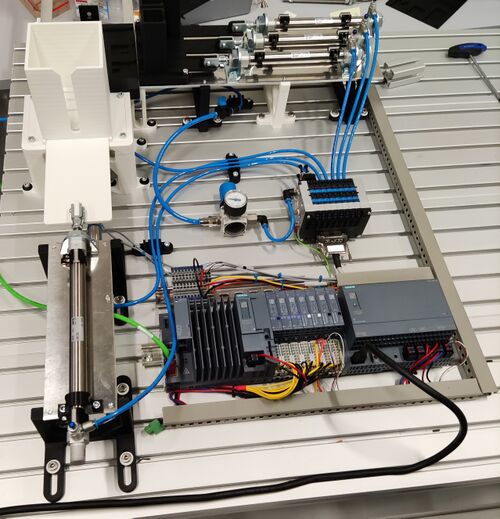
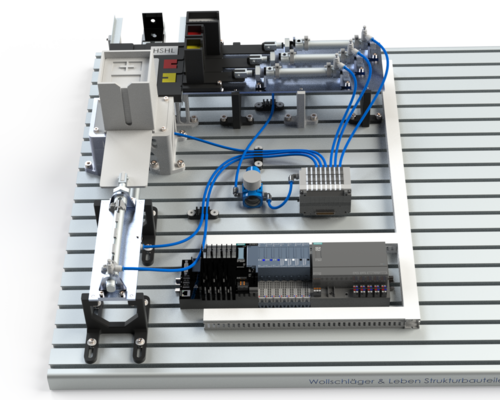
Autoren: Mario Wollschläger und Florian Leben
Dozent: Prof. Dr. Mirek Göbel
→ zum Hauptartikel: Mechatronisches Produktionssystem zur Produktion eines HSHL-Getränkeuntersetzers
→ zum Artikel des Praktikums: Praktikum Produktionstechnik
Einleitung
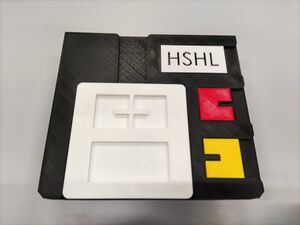
Im Rahmen des Studiengangs Mechatronik der Hochschule Hamm-Lippstadt wird im 7. Fachsemester das Praktikum Produktionstechnik als Teil des Moduls Global Production Engineering durchgeführt. In diesem Praktikum geht es um die Realisierung eines mechatronischen Produktionssystems (MPS) mittels Speicherprogrammierbarer Steuerung (SPS) sowie der Ansteuerung eines pneumatischen Systems im Rahmen des Projektes „Produktion eines HSHL-Getränkeuntersetzers“.
Gesamtkonzept
Produktion von HSHL-Getränkeuntersetzern als Werbegeschenk Produktion in 4 Stationen Verkettet über das bereits bestehende Förderband der MPS-Anlage
- Station 1: Kommissionierung
- Station 2: Kleber auftragen
- Station 3: Montage
- Station 4: Verpackung
Aufgabe der Station
Die Aufgabe der Station 1 ist, Warenträger vom Förderband mit Teilen zu bestücken. Auf dem Warenträger sind dafür vorgefertigte Plätze für die Teile vorhanden. Das zu erzielende Endresultat ist in der Abbildung rechts zu erkennen.
Anforderungsdefinition
Zu Beginn wurden verschiedene Anforderungen definiert, welche die Station erfüllen soll.
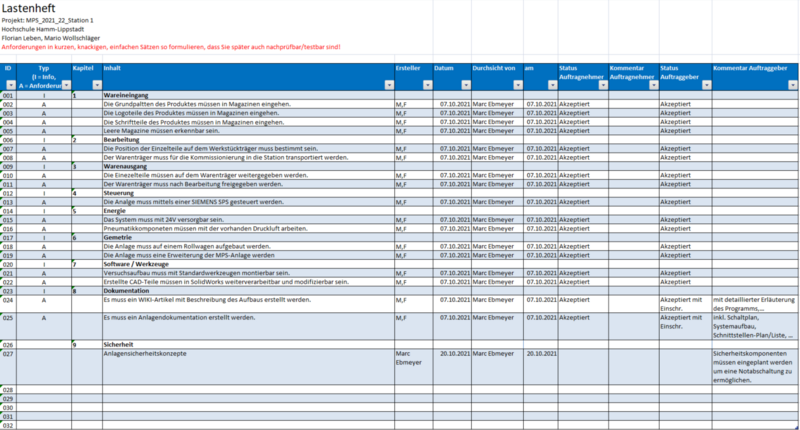
Originaldatei: Datei:MPS1-Anforderungen.xlsx
funktionaler Systementwurf
Im funktionalen Systementwurf wird die Fertigungsaufgabe in kleine Teilaufgaben runtergebrochen. Für die vorliegen Station teilt sich die Aufgabe in das Entnehmen des Warenträgers (WTs) vom Förderband, das Positionieren der Einzelteile und das anschließende Rückführen und weitergeben des WTs. Das Positionieren kann hierbei weiter unterteilt werden in das Speichern vereinzeln und genaue Positionieren auf dem WT.
-
Funktionaler Systementwurf
-
Positionierung
-
Positionierung am Beispiel Logo Links
Originaldatei: Datei:MPS1-FS.pptx
technischer Systementwurf
Im Anschluss an den funktionalen Systementwurf wird das System genauer spezifiziert. Im Folgenden sind die geplanten Komponenten mit Ein- und Ausgängen dargestellt. Zudem ist eine Gesamtübersicht mit allen relevanten Verbindungen und ein Lageplan abgebildet.
