Legosortiermaschine Sortiereinheit Anfertigung
Teammitglieder: Tobias Brandt, Marc Eidhoff
Anfertigung der Sortiereinheit
In diesem Unterartikel werden verschiedene Punkte für die Anfertigung der Sortiereinheit näher erläutert.
Prüfen des Konzepts
Die Sortiereinheit besteht aus 3D-Durck Teilen und Acrylglasplatten. Diese sind als CAD-Modelle in SVN abgelegt und müssen vorerst überprüft werden. Bevor die Einzelteile der Sortieranlage gefertigt werden konnten musste das Gesamtkonzept und die Maßgenauigkeit geprüft werden. Dazu wurde eine Überprüfung jeder einzelnen Komponente im CAD-Modell vorgenommen es wurden die Maße, Passstellen, Verbindungsstücke und Materialstärken kontrolliert.
Ebenfalls wurde die Baugruppe zur Hilfe genommen und damit konnten mögliche Kollisionen ausgeschlossen werden. Das größte zu sortierende Legoteil passt demnach durch alle Schächte und wird an keiner Stelle eingeklemmt. Aus diesem Grund werden die CAD-Modelle ab diesem Zeitpunkt als in Ordnung angenommen und die weiteren Schritte eingeleitet.
Acrylglasplatten
Aufgrund des beschränkten Fertigungsraumes, sowohl des 3D-Druckers als auch des Lasercutters, mussten große Bauteile teils mehrfach getrennt und in sich steckbar sowie stabil, umkonstruiert werden. Alle 37 Bauteile, die aus Acrylglas gefertigt werden sollen, wurden bereits in SolidWorks so angeordnet, dass möglichst wenig Platten zur Herstellung aller Bauteile von Nöten sind. (vgl. 'Abb. 1')
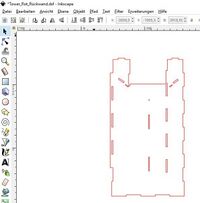
Absprache mit LaserCutter Hamm
Die Fertigung der Acrylglasplatten übernimmt das Prototyping Labor mit einem LaserCutter der Hochschule Hamm-Lippstadt am Standort Hamm. Dazu wurde ein Kontakt mit den zuständigen Betreuer hergestellt und es wurden weitere Informationen zu dem LaserCutter eingeholt. Hierbei wurde in der Stücklistefestgestellt, dass Teile zu groß waren. Nach einer genaueren Kontrolle der CAD-Modelle stellte sich jedoch heraus, dass hier die Maße der zusammengestzen Baugruppen und nicht die der einzelnen Teile eingetragen wurden. Diese Fehler wurden behoben.
Eine weitere Forderung war zudem ein spezielles Dateiformat der CAD-Modelle für den LaserCutter. Die CAD-Modelle wurden von dem ".SLDPRT"-Format in Vektorgrafiken(.dxf) umgewandelt, damit diese an die zuständigen wissenschaftlichen Mitarbeiter (Ansprechpartnerin Herr Björn Schmidt) in Hamm für den Lasercutter geschickt werden konnten.
Diese Umwandlung der SolidWorks Dateien stellte das Programm leider nicht zur Verfügung, weshalb das kostenfrei nutzbare Programm Inkscape zu Hilfe geholt werden musste.
Hierzu wurden die SolidWorks Dateien importiert, Schneidelinien rot(ff0000) und 0,01 mm stark sein, sowie die sämtliche Beschriftungen entfernt. Anschließend wurde die Datei im bereits genannten '.dxf'-Format gespeichert. Damit die Übersicht nicht verloren ging, welche Dateien schon umgewandelt wurden, musste in der Stückliste in der alle Bauteile eingetragen sind eine Spalte ergänzt werden in der abgehakt wurde welche Dateien schon vorhanden sind.
In Abbildung 2 ist eine Bearbeitung eines Teiles mit der Software InkScape zu sehen:
Die IncScape Dateien wurden in SVN abgelegt: IncSkape-Dateien.
Bestellen der Materialien
Eine Anforderung des Labors ist eine maximale Materialgröße von 300mm x 600mm. Daraufhin wurde die Stückliste, in welcher alle Teile mit ihren Maßen beschrieben sind, überprüft. Anschließend wurde die Stückliste auf Anzahl der Lasercutterteile in Hinblick auf der benötigten Stärke durchgeschaut.
