Ansteuerung des Mitsubishi Roboters
Fachpraktikum Produktionstechnik (Wintersemester 2016/2017)
Projektteam: Tobias Päschel, Khaled AL-Hushibiri
Studiengang: Mechatronik (7. Fachsemester)
Schwerpunkt: Global Production Engineering
Leitung: Prof. Dr. Mirek Göbel
Von der Produktentwicklung bis zum Recycling, lokale Nischen und globale Märkte: Der Schwerpunkt Global Production Engineering bietet im Rahmen des Studiengangs Mechatronik ein umfangreiches Repertoire für die Planung und Umsetzung von Produktionsprozessen. Unter Prodktionstechnik versteht man die Transformation wissenschaftlicher Erkenntnisse in Verfahren und Prozesse, die einerseits vom Menschen (technologisch) beherrscht werden und sich andererseits in wirtschaftlich nutzbare Produktionssysteme integrieren lassen. Sie strebt nach Effizienz und wirtschaftlichem Erfolg und genau hier setzt dieses Fachpraktikum für Produktionstechnik an, um eine Verknüpfung zwischen Theorie und Praxis herzustellen. Neben der Ansteuerung eines Industrieroboters gehören die Planung und virutelle Inbetriebnahme einer automatisierten Anlage mit Werkzeugen der Digitalen Fabrik, der Umgang mit der SPS-Programmierung an der Schulungsanlage des Labors, Übungen zur CAD-CAM-CNC-Kette sowie die Fertigung von Teilen an Werkzeugmaschinen zu den vielfältigen Themenfeldern.
Zurück zur Projektseite 3-D-Bearbeitungsmaschine (Projekt des Schwerpunkts GPE im Studiengang MTR)
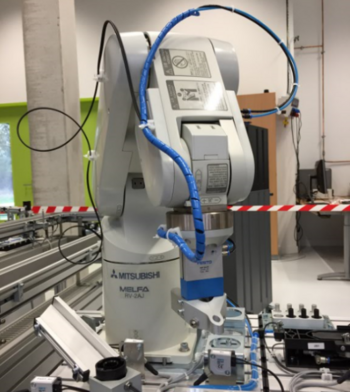
Einführung in das Projekt
Automatisierte Roboter sind aus dem 21. Jahrhundert nicht mehr wegzudenken. Die Nachfrage nach automatisierten Systemen ist bereits gewaltig und wächst zunehmend. Historisch einmalig ist an der heutigen Lage aber nicht nur, dass die Automatisierung schneller wächst als die Märkte, sondern auch, dass die Maschinen weit mehr Jobs ersetzen, als zu ihrer Herstellung notwendig sind. Nahezu jedes größere Wirtschaftsunternehmen verlässt sich auf automatisierte Systeme, wie das Lernsystem Automatisierung und Technik von Festo Didactic GmbH & Co. KG. In Abbildung 1 [1] ist der Hauptbestandteil dieser Lernstation dargestellt.
Unter der Automatisierung versteht man die Systemübertragung von Funktionen des Produktionsprozesses, insbesondere Prozesssteuerungs- und -regelungsaufgaben, vom Menschen auf künstliche Systeme.
Die Automatisierungsziele in technischen Anlagen werden vor allem durch folgende Punkte geprägt:
- Die Automatisierung wird eingesetzt, weil die Überwachung und Steuerung der Prozesse für den Menschen zu schwierig ist.
- Durch die Automatisierung lassen sich bessere wirtschaftliche Ergebnisse als durch manuelle Steuerung erzielen.
- Mittels Automatisierungsanlagen können die Unzulänglichkeiten des Menschen, wie z.B. Fehlhandlungen oder Überbeanspruchung vermindert werden.
- Die Automatisierung ermöglicht eine Verbesserung der Arbeits- sowie Lebensbedingungen, indem sie von monotoner, anstrengender oder gefährlicher Arbeit befreit wird.
Ausgangssituation, Anforderungen sowie Projektziele
Ausgangssituation: Die Station Lernsystem Automatisierung und Technik ist zwar betriebsbereit, allerdings ist der MELFA Industrieroboter RV-2AJ nicht funktionsfähig und somit das gesamte MPS-System nicht einsatzfähig.