-
Legende
-
Systemübersicht
-
Haltevorrichtung
-
Magazin
-
Entnahme
-
Ventilblock
-
SPS
-
Lageplan
Originaldatei: Datei:MPS1-TSE.pptx
Komponentenspezifikation
Nach dem technischen Systementwurf können die einzelnen Komponenten genauer spezifiziert werden. Das Hauptaugenmerk liegt hierbei auf den mechanischen Komponenten, welche in groben Skizzen vor konzipiert werden. In diesen Skizzen wird das Wirkprinzip dargestellt und ein Konzept ausgearbeitet. Diese Skizzen sind für das Magazin und die Entnahmevorrichtung unten dargestellt. Für die restlichen Komponenten wurden Eigenschaften aufgenommen. Neben der Mechanik wurde ebenfalls die Programmierung vor konzipiert. Hierfür wurde ein Programmablaufplan erstellt, welcher als Basis für die spätere Programmierung dient.
-
Magazine
-
Entnahme
-
Programmablaufplan
Originaldateien:
- Entnahme: Datei:MPS1-KSpec-Entnahmen.xlsx
- Haltevorrichtung: Datei:MPS1-KSpec-Haltevorrichtung.xlsx
- Magazin: Datei:MPS1-KSpec-Magazin.xlsx
- SPS: Datei:MPS1-KSpec-SPS.xlsx
- Ventilblock: Datei:MPS1-KSpec-Ventilblock.xlsx
Gesamtsystem der Komissionierung
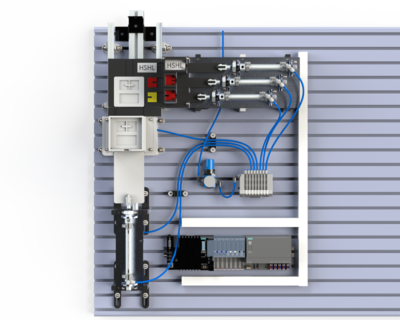
Die Aufgabe der ersten Station liegt darin, die Einzelteile für den HSHL-Getränkeuntersetzter auf dem WT zu platzieren. Neben der Mechanik werden noch weiter Komponenten benötigt. So werden die mechanischen Komponenten durch Druckluft bewegt, weshalb ein pneumatisches System aufgebaut wird. Dieses besteht einerseits aus den Druckluftzylindern selbst, andererseits jedoch auch aus Ventilen. Die Ventile werden elektrisch angesteuert. Für die Steuerung wird eine SPS verwendet. Im Folgenden sind die mechanischen Komponenten, das pneumatische System und die Programmierung des SPS genauer erläutert.
Im folgenden Ordner ist das gesamte CAD-Modell zu finden: Datei:MPS1-CAD.zip
Mechanische Komponenten
Zur Umsetzung der Fertigungsaufgabe werden mehrere mechanische Komponenten benötigt. Diese Komponenten bestehen einerseits aus einer Mechanik zum Entnehmen und Rückführen des WTs (Wahrenträgers) vom und auf das Förderband. Die Funktion wird durch die Komponente Entnahmevorrichtung umgesetzt. Andererseits müssen die einzelnen Bauteile auf den WT aufgebracht werden und zuvor gespeichert werden. Diese Funktion wird durch Magazine mit integriertem Auswerfer umgesetzt. Hierbei sind die Magazin eins bis drei zu einer Komponente zusammengefasst, währen das vierte Magazin eine separate Komponente darstellt.
Entnahmevorrichtung

Die Entnahmevorrichtung nimmt den WT (Warenträger) vom Wagen auf dem Förderband auf und verschiebt diesen in die Station, wo dieser dann bearbeitet werden kann. Hierfür greift ein gedrucktes Kunststoffteil, die Entnahmenase, in die Nase des WTs ein und zieht das gesamte Teil an dieser Nase in die Station. Sowohl der WT als auch die das Kunststoffteil werden von zwei T-Profilen geführt. Auf diese Weise wird einerseits die Position des WTs in der Station definiert, andererseits wird ein Verdrehen der Entnahmenase verhindert.
Die notwendige Bewegung in der Station wird durch einen Druckluftzylinder mit 300 mm Hub umgesetzt. Da nicht der volle Fahrweg des Zylinders benötigt wird, ist eine Begrenzung in Form von Anschlägen verbaut. Im eingefahrenen Zustand dient hierfür der interne Anschlag des Zylinders, im ausgefahrenen Zustand wird eine Konstruktion aus Boschprofilen und entsprechenden Winkeln verwendet. Diese Ausführung ermöglicht eine genaue Anpassung an den Abstand zum Förderband. Der doppeltwirkende Zylinder ist mit Reed-Kontakten versehen, welche die Endlagen des Zylinders erkennen. Hierdurch kann die Position der Entnahmenase bestimmt werden, was für die später beschriebene Programmierung wichtig ist.