Es werden 19 Platten â 3mm Stärke und 30 Platten â 5mm Platten benötigt. Mit diesen Informationen wurde eine Vielzahl von Angeboten verglichen und der günstigste Anbieter ausgewählt. Die Bill of Material wurde an Prof. Dr. Göbel weitegeiletet, sodass die Materialien bestellt wurden.
Die Bestelliste ist in SVN abgelegt: BOM Plexiglas
Nach dem Start in das Wintersemester 2018/2019 wurde festgestellt, dass die Lieferung der Teile von Hamm nach Lippstadt nicht erfolgreich war. Längeres Suchen und eine Rundmail an alle Professoren ergab schließlich, dass die Teile in Hamm fehlgeleitet wurden. Der Versand erfolgte darauf. Nachdem die Teile eingetroffen sind, wurde die Lieferung auf Vollständigkeit überprüft. In der Stückliste wurden hier die Materialstärke, Menge der Teile und die Außenmaße kontrolliert. In diesem Schritt wurde festgestellt, dass einige Acrylglasplatten falsch skaliert wurden und dementsprechend falsche Maße hatten. Außerdem wurden einige Teile überhaupt nicht geliefert.
Aus diesem Grund hat sich das Teilteam Sortierung für eine persönliche Auftragsübergabe im Prototyping Labor in Hamm entschieden, um weitere Verzögerungen ausschließen zu können. Die CAD-Modelle der falschen bzw. fehlenden Teile wurden vor Ort mit der Software Inkscape neu angepasst und skaliert. Außerdem wurden die Schnittkanten für den Laser rot eingefärbt. Darauf folgte die Fertigung der Teile wie in der Abbildung ____ zu sehen.
Nach der Fertigung wurden die Acrylglasplatten persönlich nach Lippstadt transportiert und in der Stückliste nachgetragen.
Musterfertigung
Es ist wichtig, dass der Laser genau arbeitet und die Schnittlinien eingehalten werden. Die Steckverbindungen dürfen nicht zu locker und nicht zu fest sitzen. Daher wurde ein Probeaufbau realisiert indem die beiden Platten (eine Außenwand des Towers) zusammengesteckt wurden. In Abbildung 4 ist zu erkennen, dass Teil A und Teil B die Passbedingungen erfüllen und wie ein Puzzle zusammengesetzt werden können.
Auffällig hierbei war es, dass ein geringes Spiel vorhanden ist und die deshalb Teile vorraussichtlich, wie geplant, zusätzlich verklebt werden müssen. Dafür ist eine Nacharbeit (z.B. Entgraten) nicht erforderlich. Die Außenwände wurden im Anschluss mit UV-Kleber verklebt.
3D-Druckteile
Prüfen und Übergeben
Bei dem Prüfen des Konzeptes wurden bereits die CAD-Modelle kontrolliert. Für die Sortiereinheit werden 93 zu druckende 3D-Druckteile benötigt. Diese wurden mit der Stückliste zusammen an den wissenschaftlichen Mitarbeiter Ilya Raza übergeben. Auch hier wurden Probeteile gefertigt, damit ein Testaufbau mit den Acrylglasplatten realisiert werden konnte. Dafür wurden eine Klappe und zwei seitliche Anschläge abgeholt und weiterverarbeitet. Aufgrund des 3D-Drucks sind die gedruckten Teile nachzuarbeiten. Wie in Abbildung 5 zu erkennen, muss das Stützmaterial aus den Hohlräumen sowie die Rafts entfernt werden. Desweiteren ist eine Entgratung notwendig.
Nachbearbeitung / Verklebung
Mithilfe von Feile, Cuttermesser, Dremel und Schmiergelpapier wurden alle 3D-Druckteile entgratet und vom Stützmaterial befreit. Dieser Arbeitsvorgang hat sich als durchaus schwierig herausgestellt und wie erwartet viel Zeit in Anspruch genommen. Eine besondere Herausforderung war das Entfernen des Stützmaterials aus den Steckverbindungen der Klappen und Anschlägen. Desweiteren wurden verschiedene Matarialien für das Drucken der 3D-Druckteile verwendet, sodass die Farbe bzw. Härte der Teile nicht gleich ist.
In Abbildung 6 sind zwei 3D-Druckteile zu erkennen, welche zu einer Klappe zusammengesteckt werden müssen.
