Konstruktion, Fertigung und Inbetriebnahme eines Rundtisches (4.Achse)
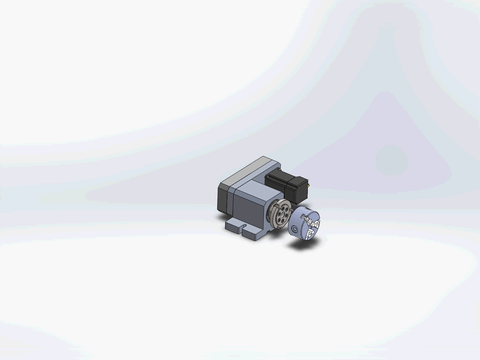
Dieses Teilprojekt des Projektes 3-D-Bearbeitungsmaschine (Projekt des Schwerpunkts GPE im Studiengang MTR) im siebten Semester des Studiengangs Mechatronik beinhaltet die Konzeptionierung, Konstruktion, Fertigung und erste Inbetriebnahme eines Rundtisches (4.Achse) im Rahmen des Praktikums der Produktionstechnik (GPE). Die Abbildung 1[1] rechts zeigt eine animierte Baugruppenexplosion des Baugruppe Rundtisch - ein Arbeitsergebnis des Teilprojektes. Zu sehen sind unter Anderem sämtliche Bauteile und Schraubelemente die Bestandteil der Baugruppe sind.
Autoren: Hendrik Buchheister, Kai Jacobs
Betreuer: Prof. Dr.-Ing. Göbel
Ausgangssituation und Problemstellung
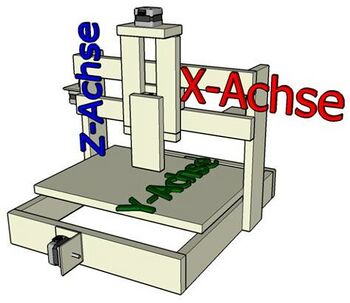
Ausgangssituation: Eine einfache Fräsmaschine verfährt, wie in den Abbildung 2[2] rechts dargestellt, auf den XYZ-Achsen zur translatorischen Werkstückmanipulation.
Die X-Achse verläuft in der Regel waagerecht. Die positive X-Achse verläuft (wenn man davor steht) nach rechts und die negative X-Achse nach links. Die positive Y-Achse verläuft bei Maschinen mit senkrechter Arbeitsspindel, wenn man direkt vor der Maschine steht, vom Betrachter weg. Die negative Y-Achse verläuft zum Betrachter hin. Die Z-Achse ist die Achse der Arbeitsspindel. Der positive Bereich der Z-Achse liegt zwischen dem Werkzeug und dem Werkstück. Der negative Bereich liegt unterhalb des Werkstücknullpunkts in die entgegengesetzte Richtung.[3]
Eine Drehbewegung des Werkstücks um die eigene Achse ist jedoch im gegebenen System nicht realisierbar. Die 4.Achse, je nach Ausführung auch Rund- oder Drehtisch genannt, ermöglicht eben diese rotatorische Werkstückbewegung. Der Rundtisch hat eine waagrechte Drehachse, um das aufgespannten Werkstück gedreht werden kann, um Bearbeitungen in verschiedenen Positionen oder am drehenden Werkstück vorzunehmen. Der Drehtisch hingegen hat eine vertikale Drehachse, um welche das Werkstück rotieren kann.
Passende Beispielvideos zur 4-Achs-Bearbeitung findet man auf YouTube unter folgenden Links:
- https://www.youtube.com/watch?v=oYdJZdeMTzE
- https://www.youtube.com/watch?v=pJ3CoQfOOXo
- https://www.youtube.com/watch?v=N6nGgLzkwxs
Problemstellung: Eine rotatorische Werkstückbewegung ist für die Fertigung von vielen Bauteilen notwendig. Aktuell kann an der CNC-Fräsmaschine eben diese Werkstückmanipulation nicht durchgeführt werden. Es sind lediglich translatorische Bewegungen auf den Achsen X,Y und Z möglich. Eine 4.Achse würde aber zusätzlich viele weitere Fräsoperationen zulassen und die Einsatzmöglichkeiten der Fräsmaschine deutlich erweitern.