Sensoren zur Endlageerkennung
Magazin 1 bis 3 (Kleinteilmagazin)
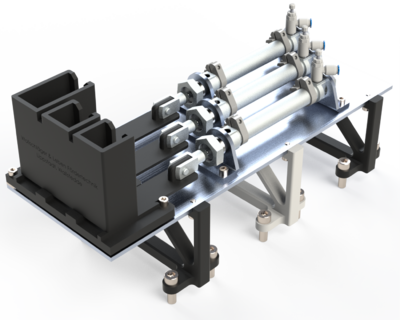
Die Magazine für die Kleinteile des Untersetzers befinden sich im Magazin 1 bis 3. Die drei Magazine sind aufgrund der räumlichen Nähe der Bauteile auf dem Warenträger zu einem Magazinblock zusammengefasst. Die Magazine ermöglichen ein geordnetes Speichern der Einzelteile in einer definierten Position. Das Nachrücken der Einzelteile erfolgt mittels Gravitation, sodass immer ein Bauteil am Auswurffenster vorhanden ist. Das Nachfüllen der Magazine erfolgt über die obigen Öffnungen und wird durch eine Aussparung an der Rückseite vereinfacht. Diese Öffnungen zeigen zeitgleich den Füllstand des Magazins an, damit der Bediener der Station weiß, wann die Magazine rechtzeitig nachzufüllen sind. Der Auswurf der Bauteile auf den Warenträger erfolgt über Schieber, welche federrückgestellte Druckluftzylinder angesteuert werden. Die Schieber besitzen jeweils eine individuelle Länge, die auf die Bauteile angepasst ist. Die drei Zylinder haben einen Hub von 100 mm und sind nebeneinander leicht versetzt, auf einer Trägerplatte angeordnet und mit einem Drosselrückschlagventil ausgestattet, um die Fahrgeschwindigkeit regulieren zu können.
Magazin 4 (Grundplatte)
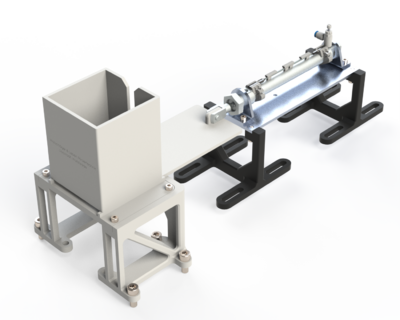
Das Magazin 4 speichert die Grundplatte des Untersetzers. Es entspricht vom Aufbau und Wirkprinzip her dem Magazin 1 bis 3. Jedoch hat dieses Magazin aufgrund des größeren Bauteils einen größeren Fahrweg, welcher durch einen größeren Zylinder realisiert wird. Diese Komponente ist in das Magazin und die Stützen unterteilt, was eine schnellere Iteration ermöglicht. Zudem bildet das Magazin 4 den Aufnahmepunkt für die Entnahmekomponente.
Pneumatik
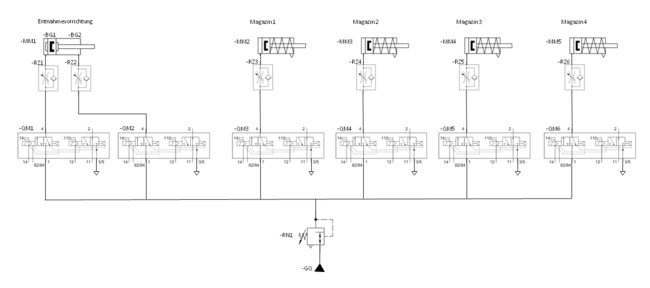
Die Station ist über einen Standard Druckluftanschluss an das Versorgungsnetz der Hochschule mit einem Druck von 8 Bar angeschlossen. Um den Druck der Station individuell zu regulieren, ist ein Druckminderer (RN1) vorgeschaltet. Die Ansteuerung der Zylinder erfolgt über eine Ventilinsel, welche mit mehreren Ventilmodulen bestückt ist. Die Schaltsignale erhält die Ventilinsel von der SPS. Die verwendeten Module der Ventilinsel sind jeweils mit zwei 3/2-Wege-Ventilen ausgestattet. Der Zylinder der Entnahmevorrichtung ist ein doppeltwirkender Zylinder (MM1), sodass für dessen Ansteuerung zwei Ventile (QM1 & QM2) verwendet werden, jeweils eins für das Ausfahren und eins für das Einfahren des Zylinders. Um die Fahrgeschwindigkeit des Zylinders in beide Richtungen einstellen zu können, wurde bei beiden Eingängen des Zylinders ein Drosselrückschlagventil (RZ1 & RZ2) eingebaut. Die Drosselrückschlagventile begrenzen den Durchfluss in eine Richtung und lassen in der entgegengesetzten Richtung den vollen Durchfluss zu, sodass eine Fahrrichtung in der eingestellt werden kann und der Zylinder beispielsweise langsam ausfährt und schnell wieder einfährt. Zudem verfügt der Zylinder der Entnahmevorrichtung über zwei Endschalter (BG1 & BG2), um die Position der Kolbenstange im Prozess bestimmen zu können. Die Zylinder der Magazine (MM2 - MM5) werden grundlegend nach dem gleichen Prinzip angesteuert und deshalb nur einmal anhand von Magazin 1 (MM2) erläutert. In den Magazinen sind Federrückgestellte Zylinder verbaut, was bedeutet, dass die Zylinder nur einen Anschluss haben und sobald Druckluft auf den Eingang gegeben wird, der Zylinder ausfährt. Wird der Eingang drucklos geschaltet, fährt der Zylinder mittels eingebauter Feder wieder in die Ursprungsposition zurück. Auch die Zylinder der Magazine sind mit einem Drosselrückschlagventil (RZ3 - RZ6) ausgestattet, um die Fahrgeschwindigkeit zu reduzieren.
Die Referenzkennzeichnung der Komponenten erfolgt nach EN 81346-2.