Da die Steckbverbindung nicht die Notwendige Festigkeit hat, werden die 3D-Druckteile zusätzlich verklebt. Da auch eine Klebeverbindung zu flexibel war, wurden die 3D-Druckteile durch thermische Erhitzung stoffschlüssig verbunden. Die Festigkeit und Steifigkeit der Klappen ist nun akzeptabel. In den Abbildungen 7 und 8 ist der Arbeitsvorgang sowie das Endergnis einer Klappe zu erkennen. Anschließend wurde die Verbindung geschliffen.
-
Abb. 6: Steckverbindung der 3D-Druckteile
-
Abb. 7: Thermische Verbindung der 3D-Druckteile
-
Abb. 8: Fertige Klappe
Servomotoren
Die Servomotoren sind für die Bewegung der Klappen vorgesehen. Im der gesamten Sortiereinheit werden 11 Servomotoren verwendet. Angesteuert werden diese über die PWM-Anschlüsse des Arduinos und einer Steuerleitung. Die Servos müssen nach einem vorher definierten Winkel verstellt werden können. Als Endergebnis soll die automatische Sortierung der Legoteile in die Sortierkisten über die Klappen erfolgen. Aufgrund von Zeitmangel aus dem letzten Semester konnten die Motoren allerdings nicht richtig angesteuert werden. Dieses zeigte sich durch "zucken" oder Stillstand einiger Motoren.
Ausgangszustand:
- 10 Meter Signalkabel
- "Lötkugel" für die Spannungsversorgung
- Lötverbindungen an den Steckern können sich leicht berühren (Kurzschlussgefahr)
Aufbau einer Testplatine
Um Störeinflüsse der Leitungen zu den Servomotoren zu untersuchen wurde eine Platine, wie in Abbildung 6 zu sehen, mit passenden Steckern angefertigt und direkt über ca. 30cm lange Leitungen an den Arduino angeschlossen. Durch die Platine können sich die einzelnen Steckerkontakte nicht mehr berühren. Die Steckverbindungen zu den Servos können so erleichtert verwendet werden ohne Kurzschlüsse zu verursachen. Seitlich von den Steckkontakten sind auf der Platine die Signalleitungen herausgeführt, die an die Steuerelektronik verbunden werden können.
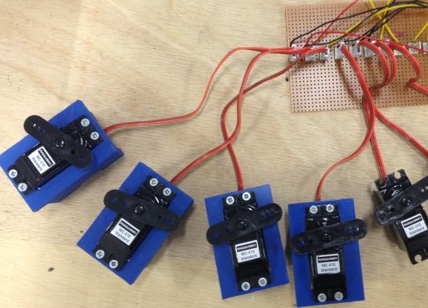
Um das 10m Signalkabel als Fehlerquelle auszuschließen wurde die Testplatine direkt an den Arduino im Schaltschrank angeschlossen. Nach dem Erstellen und anschließen der Platine an den Arduino wurde das PWM-Signal am Ausgangspin direkt gemessen und mit dem Signal an der Platine verglichen. Da das Signal an beiden Messstellen identisch war und einen ausgeprägten Rechteckimpuls darstellte ist der Grund für die Störungen und des nicht Funktionierens in der Programmierung zu suchen.
Ansteuerung der Servos
Eine Recherche hat ergeben, dass der Befehl Servo.write eine falsche Pulsweite ausgibt. Diese Pulsweite kann über die Bibliothek Servo.h verändert werden. Die Winkelstellung der Servos erfolgt anschließend über eine Pulslänge.
Einige Servos (z.B. wie das verwendete Modell „MC-410“) benötigen zur Ansteuerung eine andere Pulslänge als die Standardeinstellung in Arduino. Im folgendem Beispielprogramm in Abbildung 7 ist der Test eines Servos mit angepasster Pulsweitenbreite implementiert worden. Dieses Programm dient zum Test eines einzigen Servomotoren und ist unter folgendem Link zu finden: Servotest
//Einbinden der Bibliothek zum Ansteuern von Servomotoren
#include <Servo.h>
//Implementieren eines Servos
Servo Servo5;
void setup() {
//(Pin-Mode, Pulsweitenänderung)
Servo5.attach(5, 800, 2100);
}
void loop() {
//Wechsel der Stellung von 70° auf 0°
Servo5.write(70);
delay(1000);
Servo5.write(0);
delay(1000);
}
Abbildung 7
Die Erklärung wie die Pulsweite angepasst werden kann ist unter folgendem Link zu finden: Pulsweitenanpassung
Unter Verwendung der Pulsweitenänderung wurde das PWM- Signal mit Hilfe eines Oszilloskops wie in Abbildung 8 zu erkennen überprüft. Hier ist zu erkennen, dass beide Kanäle (in diesem Fall Servomotor 1 und 2) über einen eindeutigen Rechteckimpuls angesteuert werden. Somit ist die Ansteuerung fehlerfrei und funktionsfähig.