Anforderungen an das Projekt:
- Informationsbeschaffung (Einlesen in vorliegende Unterlagen; Recherche im Internet, Informationsaustausch mit Herstellern; Ersetzen von vorhandenen schriftlichen Dokumenten)
- Systemübersicht (Komponenten des Lernsystems darstellen)
- Ansteuerung (Recherche; Umsetzung)
- Inbetriebnahme des Roboterarms (Recherche; Vorbereitung; Anlernen der Arbeitsschritte; Test; Wartung und nützliche Hinweise)
- Herausforderung: Inbetriebnahme des gesamten MPS-Systems (Einbinden des Roboterarms in das MPS-System; Auswertung)
Projektziele:
Aus den dargestellten Anforderungen lassen sich folgende Projektziele ableiten:
- Förderung der Prozessstabilisierung
- Einhaltung der Prozessführung
- Möglichst optimale Arbeitspunkte herstellen
- Systemaufbau sowie Programmierung optimieren
- Gefährliche Extremsituation verhindern
- Nachhaltige Dokumentation (Wikipedia der Hochschule, SVN)
Projektplanung
Die Abbildung 2 [2] beschreibt das Konzept der Projektplanung. Diese wurde weitestgehend eingehalten.
Abb. 2 Konzept der Projektplanung Projektplanung
Systemübersicht
Der Aufbau der Station Roboter besteht aus:
- Roboter RV-2AJ mit Steuergerät,
- Modul Rutsche,
- Modul Aufnahme,
- Modul Montageaufnahme,
- Modul Magazin,
- Profilplatte und
- Wagen.
Betriebsdruck: 600 kPa (6 bar)
Spannungsversorgung: 24 V DC, 4,5 A
Alle Komponenten, Verschlauchungen und Verkabelungen sind eindeutig gekennzeichnet, so dass ein Wiederherstellen aller Verbindungen problemlos möglich ist.
Funktion und Referenzdaten
Die Aufgabe der Station Roboter ist es:
- Die Materialbeschaffenheit eines Werkstückes festzustellen,
- Werkstücke aus einer Aufnahme zu entnehmen,
- Die Werkstücke an eine Montageposition zu transportieren und orientiert abzulegen,
- Werkstücke zu einem Magazin zu transportieren und sie dort abzulegen oder
- Die Werkstücke an eine Folgestation weiter zugeben.
Zum Transport der Werkstücke wird ein Vertikal-Knickarmroboter eingesetzt. Es handelt sich hierbei um einen industriellen Roboter mit 5 Achsen. Die Wiederholgenauigkeit der Roboterpositionierung beträgt ± 0,02 mm. Die maximale Geschwindigkeit beträgt 2200 mm/s. Eine Endstellungs- und Überlastüberwachung ist integriert. Die maximale Reichweite des Roboterarms beträgt 410 mm.
Das Modul Rutsche dient zum Transportieren oder Lagern der Werkstücke. Durch die variable Einstellung von Neigung und Höhe ist dieses Modul universell einsetzbar. In der Station Roboter wird das Modul Rutsche zur Zuführung des Werkstückes zum Modul Aufnahme verwendet. Das Werkstück immer über die Rutsche der Aufnahme zuführen. Es darf nicht von Hand in die Aufnahme gelegt werden!
In das Modul Aufnahme werden bei der Station Roboter Werkstücke über die Rutsche eingelegt. Die Werkstücke werden in der Aufnahme von einem optischen Reflex-Lichttaster erkannt.
Der Greifer ist am Roboterarm montiert. Als Antrieb für den Greifer wird ein pneumatischer Parallelgreifer eingesetzt. Die Greiferbacken sind so konstruiert, dass der Greifer drei Greifpositionen besitzt. Außengreifer und Mittelgreifer werden zum Transport der Werkstücke Grundkörper und Deckel eingesetzt. Mit dem Kolben-/Federgreifer werden die Kolben oder die Feder gegriffen. Ein optischer Reflex-Lichttaster (Lichtleiter) in einem der Greiferbacken wird zur Farberkennung der Werkstücke eingesetzt.
Im Modul Montageaufnahme werden die Werkstücke montiert. Ein Bolzen in der Werkstückaufnahmeposition „Montage“ sorgt für eine gegen Verdrehung gesicherte Positionierung des Werkstückes. In der Position „Umgreifen“ wird der Grundkörper abgesetzt, damit der Roboter zur Ermittlung der Orientierung umgreifen kann. Der Referenzpunkt wird beim Teachen des Roboters angefahren. Alle weiteren Positionen werden vom Referenzpunkt aus im Roboterprogramm berechnet. Mit einem Reflex-Lichttaster wird die Orientierung der Werkstücke Grundkörper und Deckel geprüft.