Elektrik
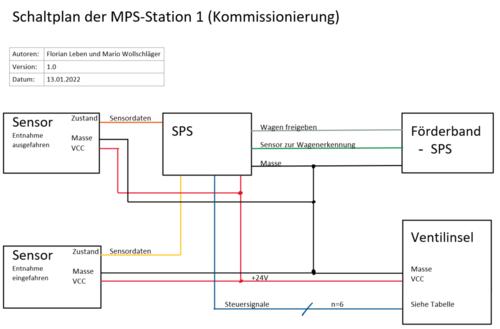
Im folgenden Schaltplan (rechts) ist die Verkabelung der Station beschrieben. Die genaue Belegung der einzelnen Anschlüsse sowie die Belegung der Anschlüsse der Ventilinsel sind der Anschlusstabelle zu entnehmen.
ID | Typ | Modul | Adresse | SPS-Adresse | Ventil li nach re | Zylinder | Ventilinsel-Anschluss | Beschreibung | Kabel |
1 | Output | 7 | 0 | A7.0 | 1 | 1 | 14 | Magazin 1 | Grau |
2 | Output | 7 | 1 | A7.1 | 2 | 2 | 14 | Magazin 2 | Weiß |
3 | Output | 7 | 2 | A7.2 | 3 | 3 | 14 | Magazin 3 | Braun |
4 | Output | 7 | 3 | A7.3 | 6 | 4 | 14 | Magazin 4 | pink |
5 | Output | 8 | 0 | A8.0 | 4 | 0 | 14 | Entnahme einfahren | Grün |
6 | Output | 8 | 1 | A8.1 | 5 | 0 | 14 | Entnahme ausfahren | Gelb-Braun |
7 | Output | 8 | 2 | A8.2 | - | - | - | Wagen freigeben | Grau |
8 | Input | 6 | 0 | E6.0 | - | 0 | eingefahren | Entnahme | |
9 | Input | 6 | 1 | E6.1 | - | 0 | ausgefahren | Entnahme | |
10 | Input | 6 | 2 | E6.2 | - | - | - | Sensor für Wagenerkennung | Grün |
Programmierung
Das Programm, welches die Station kontrolliert, läuft auf der Siemens SPS. Die verwendete Programmiersprache ist FUP (kurz für Funktionsplan), welche Netzwerke in grafischer Form beschreibt. Diese Netzwerke entsprechen dabei weitestgehend den Logikgattern der Digitaltechnik. So können beispielsweise Eingangsvariablen mit UND-Gattern verknüpft werden oder Zustände durch RS-Flipflops gespeichert werden. Als Eingangsvariablen können entweder die digitalen Eingänge der SPS verwendet werden oder interne Variablen/Merker.
Für die Anlage der Station 1 sind die Funktionen in verschiedene Netzwerke aufgeteilt. Beispielsweise wird mit Netzwerk 2 das Ausfahren der Entnahmestation gesteuert. Hierfür werden der Eingang E9.0, welcher an den Sensor des Entnahmezylinders angeschlossen ist, und der Merker M1.1 ausgelesen. Dieser wird von anderen Netzwerken beschrieben und gibt an, ob der WT in der Station bestückt wurde. Diese beiden Signale werden und-verknüpft, sodass wenn beide den logischen Wert 1 besitzen der S-Eingang eines SR-Flipflops gesetzt wird. Dieser speichert das Signal und sein Ausgang Q bleibt anschließend solange auf 1, bis der Eingang R1 des SR-Flipflops auf 1 gesetzt wird. Dann schaltet er zurück auf 0. Beim SR-Glied ist im Gegensatz zum RS-Glied der Eingang R1 dominant gegenüber dem Eingang S. Dies wird durchgeführt, sobald die Entnahme ausgefahren ist, ausgelesen durch den Sensor am Entnahmezylinder, angeschlossen am Eingang E9.1. Der Ausgang des SR-Flipflops wird mit eine Identität verschaltet, welche mit dem Ausgang A5.1 verkoppelt ist. Auf diese Weise wird der Ausgang A5.1 geschaltet, welcher die Ventilinsel ansteuert und dort das Ventil für das Ausfahren der Entnahmestation schaltet.
-
Entnahme einfahren
-
Entnahme ausfahren
-
Bestücken des WTs
-
Hilfsnetzwerk
Im folgenden Ordner ist die Programmierung der SPS zu finden: Datei:MPS1-SPS.zip
Test der Station
Komponententest
Zu Beginn werden die einzelnen Komponenten für sich getestet. Dafür wurden Kriterien überprüft, welche unten zu sehen sind.