Der Kanal 1 und 2 sind mit 2V/Division eingestellt. Die Zeiteinteilung (Y-Achse) ist mit 5ms/Div dargestellt.
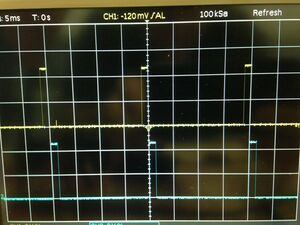
Hiernach musste der Rückbau stattfinden, sodass die Servosmotoren nicht mehr direkt im Schaltschrank angeschlossen sind, sondern an der Position der späteren Sortiereinheit Verwendung finden können.
Dafür wurde das 10m lange Signal und das 10m lange Spannungsversorgungskabel auf ca.3m gekürzt.
Da die Platine nur zu Testzwecken diente und ein beliebiges Vertauschen der Motoren möglich ist wurde am Ende des Signalkabels ein Sub-D Stecker anglötet. Hierdurch wird eine fester Anschluss der Motoren gewährleistet. In Abbildung 9 ist der Stecker zu sehen. Auf der rechten Seite ist das Signal- und Spannungsversorgungskabel zu erkennen. Auf der linken Seite führen die Steuerleitung zu den Servos (hier noch auf die Testplatine), da die Leitungslängen zu den Servos noch nicht feststehen.
Die Pinbelegung ist unter folgender Adresse hinterlegt: Pinbelegung
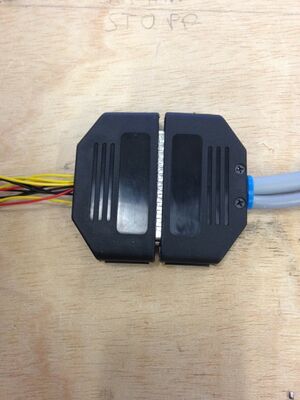
Abschließend wurde ein Funktionstest der einzelnen Motoren durchgeführt. Dabei stellte sich heraus, dass 4 von den 11 Motoren nicht funktionstüchtig waren und somit nachbestellt werden mussten.
Das Vorgehen der Prüfung und der Fehlerbehebung wurde in einem Komponententest festgehalten und ist unter folgendem Link zu finden: Komponententest
Mit der Verbindung der seriellen Schnittstelle des Arduinos und der Servos über die erstellte Steckverbidnung und der Testplatine wurden alle Servomotoren noch einmal gleichzeitig getestet. Dass Programm hierzu ist unter diesem Linkzu finden.
Desweiteren wurde nach der Schaltschrankneuverdrahtung ein gesamte Kontrolle der Steuerleitungen und der Spannungsversorgung durchgeführt. Hierfür wurde die Pinbelegung kontrolliert und erfolgreich durchgemessen. Die Einstellungen der richtigen Drehwinkel wird im Aufbau der gesamten Anlage weiter ausgeführt.
Gesamtaufbau der Sortiereinheit
In der Montageliste werden alle zu bearbeitenden Punkte aufgeführt.
Testaufbau
Nachdem nun Probeteile der Acrylglasplatten und 3D-Teile gerfertigt und nachbearbeitet wurden, wird ein Testaufbau eines Teiles der Sortiereinheit realisiert. Eine Klappe besteht dabei aus zwei zusammengesetzten 3D-Druckteilen. Die Steckverbinding dieser Teile erwies sich als schwierig. Eine sehr genaue und zeitintensive Nacharbeit der 3D-Druckteile ist deshalb erforderlich.
Der gesamte Testaufbau besteht aus einer Verbindung einer Klappe mit zwei Anschlägen (3D-Druckteile) mit einer zusammengesteckten Außenwand (Acrylglas). In Abbildung 5 ist dieser Testaufbau zu sehen.