Das Modul Magazin dient zur Lagerung runder Werkstücke. Ein Schieber verhindert beim Entnehmen des Rohres aus dem Halter, dass die Werkstücke herausfallen. Im Fallrohr des Moduls Magazin können bis zu 8 Werkstücke gespeichert werden.
Ablaufbeschreibung
Startvoraussetzung:
- Ein Werkstück in der Aufnahme
Ausgangsstellung:
- Roboterarm in Grundstellung
- Greifer geöffnet
Ablaufbeschreibung:
Die Werkstücke werden durch eine Rutsche zur Aufnahme transportiert. Der Roboter nimmt die Werkstücke dort mit einem pneumatischen Greifer auf. Anschließend werden die Werkstücke in die Montageaufnahme transportiert. Mit einem optischen Sensor wird die Orientierung der Werkstücke kontrolliert. Ein weiterer optischer Sensor ist im Greifer montiert. Dieser Sensor unterscheidet „schwarze“ und „nicht schwarze“ Werkstücke. In Abhängigkeit von der Farbe werden die Werkstücke in verschiedenen Magazinen abgelegt. Außerdem können die Werkstücke auch zu einer Folgestation transportiert werden. In Kombination mit der 'Station Montieren' können die Werkstücke zu einfach wirkenden Zylindern montiert werden.
Zur Verdeutlichung des Ablaufes soll folgendes Video dienen: https://www.youtube.com/watch?v=Fbh9EC1CC0U (Internetquelle: YouTube)
Ablauf starten:
1. Spannungsversorgung und Druckluftversorgung überprüfen.
2. Werkstücke an Übergabestellen von Modulen oder Stationen vor dem Richten von Hand entnehmen.
3. Der Roboter steht in der Grundposition.
4. Ein Werkstück über die Rutsche in das Modul Aufnahme gleiten lassen.
5. Ablauf der Station Roboter starten: MODE Schalter am Steuergerät in die Position AUTO (Op) stellen. Mit dem Taster CHANG.DISP die Programm-Menüanzeige wählen. Mit den Tasten UP und DOWN die Programmnummer selektieren. Servospannungsversorgung durch Drücken des Tasters SVO ON einschalten. Taster START am Steuergerät drücken.
(HINWEIS: Der Ablauf kann durch Drücken des NOT-AUS Tasters oder durch Drücken des STOP Tasters jederzeit unterbrochen werden).
(HINWEIS: Bei einer Kombination mehrerer Stationen gilt: Richten der einzelnen Stationen erfolgt entgegen dem Materialfluss).
Inbetriebnahme des Roboterarms
Die Sichtprüfung muss vor jeder Inbetriebnahme durchgeführt werden!
Folgende Punkte müssen vor dem Start der Station überprüft werden:
- Die elektrischen Anschlüsse
- Den korrekten Sitz und den Zustand der Druckluftanschlüsse
- Die mechanischen Komponenten auf sichtbare Defekte (Risse, lose Verbindungen usw.)
- Die NOT-AUS Einrichtungen auf Funktion
Gegebenenfalls vor dem Start der Station entdeckte Schäden/Fehler beseitigen!
Einstellen der Grundposition (Nullpunkt)
Die Einstellung erfolgt über die Datenübergabe. Diese Methode wird nach Auslieferung des Roboters zur Einstellung der Grundposition verwendet. Die Daten der vom Hersteller vorgegebenen Grundposition befinden sich auf einem Aufkleber an der Innenseite der Batteriefachabdeckung und auf dem Beipackzettel im Karton des Roboterarms.
Die Versorgungsspannung des Steuergerätes muss erst abgeschaltet werden, bevor die Abdeckung des Batteriefaches entfernt werden kann. Außerdem befinden sich die Daten für die Grundeinstellung des Nullpunktes in der Spalte "Default" des Aufklebers. Sollte eine Neueinstellung der Grundposition des Roboterarms mit einer anderen Methode vorgenommen werden (z. B. beim Auswechseln eines Motors), gelten die zuletzt eingetragenen Daten.
Abbildung 3 [3] zeigt den Aufkleber mit den Daten der Grundposition (Beispieldaten).
Schritt 1: Auswahl der Einstellmethode
Abbildung 4 [4] beschreibt die Auswahl der Methode „Einstellung über Dateneingabe“ mit Hilfe der Teaching Box.
Schritt 2: Eingabe der Grundpositionsdaten
Nachdem die Versorgungsspannung der Servoantriebe abgeschaltet ist, wird das Menü zur Eingabe der Grundpositionsdaten (s. Abb 5 [5]) auf der Teaching Box angezeigt.