Originaldokumentation: Datei:MPS1-Komponententest.xlsx
SPS
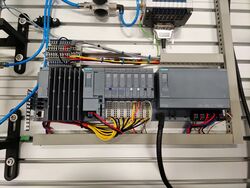
ID | Beschreibung | Status | Datum | Prüfer |
1 | Verbindung mit Computer | i.O. | 25.11.2021 | FL & MW |
2 | Ausführen eine Programmes | i.O. | 02.12.2021 | FL & MW |
3 | Einlesen von digitalen Inputs | i.O. | 09.12.2021 | FL & MW |
4 | Schreiben von digitalen Outputs | i.O. | 09.12.2021 | FL & MW |
5 | Software vollstänig | i.O. | 23.12.2021 | FL & MW |
Ventilinsel

ID | Beschreibung | Status | Datum | Prüfer |
1 | Anschließen an die Druckluftversorgung | i.O. | 16.12.2021 | FL & MW |
2 | Manuelle Betätigung | i.O. | 16.12.2021 | FL & MW |
3 | Elektrische Betätigung | i.O. | 23.12.2021 | FL & MW |
Entnahme
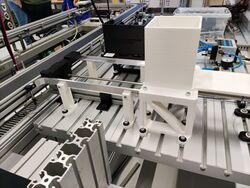
ID | Beschreibung | Status | Datum | Prüfer |
1 | Manuelles verschieben eines WTs | i.O. | 23.12.2021 | FL & MW |
2 | Pneumatisches verschieben eines WTs | i.O. | 23.12.2021 | FL & MW |
3 | Entnahme vom Förderband | i.O. | 06.01.2022 | FL & MW |
4 | Rückführung aufs Förderband | i.O. | 06.01.2022 | FL & MW |
Magazin 1 bis 3
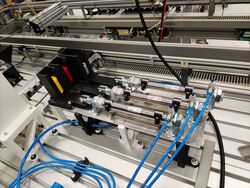
ID | Beschreibung | Status | Datum | Prüfer |
1 | Zylinder ausfahren | i.O. | 23.12.2021 | FL & MW |
2 | Zylinder einfahren | i.O. | 23.12.2021 | FL & MW |
3 | Teil auswerfen | i.O. | 23.12.2021 | FL & MW |
4 | Teil nachrücken | i.O. | 23.12.2021 | FL & MW |
5 | sequenziertes Teil auswerfen | i.O. | 23.12.2021 | FL & MW |
Magazin 4

ID | Beschreibung | Status | Datum | Prüfer |
1 | Zylinder ausfahren | i.O. | 23.12.2021 | FL & MW |
2 | Zylinder einfahren | i.O. | 23.12.2021 | FL & MW |
3 | Teil auswerfen | i.O. | 23.12.2021 | FL & MW |
4 | Teil nachrücken | i.O. | 23.12.2021 | FL & MW |
5 | sequenziertes Teil auswerfen | i.O. | 23.12.2021 | FL & MW |
Integrationstest
Der Integrationstest wird durchgeführt, um das Zusammenspiel verschiedener Komponenten des System zu prüfen.
Originaldokumentation: Datei:MPS1-Integrationstest.xlsx
SPS zu Ventilinsel
Durch einfache Netzwerke, welche beim Start der SPS Ausgänge auf logisch 1 setzen, wurde die Funktion der Schnittstelle zwischen SPS und Ventilinsel überprüft. Dabei wurden alle Ventile, welche im späteren Betrieb der Station verwendet werden, aktiviert. Die Funktionsweise der Ventile wurde durch die Indikations-LED auf der Ventilinsel und durch den Druckausgang überprüft. Alle Tests verliefen erfolgreich, wie der folgenden Tabelle zu entnehmen ist.
ID | Beschreibung | Status | Datum | Prüfer |
1 | elektrische Verbindung | i.O. | 16.12.2021 | FL & MW |
2 | Ansteuerung Ventil 1 | i.O. | 16.12.2021 | FL & MW |
3 | Ansteuerung Ventil 2 | i.O. | 16.12.2021 | FL & MW |
4 | Ansteuerung Ventil 3 | i.O. | 16.12.2021 | FL & MW |
5 | Ansteuerung Ventil 4 | i.O. | 16.12.2021 | FL & MW |
6 | Ansteuerung Ventil 5 | i.O. | 16.12.2021 | FL & MW |
7 | Ansteuerung Ventil 6 | i.O. | 16.12.2021 | FL & MW |
Ventilinsel zu Magazin
Für diesen Integrationstest wurde die Ventilinsel an die Druckluftversorgung angeschlossen und die Ventile anschließend per Hand mit einem Schraubendreher betätigt. Dabei wurde kontrolliert, ob am jeweiligen Ausgang Druckluft ausströmt. Anschließend wurden die Druckluftleitungen zu den Magazinen gelegt und an der Ventilinsel und den Zylindern angeschlossen. Durch das manuelle Betätigen der Ventile wurden die Magazine auf Funktion überprüft. So wurden die Magazine mehrmals per manueller Betätigung ein- und ausgefahren. Während dieses Vorgangs wurden die Drosselrückschlagventile der Zylinder eingestellt, um die optimale Fahrgeschwindigkeit zu verwenden.
ID | Beschreibung | Status | Datum | Prüfer |
1 | Magazin 1 | i.O. | 16.12.2021 | FL & MW |
2 | Magazin 2 | i.O. | 16.12.2021 | FL & MW |
3 | Magazin 3 | i.O. | 16.12.2021 | FL & MW |
4 | Magazin 4 | i.O. | 16.12.2021 | FL & MW |
Ventilinsel zu Entnahme
Der Test entspricht in seiner Durchführung dem Test von "Ventilinsel zu Magazine".
ID | Beschreibung | Status | Datum | Prüfer |
1 | Ausfahren | i.O. | 16.12.2021 | FL & MW |
2 | Einfahren | i.O. | 16.12.2021 | FL & MW |
Magazin zu Entnahme
Es wurde die Position der Magazine zum WT in der eingefahrenen Entnahme getestet. Hierbei wurden die Magazine manuell betätigt.