Ergebnisse aus dem Testaufbau sind:
- sehr genaue Nachbearbeitung der 3D-Druckteile erforderlich
- kleben der segmentierten 3D-Druckteile und Acrylglasplatten notwendig
- keine Nachbearbeitung der Acrylglasplatten nötig
- Steckverbindungen sind passgenau
Nun wird zusätzlich eine Welle gebogen und darauf ein Ruderhorn befestigt. In Abbildung __________ wird dieser Arbeitsvorgang gezeigt. In den Abbildungen ___ und ___ wird die Klappe in den Mitteltower der Sortiereinheit eingebaut. Zusätzlich wird die Welle mit dem Ruderhorn in die zugehörigen Bohrungen geschoben und das Ruderhorn mit Federn mit dem Servo verbunden.
-
Abb. : Ruderhorn an der Welle
-
Abb. : Welle und Servo im Testaufbau
-
Abb. : Anschlag und Klappen im Testaufbau
In den folgenden Schritten wird der Drehwinkel eines Servos eingestellt:
- Servo auf „Nullstellung“ drehen (Arduino Programm Wert 0)
- Schwarzer Hebelarm auf max. Stellung anbringen
- Ruderhorn parallel anordnen
- Federn befestigen
- Servo auf max. Stellung ansteuern
- Ruderhorn ausklinken
- In Initialstellung Klappe befestigen/kleben
Wenn der Kleber getrocknet ist können die Drehwinkel in dem Arduino Programm eingestellt werden. Mithilfe der Testplatine und dem Testprogramm für einen Servo können die Winkel durch ausprobieren ermittelt werden.
Dabei muss zuerst der Servo in die Ausgangssituation (Winkel = 0) gebracht werden. Durch langsames erhöhen des Winkels in dem Testprogramm dreht sich die Klappe immer weiter Richtung Anschlag.
Ist der Anschlag erreicht, wurde der richtige Drehwinkel gefunden. Die aktuellen Drehwinkel befinden sich in diesem Dokument: Drehwinkel (Stand: Januar 2019).
Bei der Kalibrierung der Drehwinkel wurde allerdings folgendes Problem festgestellt:
- Die Ruderhörner stören die Bewegungsfreiheit der Federn und diese können sich folglich nicht richtig ausdehnen.
Zur Lösung des Problems könn mit Hilfe eines Dremels die Ruderhörner verkleinert werden bis die Feder eine freie Bewegung bis zum Schließen der Klappe hat. In Abbildung ___ ist eine Verkleinerung des Ruderhorns gut zu erkennen.
In dem folgendem GIF (Abbildung ___) ist die Funktion einer fertigen Klappe im Testaufbau zu sehen.
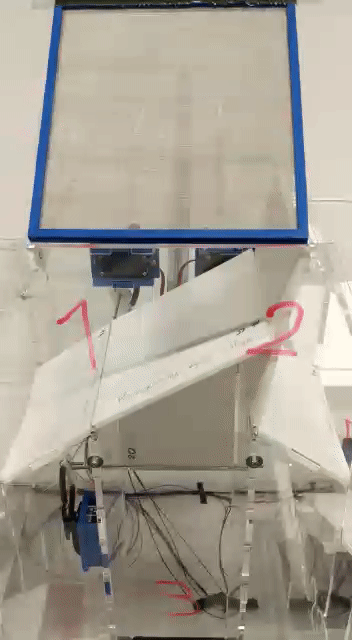
Grundgerüst
Das Grundgerüst aus Acrylglasplatten dient Grundlage für den Kompletten Aufbau. Diese werden durch Steckverbindungen zu drei Modulen zusammen gesteckt: Tower weiß, Tower rot, Vorsortierung. Als Fundament dienen zwei zusammengeklebte 5mm Platten, auf denen die Seite- vorder und Rückwände aufgesteckt werden. Alle nicht geklebten Teile werden nicht wie geplant auch geklebt sondern durch Schraubverbindungen besfestigt. Hierfür werden Bohrungen (2,5mm) in die Seitenwände gebohrt und M3 Gewinde geschnitten. Durch dieses Verfahren können die Platten einfach gelöst und abgebaut werden, so dass evtl. defekte 3D- Druckteile später ausgewechselt werden können. In den Abbilungen ___ und ___ ist das schneiden eines Gewindes und eine Schraube zu erkennen.