Abb. 5 Zuordnung der Daten auf dem Display
Der Cursor auf dem Display der Teaching Box kann über die Tasten [ADD Pfeil hoch], [RPL Pfeil runter], [DEL Pfeil links] und [HAND Pfeil rechts] bewegt werden. Die Eingabe von Zeichen erfolgt bei gleichzeitiger Betätigung der [POS/CHAR]-Taste und der Taste für das Zeichen. Bei mehrmaliger Betätigung der Zeichentaste wird jeweils das nächste Zeichen aufgerufen. Die Eingabe von Ziffern erfolgt über die Zifferntasten. Fehlerhafte Eingaben können mit der [DEL Pfeil links] Taste gelöschen werden. Bei fehlerhaft eingegebenen Grundpositionsdaten wird der Alarm Nr. 1760 angezeigt. [ERROR RESET] Taste betätigen und Daten für die Grundposition erneut eingeben.
Dieser Vorgang wird in Abbildung 6 [6] und fortlaufend in Abbildung 7 [7] beschrieben.
Ansteuerung per Teaching Box
Schritt 1: Versorgungsspannung einschalten
1. Vergewissern, dass sich niemand im Bewegungsbereich des Roboterarms aufhält.
2. Den [POWER]-Schalter an der Seite des Steuergerätes in die Position „ON“ bringen.
3. Die Kontroll-LEDs des Steuergerätes blinken einen Moment. Auf der STATUS NUMBER-Anzeige erscheint die Anzeige „o.100“.
Schritt 2: Teaching Box einschalten
1. Den [MODE]-Schalter in die „TEACH“-Position stellen (s. Abb. 8 [8]).
2. Den [ENABLE/DISABLE]-Schalter in die Position „ENABLE“ drehen (s. Abb. 9 [9]).
3. Auf dem Display der Teaching Box erscheint das Hauptmenü (s. Abb. 9 [9]).
Positionen teachen
Zum Teachen der Positionen wie folgt vorgehen:
1. Nach dem Einschalten des Steuergerätes das Startdisplay durch Drücken der Taste MENU aufrufen. 'TEACH' durch Drücken der Taste INP/EXE wählen.
2. Programmnummer des aktuellen Programms eingeben. Danach INP/EXE Taste drücken.
3. POS Taste drücken. Mit den Tasten +/ FORWD bzw. -/ BACKWD Positionen P1, P2, P3, P4, P5 und P99 auswählen.
4. Verfahrgeschwindigkeit durch Drücken der Taste -/ BACKWD reduzieren.
5. Totmannschalter auf der Rückseite der Teachingbox sowie STEP/MOVE Taste drücken. Wenn die Servomotoren eingeschaltet sind, INP/EXE Taste drücken. Die gewählte Position wird angefahren. Dabei auf mögliche Kollisionen achten!
6. Angefahrene Positionen kontrollieren. Ist die Position korrekt, zu Schritt 3 zurückkehren und nächste Position prüfen. Ist die Position nicht korrekt, weiter mit Schritt 7 verfahren.
7. Totmannschalter drücken.
8. Koordinatensystem wählen, z.B. XYZ.
9. STEP/MOVE Taste drücken und Roboter durch Drücken der Tasten -X, +X, -Y, +Y, -Z, +Z, -A, +A, -B und +B bewegen.
10. Wenn die genaue Position angefahren ist, ADD Taste zweimal drücken. Die aktuelle Position wird in die Positionsliste übernommen.
(HINWEIS: Durch das Drücken der Tasten HAND und +C bzw. HAND und -C wird der Greifer geöffnet bzw. geschlossen).
Ansteuerung per CIROS Robotics
Folgende Schritte müssen ausgeführt werden, um ein Programm auf das Steuergerät zu laden:
1. PC und Steuergerät mit dem Programmierkabel verbinden.
2. Steuergerät einschalten.
3. Netzgerät einschalten.
4. Druckluftversorgung einschalten.
5. NOT-AUS Taster entriegeln.
6. Roboter Programmiersoftware (CIROS Robotics) starten.
7. Das gewünschte Programm aus dem Verzeichnis auswählen.
8. MODE Schalter am Steuergerät in die Position AUT (ext) stellen.
9. Programm kompilieren.
10. Programm und Positionsliste in das Steuergerät laden.
Als Programmiersprache können entweder MELFA-BASIC IV oder MOVEMASTER COMMAND verwendet werden. Um die Funktionalität des Steuergerätes in vollem Umfang zu nutzen, sollten die MELFA-BASIC-IV-Befehle verwendet werden. Eine fortlaufende Übersicht über alle Programmierbefehle und Parameter sind in Form von Links im Anhang zu finden.