ID | Beschreibung | Status | Datum | Prüfer |
1 | Magazin 1 | i.O. | 23.12.2021 | FL & MW |
2 | Magazin 2 | i.O. | 23.12.2021 | FL & MW |
3 | Magazin 3 | i.O. | 23.12.2021 | FL & MW |
4 | Magazin 4 | i.O. | 23.12.2021 | FL & MW |
Systemtest
Originaldokumentation: Datei:MPS1-Systemtest.xlsx
ID | Typ (I = Info, A = Anforderung) | Kapitel | Inhalt | Kommentar Auftraggeber | Status | Prüfer | Komentar |
001 | I | 1 | Wareneingang | ||||
002 | A | Die Grundplatten des Produktes müssen in Magazinen eingehen. | i.O. | M,F | |||
003 | A | Die Logoteile des Produktes müssen in Magazinen eingehen. | i.O. | M,F | |||
004 | A | Die Schriftteile des Produktes müssen in Magazinen eingehen. | i.O. | M,F | |||
005 | A | Leere Magazine müssen erkennbar sein. | i.O. | M,F | Erkennung bisher optisch durch Mitarbeiter. In der nächsten Ausbaustufe sollten Sensoren verwendet werden | ||
006 | I | 2 | Bearbeitung | ||||
007 | A | Die Position der Einzelteile auf dem Werkstückträger muss bestimmt sein. | i.O. | M,F | |||
008 | A | Der Warenträger muss für die Kommissionierung in die Station transportiert werden. | Ausstehend | M,F | Neue WT-Unterseite fehlt | ||
009 | I | 3 | Warenausgang | ||||
010 | A | Die Einzelteile müssen auf dem Warenträger weitergegeben werden. | i.O. | M,F | |||
011 | A | Der Warenträger muss nach Bearbeitung freigegeben werden. | Ausstehend | M,F | |||
012 | I | 4 | Steuerung | ||||
013 | A | Die Anlage muss mittels einer SIEMENS SPS gesteuert werden. | i.O. | M,F | |||
014 | I | 5 | Energie | ||||
015 | A | Das System muss mit 24V versorgbar sein. | i.O. | M,F | Netzteil innerhalb der SPS | ||
016 | A | Pneumatikkomponenten müssen mit der vorhanden Druckluft arbeiten. | i.O. | M,F | |||
017 | I | 6 | Geometrie | ||||
018 | A | Die Anlage muss auf einem Rollwagen aufgebaut werden. | i.O. | M,F | |||
019 | A | Die Anlage muss eine Erweiterung der MPS-Anlage werden | i.O. | M,F | |||
020 | I | 7 | Software / Werkzeuge | ||||
021 | A | Versuchsaufbau muss mit Standardwerkzeugen montierbar sein. | i.O. | M,F | |||
022 | A | Erstellte CAD-Teile müssen in SolidWorks weiterbearbeitbar und modifizierbar sein. | i.O. | M,F | |||
023 | I | 8 | Dokumentation | ||||
024 | A | Es muss ein WIKI-Artikel mit Beschreibung des Aufbaus erstellt werden. | mit detaillierter Erläuterung des Programms,… | Ausstehend | in Bearbeitung | ||
025 | A | Es muss ein Anlagendokumentation erstellt werden. | inkl. Schaltplan, Systemaufbau, Schnittstellen-Plan/Liste, … | Ausstehend | in Bearbeitung | ||
026 | 9 | Sicherheit | |||||
027 | Anlagensicherheitskonzepte | Sicherheitskomponenten müssen eingeplant werden um eine Notabschaltung zu ermöglichen. | Ausstehend | Niedervoltsystem mit geringem Druck (2 Bar), Sicherheitskonzept sollte für Gesamtanlage erstellt werden. |
Abnahmetest
Der Abnahmetest der Station lief im autarken Betrieb durchweg positiv. Alle Komponenten arbeiten, wie in den Anforderungen beschrieben und die Kommissionierung erfolgt wie gewünscht. Die Feineinstellung der Drosselrückschlagventile und des Systemdrucks muss im Betrieb noch erfolgen. Die Integration in das Gesamtsystem und der Steuerung der MPS-Anlage ist zum Teil abgeschlossen. Die Freischaltung zum weiterfahren des Wagens ist schon verdrahtet und in die Software eingebunden, muss allerdings noch getestet werden. Die gesamte Hardware, also der mechanische, elektrische und pneumatische Teil der Anlage, ist somit fertiggestellt, lediglich die Software muss noch an die kurzfristigen Änderungen der Anforderungen verifiziert werden.