Aufgabenstellung und Definition der Anforderungen
Aufgabenstellung: Aus der Problemstellung kann nun die Aufgabenstellung abgeleitet werden. Die Aufgabe ist es, eine geeignete 4.Achse für die Fräsmaschine in Betrieb zu nehmen. Dies setzt eine Konzeptionierung, eine Konstruktion sowie die Fertigung und Montage der einzelnen Bauteile des Rundtisches voraus. Die einzelnen Arbeitspakete gliedern sich wie folgt:
• Konzeptionierung: Unter Zuhilfenahme von Kreativitätstechniken soll ein geeignetes Lösungskonzept entwickelt werden. • Konstruktion: Das Lösungskonzept ist als 3D-Modell zu realisieren. Technische Zeichnungen sind ebenfalls zu erstellen. • Beschaffung: Bestellung fehlender Halbzeuge, Normteile oder sonstiger Zukaufteile zur Umsetzung des Lösungskonzeptes. • Fertigung und Montage: Die Halbzeuge sind eigenständig nach den techn. Zeichnungen zu fertigen. Alle Teile der Baugruppe sind anschließend zu fügen. • Inbetriebnahme: Durchführung erster Funktionstest mit elektrischer Ansteuerung.
Definition der Anforderungen: Folgende Rahmenbedingungen und Anforderungen wurden an die Projektlösung gestellt:
• Realisierung rotatorischer Werkstückbewegung • Konventioneller, simpler Aufbau • Schnelle Montage und Demontage des Systems • Gegenlager für lange Werkstücke • Verwendung der Alu-Strukturprofile • Spanndurchmesser bis ca. 80 mm • Budget bis maximal 500€ • Bestellung/ Beschaffung rechtzeitig auslösen • Lieferung bis Januar 2017
Konzeptionierung
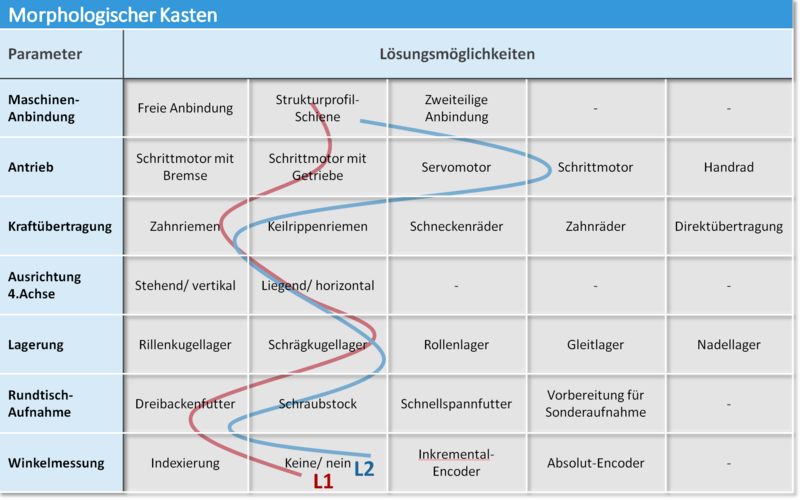
Gemäß den technischen und kommerziellen Anforderungen sind durch einen Morphologischen Kasten (siehe Abbildung 3[4]) die zwei Lösungskonzepte L1 und L2 entstanden. Die Grundidee der Kreativitätstechnik des Morphologischen Kastens ist es, verschiedene Kombinationen und Ausprägungen von möglichen Lösungen zu sammeln und zu untersuchen. Anhand der Auflistung aller Lösungsmöglichkeiten in einer Tabelle können nun durch die Auswahl einzelner Ausprägungen verschiedene Lösungskonzepte entstehen. Der Morphologische Kasten eignet sich besonders als Methode im Rahmen von Produktdefinitionen und Produktentwicklungen.[5]
Lösungskonzept L1
- Horizontal liegende 4.Achse mit Dreibackenfutter auf Strukturprofil-Schiene montiert.
- Antrieb über Schrittmotor PLUS Planetengetriebe und Kraftübertragung mittels Zahnriemen.
- Die Abtriebsachse ist mit Schrägkugellagern gelagert. Es erfolgt keine Winkelmessung.