Sicherheitshinweise und Wartung
Grundvoraussetzung für den sicherheitsgerechten Umgang und den störungsfreien Betrieb des MPS-Systems ist die Kenntnis der grundlegenden Sicherheitshinweise und der Sicherheitsvorschriften.
Allgemein:
- Nur unter Aufsicht eines Betreuers/einer Betreuerin an der Station arbeiten.
- Datenblätter der einzelnen Elemente beachten.
Elektrik:
- Herstellen bzw. abbauen von elektrischen Verbindungen nur in spannungslosem Zustand.
- Nur Kleinspannungen verwenden (max. 24 V DC).
Pneumatik:
- Den zulässigen Druck von 800 kPa (8 bar) nicht überschreiten.
- Die Druckluft erst einschalten, wenn alle Schlauchverbindungen hergestellt und gesichert sind.
- Keine Schläuche unter Druck entkuppeln.
- Beim Einschalten der Druckluft besonders vorsichtig sein. Zylinder können selbsttätig aus- oder einfahren.
Robotik:
- Kein bewegliches Teil des Roboters während des Betriebes berühren. Roboter vor jeder Arbeit in Reichweite des Roboters ausschalten.
- Eine nicht angeschlossene Teaching-Box wegen der Nichtwirksamkeit der integrierten NOT-AUS Einrichtung nicht in der Nähe des Roboters aufbewahren.
- Die elektrisch gesteuerte Hand des Roboters verliert bei Netzabschaltung, d.h. auch in einer NOT-AUS Situation, ihre Haltekraft.
Mechanik:
- Alle Elemente fest auf die Platte montieren.
- Nur bei Stillstand in die Station greifen.
Tägliche Inspektionspunkte
Die Abbildung 10 [10] beschreibt die täglichen Inspektionspunkte, die sorgfältig durchgeführt werden müssen, um eine einwandfreie Funktion des Roboters zu gewährleisten.
Abb. 10 Tägliche Inspektionspunkte
Periodische Inspektionspunkte
Die Abbildung 11 [11] beschreibt die periodischen Inspektionspunkte, die sorgfältig durchgeführt werden müssen, um eine einwandfreie Funktion des Roboters zu gewährleisten.
Abb. 11 Periodische Inspektionspunkte
Austausch der Pufferbatterien
Der Roboterarm verfügt über Pufferbatterien, um die Encoder-Positionsdaten auch im ausgeschalteten Zustand zu speichern. Ebenso befindet sich im Steuergerät eine Pufferbatterie, die zur Speicherung der Programme und Positionen dient. Ist die Lebensdauer der Batterien abgelaufen, wird eine Fehlermeldung mit der Fehlernummer 7520 ausgelöst. Die Batterien sind dann schnellstmöglich zu ersetzen, um einen Verlust der Daten zu verhindern. Die Batterien sind auf Lithiumbasis hergestellt. Der folgende Abschnitt beschreibt das Austauschen der Pufferbatterien.
(HINWEIS: Sowohl die Batterien im Roboterarm als auch die im Steuergerät immer gleichzeitig austauschen!)
(HINWEIS: Der gesamte Austauschvorgang darf maximal 15 Minuten dauern. Andernfalls kann es zu einem Datenverlust kommen!)
Austausch der Batterien im Roboterarm
1. Überprüfung der Kabelverbindung zwischen Roboterarm und Steuergerät.
2. Steuergerät einschalten.. Das Steuergerät liefert während des Batteriewechsels die Versorgungsspannung für die Encoder. Der Roboterarm muss mit dem eingeschalteten Steuergerät verbunden sein, damit die Positionsdaten nicht verloren gehen.