Bauteile
Zylinder
Es wurden drei verscheiden Druckluftzylinder in der Station verbaut:
Artikelname | Bestellnummer | Lieferant | Preis | Anzahl | Komponente | Beschreibung | Bild |
---|---|---|---|---|---|---|---|
300mm Zylinder | DSNU-20-300-PA | Festo | 35,04€ | 1 | Entnahme | Doppeltwirkender Zylinder mit 20mm Kolbendurchmesser, 300mm Hub und Magnet zur Positionserkennung im Kolben | ![]() |
150mm Zylinder | 206111200150 | Esska | 67,66€ | 1 | Magazin 4 | SMC CM2B20-150SZ:
Einfachwirkender, federrückgestellter Zylinder mit 20mm Kolbendurchmesser und 150mm Hub
|
![]() |
100mm Zylinder | 206111200100 | Esska | 59,50€ | 3 | Magazin 1 bis 3 | SMC CM2B20-100SZ:
Einfachwirkender, federrückgestellter Zylinder mit 20mm Kolbendurchmesser und 100mm Hub
|
![]() |
Für die Befestigung und Positionserkennung wurden die folgenden Komponenten verwendet:
Artikelname | Bestellnummer | Lieferant | Preis | Anzahl | Zylinder | Beschreibung | Bild |
---|---|---|---|---|---|---|---|
Reedkontakt | SME-8M-DS-24V-K-2.5-OE | Festo | 13,88 € | 2 | Entnahme | Sensor zur Erkennung der Position des Kolbens im Zylinder, über den verbauten Magneten | ![]() |
Sensorbefestigung | SMBR-8-20 | Festo | 2,54€ | 2 | Entnahme | Befestigung für den Sensor | ![]() |
Gabelkopf | SG-M8 | Festo | 2,21€ | 4 | Alle Zylinder | Gabelkopf | ![]() |
Zylinderbefestigung | HBN-20/25X2 | Festo | 3,45€ | 5 | Alle Zylinder | Zylinderbefestigung | ![]() |
Drosselrückschlagventil | GRLA-1/8-QS-6-RS-D | Festo | 8,83€ | 6 | Alle Zylinder | Drosselrückschlagventil | ![]() |
Ventilstation
Zur pneumatischen Ansteuerung der Druckluftzylinder wurde eine Ventilinsel des Herstellers Festo mit der Bezeichnung CPV10-G verwendet. Mit einem Druckluftanschluss können so bis zu 16 Ausgänge gesteuert werden. Die Ventilinsel besitzt acht Steckplätze für Ventilmodule. Jedes der Module kann zwei Ausgänge schalten.
Datenblatt: Datei:MPS1-Db-Ventilinsel.pdf
Artikelname | Bestellnummer | Lieferant | Preis | Anzahl | Komponente | Beschreibung | Bild |
---|---|---|---|---|---|---|---|
Ventilstation | 10P-10-8A-MP-N-U-HPHP6N | Festo (HSHL) | 826,09€ | 1 | Ventilinsel | Steuert die Druckluft und somit die Druckluftzylinder | ![]() |
Druckminderer | LR-1/4-DB-7-MINI | Festo | 17,56€ | 1 | Ventilinsel | Druckminderer: Verringert den Druck | ![]() |
Für das Adapterkabel wurde ein 25-poliges Kabel verwendet, bei dem dann nicht alle Adern belegt sind.
Pin | Farbe | Ventilplatz | Anschluss | Potential |
1 | Grau | 1 | 14 | 24V |
2 | Grau-Braun | 1 | 12 | 24V |
3 | Weiß | 2 | 14 | 24V |
4 | Grau-Pink | 2 | 12 | 24V |
5 | Braun | 3 | 14 | 24V |
6 | Braun-Grün | 3 | 12 | 24V |
7 | Grün | 4 | 14 | 24V |
8 | Gelb | 4 | 12 | 24V |
9 | Gelb-Braun | 5 | 14 | 24V |
10 | Weiß-Gelb | 5 | 12 | 24V |
11 | pink | 6 | 14 | 24V |
12 | blau | 6 | 12 | 24V |
13 | rot | 7 | 14 | 24V |
14 | lila | 7 | 12 | 24V |
15 | braun-rot | 8 | 14 | 24V |
16 | schwarz | 8 | 12 | 24V |
17 | weiß-schwarz | |||
18 | braun-blau | |||
19 | weiß-rot | |||
20 | weiß-grau | |||
21 | weiß-blau | |||
22 | pink-braun | |||
23 | weiß-pink | |||
24 | rot-blau | 0V | ||
25 | weiß-grün | 0V |
SPS
Für die Steuerung der Station wurde eine Siemens SPS Simatic ET200SP Open Controller 1515SP PC2 verwendet. Diese wurde mittels TIA-Portal und FUP programmiert. Nähere Infos finden sich im Hauptartikel der Siemens-SPS.
Artikelname | Bestellnummer | Lieferant | Preis | Anzahl | Komponente | Beschreibung | Bild |
---|---|---|---|---|---|---|---|
Siemens SPS | 6ES7193-6AR00-0AA0 | Siemens (HSHL) | unbekannt | 1 | SPS | Siemens SPS Simatic ET200SP Open Controller 1515SP PC2: Steuert die Station | ![]() |
Siemens SPS Netzteil | 6EP7133-6AE00-0BN0 | Siemens (HSHL) | unbekannt | 1 | SPS | Siemens SPS simatic ET200SP Netzteil: Stromversorgung | ![]() |
BaseUnit | 6ES7139-68P00-0DA0 | Siemens (HSHL) | unbekannt | 1 | SPS | Siemens SPS Simatic ET200SP OBaseUnit BU15-P16+A0+2D, BU-Typ A0: Verbindung von Peripheriemodulen | ![]() |
6ES7135-6HB00-0DA1 | Siemens (HSHL) | unbekannt | 1 | SPS | Siemens SPS simatic ET200SP Analog Output Modul 2*U/I: Analoge Ausgänge | Siehe BaseUnit | |
6ES7134-6HB00-0DA1 | Siemens (HSHL) | unbekannt | 2 | SPS | Siemens SPS simatic ET200SP Analog Input Modul 2* U/I 2-/4- wire: Analoge Eingänge | Siehe BaseUnit | |
6ES7131-6BF00-0CA0 | Siemens (HSHL) | unbekannt | 2 | SPS | Siemens SPS simatic ET200SP Digital Input Modul 8* 24VDC: Digitale Eingänge | Siehe BaseUnit | |
6ES7132-6BF00-0CA0 | Siemens (HSHL) | unbekannt | 2 | SPS | Siemens SPS simatic ET200SP Digital Output Modul 8*24V DV/0,5A: Digitale Ausgänge | Siehe BaseUnit |
Metallbauteile
Die Basis der Station besteht aus einer großen Aluminium-Nutenplatte. Zur Verbindung der einzelnen Komponenten und primär zu stabilen Montage wurde Aluminiumplatten gefertigt. Diese wurden im Vorhinein mit SolidWorks geplant und anschließend wurden darüber technische Zeichnungen erstellt. In diesen befinden sich Gewinde für die direkte Verschraubung der Komponierten. Des Weiteren wurden Aluminium-Profile in der Komponente "Entnahme" verwendet: Zum einen wurden T-Profile (20mm x 20mm x 1,5mm) zur Führung des WTs und weiterer Bauteile eingesetzt, zum anderen ist zur Umsetzung eines verstellbaren und damit flexibel nutzbaren Anschlags ein Standard-BOSCH-Profil verwendet worden.