Lösungskonzept L2
- Horizontal liegende 4.Achse mit Dreibackenfutter auf Strukturprofil-Schiene montiert.
- Antrieb über Schrittmotor OHNE Extra-Getriebe und Kraftübertragung mittels Zahnriemen.
- Die Abtriebsachse ist mit Schrägkugellagern gelagert. Es erfolgt keine Winkelmessung.
Erläuterungen zu den Konzepten
- Eine Strukturprofilschiene wird in beiden Konzepten verwendet. Diese kann im vorhandenen System positions- und lagegerecht montiert werden. Durch den Aufbau der Drehachse und des Gegenlagers auf diese Schiene wird auch eine funktional einwandfreie Flucht der Achsen gewährleistet. Somit lässt sich das eingespannte Werkstück mit lediglich minimalsten Rundlauf-Abweichungen rotatorisch manipulieren.
- Die Drehachse wird liegend ausgerichtet, da diese Ausrichtung für die vorhandenen Anwendungsszenarien die besseren Möglichkeiten zur Bearbeitung bietet.
- Eine Implementierung der Winkelmessung überschreitet das vorhandene Budget und wird somit nicht weiter berücksichtigt.
- Die Werkstückaufnahme erfolgt mittels Dreibackenfutter. Durch den Spannvorgang in einem Dreibackenfutter ist das Werkstück auf der Drehachse ausgerichtet und kann sauber im Gegenlager befestigt werden.
- Durch die Lagerung mittels Schrägkugellager können zu den rotatorischen Kräften auch axiale Kräfte aufgenommen werden. Durch eine doppelte Lagerung ist ebenfalls der einwandfreie Rundlauf gewährleistet.
- Konzept L1 verfügt über einen Schrittmotor MIT, Konzept L2 OHNE vorgeschaltetes Planetengetriebe.
Konzeptentscheid
Beide Konzepte sind bis auf die unterschiedlichen Schrittmotoren identisch (die technischen Daten des Schrittmotors NEMA23 können durch das Klicken hier eingesehen werden). Planetengetriebene Schrittmotoren haben den Vorteil ein höheres Haltemoment aufbringen zu können. Jedoch besteht das Risiko von Freilauf im Getriebe. Dadurch überträgt sich vorhandenes Spiel über den Zahnriemen direkt auf die Drehachse. Schrittmotoren ohne vorgeschaltetes Getriebe haben hingegen ein geringeres Haltemoment. Das mögliche Spiel im System ist bei diesem Konzept jedoch wesentlich geringer, da kein Getriebespiel vorgeschaltet ist. Es ist also eine Abwägung zwischen hohem Haltemoment und geringen Spiel notwendig gewesen.
Letztendlich wurde einstimmig entschieden, dass für die vorhandenen Anwendungsszenarien ein geringeres Spiel wichtiger als ein höheres Haltemoment ist.
Demnach fiel die Entscheidung auf Konzept L2.
Konstruktion
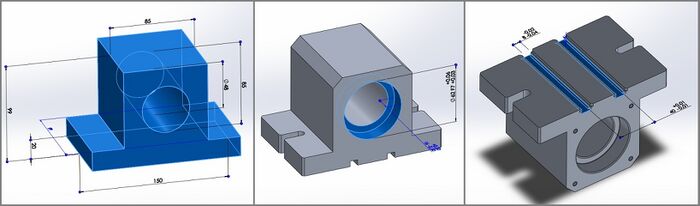
Modellierung
Die Modellierung des ausgewählten Konzeptes L2 wurde in SolidWorks durchgeführt. Die Abbildung 4[6] rechts zeigt die ersten Konstruktionsschritte am großen Gehäuse des Rundtisches. Zuerst wurde ein 3D-Objekt extrudiert und eine große Bohrung für den Einsatz der Welle geschaffen, sowie überflüssiges Material entfernt. Anschließend wurden Phasen gesetzt und seitliche Spannmöglichkeiten geschaffen. Darüber hinaus wurden die zum Einbau der Schrägkugellager notwendigen Passungsflächen konstruiert. Zum Abschluss wurden an der Unterseite des Gehäuses Nutenbahnen geschaffen, um die Baugruppe in Verbindung mit genormten Passfedern form- und lagegerecht auf der Aluminium-Strukturschiene auszurichten. Im Rahmen der Konstruktion der Baugruppe Rundtisch sind folgende Modelle entstanden:
- Welle
- Gehäuse
- Motorflansch
- Riemenabdeckung
- Planscheibe
- Zahnriemenrad (Abtriebsseite)
- Zahnriemenrad (Antriebsseite)
Im Rahmen der Konstruktion der Baugruppe Gegenlager sind folgende Modelle entstanden:
- Zentrierspitze
- Gehäuse
- Grundplatte
Zum Schluss wurden die einzelnen Modelle zu zwei Baugruppen zusammengefügt und noch um Kugellager, Schrauben, Muttern etc. erweitert. Die Abbildung 5[7] zeigt eine Schnittansicht durch das Rundtisch-Modell. In Abbildung 6[8] ist die 4.Achse ohne Schnitt und mit verbautem Schrittmotor (schwarzes Objekt) gezeigt.