3. Mit dem Jog-Betrieb die angegebenen Achsen wie folgt verfahren: J2 = −20°, J3 = 90° und J5 = 90°.
4. Zur Sicherheit den NOT-HALT-Schalter betätigen.
5. Schulterabdeckung A entfernen.
6. Batteriefachabdeckung 2 entfernen (s. Abb. 12 [12]).
7. Schrauben 3 und die Batteriehalterung 4 entfernen (s. Abb. 12 [12]).
8. Alle alten Batterien aus dem Batteriehalter entnehmen und die Steckanschlüsse trennen.
9. Neue Batterien einsetzen. Anschließend Anschlussstecker wieder aufstecken.
10. Batteriehalterung montieren.
11. Abdeckung des Batteriefachs montieren.
12. Sachgerechte Entsorgung der Batterien.
Abb. 12 Austausch der Pufferbatterien im Roboterarm
Austausch der Batterie im Steuergerät
1. Steuergerät für ca. 1 Minute einschalten.
2. Netzschalter ausschalten und Netzzuleitung trennen.
3. Mindestens 3 Minuten warten, damit sich die Restspannungen abbauen können.
4. Befestigungsschraube des Gehäusedeckels lösen und Abdeckung entfernen (s. Abb 13 [13]).
5. Steckverbindung lösen und Batterie entnehmen.
6. Neue Batterie einsetzen.
7. Den Stecker der Batterie mit dem entsprechenden Anschluss verbinden. Kontaktseite dabei nach unten halten.
8. Alle Abdeckungen mit den Befestigungsschrauben montieren.
9. Batterie-Timer zurück (siehe Zurücksetzen des Batterie-Timers).
10. Sachgerechte Entsorung der Batterie.
Abb. 13 Entfernen des Gehäusedeckels
Zurücksetzen des Batterie-Timers
Den Batterie-Timer (s. Abb 14 [14]) sofort nach dem Austauschen der Batterie zurücksetzen. Dabei wie folgt vorgehen:
Abb. 14 Batterie-Timer zurücksetzen
Justierung der Sensoren
Der Reflex-Lichttaster wird zum Werkstücknachweis, zur Farberkennung der Werkstücke und zur Überprüfung der Orientierung der Werkstücke eingesetzt. An ein Lichtleitergerät werden flexible Lichtleiter angeschlossen. Das Lichtleitergerät arbeitet mit sichtbarem Rotlicht. Das vom Werkstück reflektierte Licht wird nachgewiesen. Unterschiedliche Oberflächen und Farben der Werkstücke ändern den Reflexionsgrad.
Reflex-Lichttaster (Aufnahme, Werkstückerkennung)
Voraussetzungen:
- Modul Aufnahme und Lichtleitergerät montiert
- Elektrischer Anschluss des Lichtleitergerätes hergestellt
- Netzgerät eingeschaltet
Vorgehen:
1. Lichtleiterkopf in das Modul Aufnahme schrauben. Der Lichtleiterkopf ist bündig mit der Innenseite der Werkstückaufnahme.
2. Beide Lichtleiter am Lichtleitergerät montieren.
3. Ein schwarzes Werkstück in die Werkstückaufnahme legen.
4. Evtl. mit einem kleinen Schraubendreher an der Einstellschraube drehen, bis die Schaltzustandsanzeige (LED) einschaltet (max. 12 Umdrehungen der Einstellschraube sind zulässig).
5. Einstellung durch Einlegen schwarzer, roter und silberner Werkstücke (alle Werkstücke müssen sicher erkannt werden).
Reflex-Lichttaster (Greifer, Farberkennung)
Voraussetzungen:
- Roboter, Greifer und Lichteitergerät montiert
- Pneumatischer Anschluss des Greifers hergestellt
- Druckluftversorgung eingeschaltet
- Elektrischer Anschluss des Lichtleitergerätes hergestellt
- Netzgerät eingeschaltet
Vorgehen:
1. Lichtleiterkopf in den Greiferbacken schrauben.
2. Beide Lichtleiter am Lichtleitergerät montieren.
3. Ein rotes Werkstück in die Werkstückaufnahme legen. Den Greifer verfahren, bis der Reflex-Lichttaster zur Farberkennung im Greiferbacken auf die Mitte des Werkstückes zeigt. Der Abstand Reflex-Lichttasterkopf – Werkstück beträgt ca. 1 cm.
4. Evtl. mit einem kleinen Schraubendreher an der Einstellschraube drehen, bis die Schaltzustandsanzeige (LED) einschaltet (max. 12 Umdrehungen der Einstellschraube sind zulässig).
5. Ein schwarzes Werkstück in die Werkstückaufnahme legen. Den Greifer verfahren, bis der Reflex-Lichttaster zur Farberkennung im Greiferbacken auf die Mitte des Werkstückes zeigt. Der Abstand Reflex-Lichttasterkopf – Werkstück beträgt ca. 1 cm.
6. Evtl. mit einem kleinen Schraubendreher an der Einstellschraube drehen, bis die Schaltzustandsanzeige (LED) ausschaltet (max. 12 Umdrehungen der Einstellschraube sind zulässig).
7. Einstellung für schwarze, rote und silberne Werkstücke kontrollieren (rote und silberne Werkstücke müssen sicher erkannt werden. Schwarze Werkstücke dürfen nicht erkannt werden).