-
Magazin 1 bis 3 Zylinderplatte
-
Magazin 4 Zylinderplatte und Entnahme
Orignaldateien:
3D-Druckteile
Durch die umfangreiche Planung der Station im CAD mittels SolidWorks konnte die Möglichkeit der Fertigung durch additiver Verfahren genutzt werden. Somit konnten von vornherein die Bauteile auf diese Fertigungsart ausgelegt und optimiert werden. Durch die Fertigung mittels 3D-Druck konnten die Bauteile optimal auf die Bedürfnisse ausgelegt werden und trotzdem kostengünstig und schnell gefertigt werden. Somit wurde ein Großteil der Komponenten individuell konstruiert und in diesem Verfahren gefertigt. Im Folgenden können die Bauteile bewundert werden.
-
Nase für Entnahme
-
Stütze der Entnahme
-
Zylinderbefestigung der Entnahme
-
Magazingehäuse für Magazin 1 bis 3
-
Stütze des Magazin 1 bis 3
-
Schieber des Magazin 1 und 2
-
Schieber des Magazin 3
-
Magazingehäuse für Magazin 4
-
Stütze rechts Magazingehäuse 4
-
Stütze links Magazingehäuse 4
-
Stütze für Zylinder des Magazin 4
-
Halterung des Zylinders des Magazin 4 (Teil 1)
-
Halterung des Zylinders des Magazin 4 (Teil 2)
-
Schieber des Magazin 4
-
Klemme zur Organisation von Druckluftschläuchen
-
Adapter für Verschraubung Durchmesser 6mm Länge 10mm
-
Adapter für Verschraubung Durchmesser 6mm Länge 20mm
-
Adapter für Verschraubung Durchmesser 8mm Länge 10mm
-
Adapter für Verschraubung Durchmesser 8mm Länge 20mm
Im folgenden Ordner befeinden sich die Originaldateien: Datei:MPS1 Druckteile.zip
Verwendete Software
- SolidWorks: Erstellung des CAD-Modells und Konzipierung der Druckteile
- TIA Portal V15: Einrichtung und Programmierung der SPS
- PapDesigner: Konzipierung des Programms
- Microsoft Office: Dokumentation
Erweiterungsmöglichkeiten
Die MPS-Station 1 wurde von vornherein dahingehend konzipiert, dass diese Möglichkeiten zur Erweiterung für die kommenden Semester bietet. Diese Erweiterungen bieten sowohl Potenzial im mechanischen, elektronischen sowie auch im Softwarebereich und somit die ideale Grundlage für das Praktikum Produktionstechnik im Studiengang Mechatronik. Im Folgenden sind einige Erweiterungsmöglichkeiten enthalten.
- Füllstandsensoren für die Magazine
- Nachfüllmechanismus für die Magazine
- Kommunikation mit der Haupt SPS über BUS-Schnittstelle
- Positionserkennung an den restlichen Zylindern
- HMI zur Anlagensteuerung
- grafische Füllstandsanzeige über das HMI
- Umbau auf doppeltwirkende Zylinder an den Magazinen
- kamerabasierte Überprüfung des Warenträgers
- Erweiterung der Magazine zur Farbauswahl des Logos über das HMI
Literatur
- ↑ https://i.ebayimg.com/images/g/U~4AAOSwPSNfimkj/s-l1600.jpg
- ↑ https://www.tsisolutions.us/ecomm_images/items/large/smbr-8-20.jpg
- ↑ https://media.rs-online.com/t_large/F1215825-03.jpg
- ↑ https://www.tsisolutions.us/ecomm_images/items/large/smbr-8-20.jpg
- ↑ https://www.landefeld.com/shop/media/festo/produkte/d15000100125251.jpg
- ↑ https://www.kiowa.co.uk/SupplyImages/WF00213/P_C5DF78A94B564A5A9326D8554713803E_pp.jpg
- ↑ https://www.amazon.de/197581-grla-1-8-qs-6-rs-d-Einweg-Control-Ventil/dp/B00RW7FCSO
- ↑ https://www.festo.com/de/de/a/539682/?q=LR-1_4-DB-7~:festoSortOrderScored
- ↑ https://mall.industry.siemens.com/mall/de/WW/Catalog/Product/6EP7133-6AE00-0BN0
→ zum Hauptartikel: Mechatronisches Produktionssystem zur Produktion eines HSHL-Getränkeuntersetzers
→ zum Artikel des Praktikums: Praktikum Produktionstechnik