-
Abb. : Gewindeschneiden in die Acrylglasplatten
-
Abb. : Verschrauben der Platten
Nach der fertigen Montage des Grundgerüsts wurde festgestellt, dass sich Teilerückführung der Sortiereinheit aufgrund des langen Hebelarms nach unten neigt. Zur Behebung des Problems wurde eine Stütze aus Boschprofil auf die richtige Länge gesägt und mittels Schraubverbindungen befestigt. Sie verbindet den Mitteltower mit der Teilerückführung. In der Abbildung ___ ist die eingebaute Stütze zu erkennen.
Einbau der Klappen
Nachdem das Grundgerüst aufbgebaut war konnten die ersten 3D-Druckteile eingebaut werden. Wichtig ist es hierbei beachten, dass sich in dem Tower rot und weiß Zwischenwände aus 3mm Acrylglas befinden. Diese Platten müssen zuerst wie in Abb. ____ und _____ in eine Seitenwand eingesteckt werden. Bei den Anschlägen die zusammen geschmolzen wurden machte sich jetzt die sorgfältige Nacharbeit der Klebestellen bemerkbar. Eine besondere Herausforderung stellte sich bei dem Einsetzen der Vorderwand bemerkbar, da in diese Vorderwand knapp 20 Teile passgenau eingesteckt werden mussten.
-
Abb. : Einsetzen von 3D-Druckteilen im CAD-Modell
-
Abb. : Einsetzen der 3D-Druckteile in der Sortiereinheit
Der nächste Schritt ist das einbauen aller weiteren Klappen, Wellen und Servos. Die Arbeitsschritte sind identisch mit der Klappe aus dem Testaufbau.
Elektrischer Anschluss
Der elektrische Anschluss der Servomotoren ist wie folgt umgesetzt worden:
- An dem Servomotor befindet sich jeweils an einem 10cm langen Kabel eine 3-polige Buchse
- Als Gegenstück wurde ein 3-poliger Stecker verwendet an dem 3 Einzeladern angelötet wurden
- Alle Einzeladern von jedem Servo wurden als Kabelbaum zusammen gefass und auf Verbindungsstecker zum Schaltschrank geführt
- Jede Leitung wurde auf dem Sub-D Stecker nach vorher erstellten Belegungsplan aufgelötet
- Die Lötverbindungen wurden gegen direktes Berühren mit Schrumpfschläuchen gesichert
In den folgenden drei Abbildungen ist die Umsetzung sichtbar:
-
Abb. : Steckverbindung des Servos
-
Abb. : Steckverbindung_Sortiereinheit_Schaltschrank
Prüfprotokolle
Funktionsprüfprotokoll
In dem Funktionsprüfprotokoll werden folgende Punkte bearbeitet:
- Überprüfung ob die Fächer richtig angesteuert werden. Teilkontrolle in den Kästen
- Überprüfung ob alle nicht erkannten Teile in ein seperates fach liegen
- Fremdteilsortierung kontrollieren
Das Protokoll ist unter folgendem Link abrufbar: Funktionsprüfprotokoll
Unit-Tests
Für veränderte oder neu erstellte Software werden Unit-Tests durchgeführt, um die Funktion der neuen Komponenten zu überprüfen. Dazu wurde ein Prüfleitfaden erstellt, in welchem die Schritte zum Test der entsprechenden Funktion aufgeführt sind. Dem Verantwortlichen Prüfer wird dieser Leitfaden übergeben und der Test wird durchgeführt. Mängel oder Warnungen müssen dokumentiert und weitergegeben werden.
Die Vorlage für einen Unit-Test ist unter dem folgenden Link zu finden: Vorlage Unit Test
Eine beispielhafte Ausfüllung für die Unit "Klappensteuerung" bedindet sich hier: Unit Test für alle Klappen
Integrationstest
In Form eines Integrationstests wird ein einzelnes Modul (eine Unit) in dem Gesamtsystem getestet.
Die Vorlage für einen Integrations-Test ist unter dem folgenden Link zu finden: Vorlage Integrations-Test
Eine beispielhafte Ausfüllung für den Integrationstest der"Klappensteuerung" bedindet sich hier: Integrations-Test für alle Klappen
Dies ist ein Unterartikel von der Legosortiermaschine Sortierung, welcher den genauen Aufbau der Sortiereinheit beschreibt.