Technische Zeichnungen
Zur Fertigungsüberleitung wurden aus den 3D-Modellen einzelne technische Zeichnungen mit umfangreicher Bemaßung und Werkstoffangabe erstellt. Nach DIN 199-1:2002-3stellt eine Einzelteilzeichnung das Einzelteil ohne räumliche Zuordnung zu anderen Bauteilen dar[9]. Diese technischen Zeichnungen sind zusammen mit dem .STEP-Dateien der Modelle im SVN-Ordner des Praktikums einzusehen. Zusätzlich zu den Einzelteilzeichnungen wurden auch sogenannte Explosionszeichnungen erstellt. Dies ist eine Art der Darstellung bei Zeichnungen, die einen komplexen Gegenstand perspektivisch und in seine Einzelteile zerlegt zeigt. Die dargestellten Einzelteile oder Bauteile sind räumlich voneinander getrennt (als flögen sie nach einer Explosion auseinander).
Folgende technischen Zeichnungen sind Arbeitsergebnis des Teilprojektes:
Gehäuse | (Rundtisch) | Media:NX-16200-001-A.PDF |
Welle | (Rundtisch) | Media:NX-16200-002-A.PDF |
Motorflansch | (Rundtisch) | Media:NX-16200-003-A.PDF |
Riemenabdeckung | (Rundtisch) | Media:NX-16200-004-A.PDF |
Planscheibe | (Rundtisch) | Media:NX-16200-005-A.PDF |
Zahnriemenrad | (Abtriebsseite) | Media:NX-16200-006-A.PDF |
Zahnriemenrad | (Antriebsseite) | Media:NX-16200-007-A.PDF |
Zentrierspitze | (Gegenseite) | Media:NX-16200-101-A.PDF |
Gehäuse | (Gegenseite) | Media:NX-16200-102-A.PDF |
Grundplatte | (Gegenseite) | Media:NX-16200-103-A.PDF |
Explosionszeichnung | (Rundtisch) | Media:NX-16200-000-A.PDF |
Explosionszeichnung | (Gegenseite) | Media:NX-16200-100-A.PDF |
Beschaffung
Die nachfogend aufgeführten Zukaufteile wurden beschafft:
• Rillenkugellager 6000 2RS • Schrägkugellager 7206 2RS • Passfeder DIN 6885 Form A 6 x 6 x 16 • Passfeder DIN 6885 Form A 10 x 8 x 25 • Zahnriemen HTD-3M 384 • Zahnriemen HTD-3M 363 • Zahnriemenrad HTD-3M 15 Zahn • Zahnriemenrad HTD-3M 72 Zahn • Harkenmutter DIN 1804 M28 x 1,5 • Passscheiben DIN 988 30 x 42 x 1,5 • Diverse Innensenchskantschrauben DIN 912 • 3 Backenfutter 80mm • Igus Schrittmotor Nema 23
Folgende Halbzeuge in angegebenen Maßen (inkl. Aufmaßen) wurden beschafft:
• Gehäuse EN-AW-5083 155 x 100 x 100 • Welle S355J2G3 Blankgezogen 150 x Ø50 • Motorflansch EN-AW-5083 205 x 20 x 80 • Riehmenabdeckung PVC 205 x 30 x 80 • Planscheibe S355J2G3 Blankgezogen 15 x Ø85 • Lagerblock EN-AW-5083 45 x 40 x 65 • Zentrierspitze S355J2G3 Blankgezogen 40 x Ø20 • Grundplatte EN-AW-5083 155 x 40 x 20