Reflex-Lichttaster (Aufnahme, Werkstückerkennung)
Voraussetzungen:
- Modul Montageaufnahme und Lichtleitergerät montiert
- Elektrischer Anschluss des Lichtleitergerätes hergestellt
- Netzgerät eingeschaltet
Vorgehen:
1. Den Lichtleiterkopf in das Modul Montageaufnahme schrauben. Der Lichtleiterkopf ist bündig mit der Oberseite der Befestigungsschraube.
2. Beiden Lichtleiter am Lichtleitergerät montieren.
3. Einen Deckel auf den Bolzen der Montageaufnahme setzen und den Deckel drehen bis eine Halteklammer im Erfassungsbereich des Reflex-Lichttasters ist.
4. Evtl. mit einem kleinen Schraubendreher an der Einstellschraube drehen, bis die Schaltzustandsanzeige (LED) einschaltet (max. 12 Umdrehungen der Einstellschraube sind zulässig).
5. Den Deckel drehen, bis die glatte Unterseite des Deckels im Erfassungsbereich des Reflex-Lichttasters ist. Die Schaltzustandsanzeige muss erlöschen.
Einbindung des Roboterarms in die MPS-Station
Zur Inbetriebnahme der MPS-Station Roboter wird benötigt:
- Die montierte und justierte MPS-Station
- Ein Steuergerät
- Eine Teaching Box
- Ein Netzgerät 24 V DC, 4,5 A
- Eine Druckluftversorgung mit 600 kPa (6 bar), Saugleistung ca. 50 l/min
- Einen PC mit installierter Roboter Programmiersoftware
Kombination von Stationen:
In der Standardversion werden MPS-Systeme mit optischen Sensoren gekoppelt. Diese Art der Kopplung wird als StationLink bezeichnet. Als StationLink Sensoren werden Einweg-Lichtschranken Sender und Empfänger verwendet. Der StationLink Sender ist auf der Materialeingangsseite der Station montiert, der StationLink Empfänger auf der Materialausgangsseite. Durch Ein- bzw. Ausschalten des StationLink Senders signalisiert die Station der Vorgängerstation, ob sie zur Aufnahme eines Werkstückes bereit ist oder ob sie belegt ist.
Die Sensoren zur Verkettung mehrerer Stationen müssen sich gegenüberstehen und fluchten. Die verketteten Stationen müssen über die Verbindungselemente sicher miteinander verbunden sein. Fluchten die Stationen richtig, so wird dies durch die grün leuchtenden LEDs der StationLink Sensoren bei der Vorbereitung zur Aufnahme eines Werkstückes kenntlich gemacht.
Fazit und Ausblick
Das Projekt "Ansteuerung des Mitsubishi Roboters" ist ein vielseitiges Projekt, welches sowohl für den Anfänger als auch für den fortgeschrittene Anwender geeignet ist. Das Lernsystem Automatisierung und Technik von Festo Didactic orientiert sich an unterschiedlichen Bildungsvoraussetzungen und beruflichen Anforderungen. Die Anlagen und Stationen des Modularen Produktions-Systems (MPS-System) ermöglichen eine an der betrieblichen Realität ausgerichtete Aus- und Weiterbildung. Die Hardware setzt sich aus didaktisch aufbereiteten Industriekomponenten zusammen.
Die Station Roboter liefert ein geeignetes System, mit dem die Schlüsselqualifikationen
- Sozialkompetenz,
- Fachkompetenz und
- Methodenkompetenz
praxisorientiert vermitteln werden. Zusätzlich können Teamfähigkeit, Kooperationsbereitschaft und Organisationsvermögen trainiert werden, die sowohl für den weiteren Verlauf des Studiums der Mechatronik als auch für das spätere Berufsleben von Vorteil sind.
Des Weiteren können z.B. in Lernprojekten die realen Projektphasen geschult werden. Hierzu gehören:
- Planung,
- Montage,
- Programmierung,
- Inbetriebnahme,
- Betrieb,
- Wartung und
- Fehlersuche.
Die Anforderungen an das Projekt wurden größtenteils erfüllt, jedoch konnte kein vollständig funktionierendes Programm erstellt werden. Des Weiteren konnte der Roboterarm aufgrund verschiedener Probleme nicht in das MPS-System eingebunden werden (s. Verbesserungsvorschläge).