Fertigung und Montage
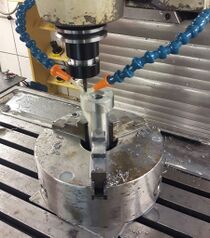
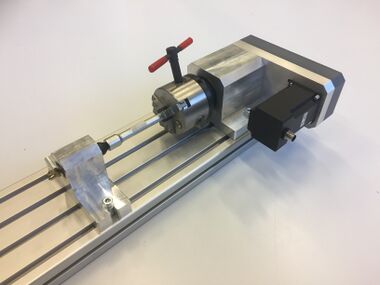
Die Zerspanung und das weitere Bearbeiten der Bauteile und Halbzeuge wurde in der heimischen Werkstatt vorgenommen. Zur Bearbeitung wurde unter Anderem eine CNC-Fräsmaschine sowie eine konventionelle Drehmaschine eingesetzt. Mit diversen Spiralfräsern, Schneidplatten und einem Messerkopf wurden die Bauteile nach den zuvor selbst erstellten technischen Zeichnungen zerspant. Die durchgeführten Arbeiten wurden mit einem digitalen Messschieber sowie mit verschiedenen Prüflehren auf Richtigkeit untersucht.
Die Abbildung 7[10] rechts zeigt dabei die Abtriebswelle im ersten Bearbeitungsschritt, dem Längs-Runddrehen. Die Abbildung 8[11] zeigt einen Fräsen bei der Bearbeitung der zuvor gedrehten Welle. Hier werden gerade die Bohrungen zur Aufnahme des Backenfutters gefertigt.
Die Montage der Baugruppe Rundtisch wurde in folgender Reihenfolge durchgeführt:
- Lager einsetzen
- Welle durch die Lager Schieben
- Passscheiben aufsetzen
- Passfeder einsetzen
- Zahnriehmenrad aufschieben
- Wellenmutter aufschrauben
- Lagerung vorspannen und Sichern
- Motorflansch montieren
- Schrittmotor aufsetzen
- Zahnriehmenrad montieren
- Zahnriehmen aufzeihen und spannen
- Zahnriemenabdeckung aufsetzen
- Passfeder einsetzen
Die Montage der Baugruppe Gegenlager wurde in folgender Reihenfolge durchgeführt:
- Lager einsetzen
- Zentrierspitze einfügen und Sichern
- Grundplatte befestigen
- Passfeder einsetzen
In Abbildung 9[12] ist dann die fertig montierte Baugruppe Rundtisch inklusive Gegenlager abgebildet. Zur fluchtenden Ausrichtung der beiden Drehachsen wird die Passfeder in die Schiene gesetzt und beide Baugruppen in die selbe Richtung gegen den Anschlag gedrückt. Anschließend sind die Innensechskantschrauben handfest anzuziehen. Mit dem Backenschlüssel kann das Futter geöffnet und geschlossen werden.
Inbetriebnahme
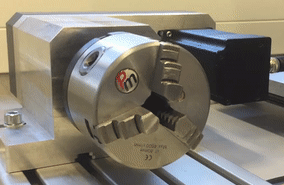
Die erste Inbetriebnahme wurde in einen mechanischen und einen elektrischen Funktionstest unterteilt. Die Abbildung 10[13] zeigt die vor- und zurücklaufende Achse beim elektrischen Funktionstest.
Damit ist der Aufgabenumfang des Teilprojektes erfüllt. Als Arbeitsergebnis liegt nun eine einsatzbereite 4.Achse zur Montage auf der CNC-Fräsmaschine vor.