Verbesserungsvorschläge/Aufgaben für zukünftige Projektteams:
- Das Einbinden des Industrieroboterarms in die MPS-Station hat nicht funktioniert, da die MPS-System - Stand Dezember 2016 - nicht betriebsbereit ist. Dies führt z.B. dazu, dass sich der Roboterarm in Schleifen von Programmen permanent aufhängt.
- Optiemierung der TEACH-Positionen.
- Überprüfen, ob alle notwendigen Kabel-, Steck- oder Druckluftverbindungen angeschlossen sind. Des Weiteren diese auf Funktionalität überprüfen. Gegebenenfalls Schäden beseitigen.
Sämtliche Daten, die zur Bearbeitung des Projektes erstellt und benötigt wurden, befinden sich im SVN der Hochschule.
Zurück zur Projektseite 3-D-Bearbeitungsmaschine (Projekt des Schwerpunkts GPE im Studiengang MTR)
Literatur
- ↑ Abbildung 1: Eigene Quelle, hochgeladen am 31.12.2016, 02:11 Uhr
- ↑ Abbildung 2: Eigene Quelle, Datei:Timeline.xlsx (Originaldatei), hochgeladen am 31.12.2016, 02:01 Uhr
- ↑ Abbildung 3: Datei:Technisches-Handbuch.pdf (Originaldatei), Mitsubishi Electric, Zugriff am 09.01.2017, 14:38 Uhr
- ↑ Abbildung 4: Datei:Technisches-Handbuch.pdf (Originaldatei), Mitsubishi Electric, Zugriff am 09.01.2017, 14:48 Uhr
- ↑ Abbildung 5: Datei:Technisches-Handbuch.pdf (Originaldatei), Mitsubishi Electric, Zugriff am 09.01.2017, 14:53 Uhr
- ↑ Abbildung 6: Datei:Technisches-Handbuch.pdf (Originaldatei), Mitsubishi Electric, Zugriff am 09.01.2017, 15:10 Uhr
- ↑ Abbildung 7: Datei:Technisches-Handbuch.pdf (Originaldatei), Mitsubishi Electric, Zugriff am 09.01.2017, 15:13 Uhr
- ↑ Abbildung 8: Datei:Technisches-Handbuch.pdf (Originaldatei), Mitsubishi Electric, Zugriff am 01.01.2017, 19:25 Uhr
- ↑ 9,0 9,1 Abbildung 9: Datei:Technisches-Handbuch.pdf (Originaldatei), Mitsubishi Electric, Zugriff am 01.01.2017, 19:32 Uhr
- ↑ Abbildung 10: Eigene Quelle, Datei:Mitsubishi Projekt Abschlusspräsentation.pptx (Originaldatei), hochgeladen am 03.01.2017, 02:02 Uhr
- ↑ Abbildung 11: Eigene Quelle, Datei:Mitsubishi Projekt Abschlusspräsentation.pptx (Originaldatei), hochgeladen am 03.01.2017, 02:03 Uhr
- ↑ 12,0 12,1 Abbildung 12: Datei:Technisches-Handbuch.pdf (Originaldatei), Mitsubishi Electric, Zugriff am 31.12.2016, 02:34 Uhr
- ↑ Abbildung 13: Datei:Technisches-Handbuch.pdf (Originaldatei), Mitsubishi Electric, Zugriff am 01.01.2017, 16:28 Uhr
- ↑ Abbildung 14: Datei:Technisches-Handbuch.pdf (Originaldatei), Mitsubishi Electric, Zugriff am 01.01.2017, 18:47 Uhr
Anhang
MELFA-BASIC-IV-Programmierbefehle:
Originalversion: Datei:Mitsubishi RV-1ARV-2AJ Bedienungs- und Programmieranleitung.pdf (Originaldatei), Mitsubishi Electric, Zugriff am 09.01.2017, 15:38 Uhr
Teil 1: http://193.175.248.52/wiki/index.php/Datei:Projekt_Mitsubishi_Programmierbefehle_Teil1.PNG, hochgeladen am 09.01.2017, 15:38 Uhr
Teil 2: http://193.175.248.52/wiki/index.php/Datei:Projekt_Mitsubishi_Programmierbefehle_Teil2b.PNG, hochgeladen am 09.01.2017, 15:47 Uhr
Teil 3: http://193.175.248.52/wiki/index.php/Datei:Projekt_Mitsubishi_Programmierbefehle_Teil3.PNG, hochgeladen am 09.01.2017, 15:49 Uhr
Teil 4: http://193.175.248.52/wiki/index.php/Datei:Projekt_Mitsubishi_Programmierbefehle_Teil4.PNG, hochgeladen am 09.01.2017, 15:50 Uhr