Mechanischer Funktionstest:
- Überprüfung der Passungen (die Wellen sollte ohne spürbares Spiel gelagert werden)
- Drehen des Futters von Hand (es sollte mit wenig Anstrengung zu drehen sein und sollte bei Loslassen nicht nachlaufen)
- Betrachtung des Zahnriemen-Antriebes (der Zahnriemen sollte mittig auf den Rädern laufen und ausreichend gespannt sein)
- Öffnen und Schließen des Futters mit dem dazugehörigen Werkzeug
- Montage des Rundtisches und des Gegenlagers auf der Strukturschiene
Elektrischer Funktionstest:
- Ansteuerung des Schrittmotors mit Steuersignalen zum Verfahren der 4.Achse in beide Richtungen
- Prüfen des Haltemoments unter Strom (bei Einschalten des Motors sollte das Drehen von Hand mit mehr Anstrengung verbunden sein als)
Technische Daten der Baugruppe Rundtisch (4.Achse)
• Übersetzungsverhältnis: 4,8 • Auflösung Motor: 200 Schritte • Auflösung Welle: 960 Schritte • Max. Haltemoment: 9,6Nm • Nennstrom: 4,2A[14] • Nennspannung: 24-48V[15] • Gewicht: ca.6kg (inkl. Alu-Schiene und Gegenlager) • Möglicher Spanndurchmesser am Futter: 80mm
Schlussbetrachtung
Reflexion:
Schlussendlich war es die Aufgabe, eine 4.Achse eigenständig zu entwickeln, zu fertigen und in Betrieb zu nehmen. Die Zielsetzung wurde vollumfänglich erreicht. Als Arbeitsergebnis des Praktikums bleibt eine fertig montierte und einsatzbereite 4.Achse zurück. Das Projekt verlief planmäßig. Uns hat es vor allem sehr viel Spaß bereitet, unsere eigene Konstruktion auch selbst zu fertigen und in Betrieb zu nehmen.
Lessons learned:
Im Praktikum haben wir gelernt ein Projekt von Anfang bis Ende eigenständig durchzuführen. Von der ersten Idee, über die Konstruktion und Fertigung bis zur Inbetriebnahme wurden alle Schritte eigenständig durchgeführt. Zusätzlich haben wir erfahren, wie wichtig die Kommunikation im Projekt intern und extern ist. Nur durch Abstimmung und dem Festlegen von neuen Teilzielen mit dem Betreuer und in Kontakt mit den Arbeiten von anderen Gruppen konnte ein erfolgreicher Projektverlauf gewährleistet werden. Wir haben unsere Kenntnisse der Produktentwicklung und Konstruktion erweitert. Darüber hinaus konnten wir unsere Fertigkeiten im Umgang mit den Bearbeitungsmaschinen auffrischen und im Bereich des CNC-Fräsens erweitern.
Ausblick:
In Zukunft kann nun im Rahmen eines neuen Projektes in die Programmierung zur Ansteuerung der Achse durchgeführt und die Baugruppe stationär in der CNC-Fräsmaschine verkabelt werden. Allgemein sind künftig erste Fräsversuche erstrebenswert, um zu erfahren, welche Fräsoperationen nun in der Realität in Kombination mit dem gegebenen Maschinensystem möglich sind. Auch denkbar ist es eine Konstruktion zu schaffen, die die Baugruppe Rundtisch vertikal einspannt, damit auch die Fertigungsmöglichkeiten eines Drehtisches genutzt werden könnten.
Quellen
- ↑ Abbildung 1: eigene Quelle
- ↑ Abbildung 2: https://h2oengineering.files.wordpress.com/2011/07/xyz.jpg, Zugriff am 02.01.2017, 15:03 Uhr
- ↑ vgl. Ay, Cengiz (2017): X-, Y- und Z-Achsen in der CNC-Technik, https://www.cnc-lehrgang.de/achsen-im-cnc-koordinatensystem/, Zugriff am 02.01.2017, 15:01 Uhr
- ↑ Abbildung 3: eigene Quelle
- ↑ vgl. Zec, Marin (2017): Morphologischer Kasten, http://kreativitätstechniken.info/morphologischer-kasten-bzw-morphologische-analyse/, Zugriff am 02.01.2017, 15:34 Uhr
- ↑ Abbildung 4: eigene Quelle
- ↑ Abbildung 5: eigene Quelle
- ↑ Abbildung 6: eigene Quelle
- ↑ vgl. DIN 199-1:2002-3, Beuth Verlag, Berlin, 2002
- ↑ Abbildung 7: eigene Quelle
- ↑ Abbildung 8: eigene Quelle
- ↑ Abbildung 9: eigene Quelle
- ↑ Abbildung 10: eigene Quelle
- ↑ vgl. Igus GmbH (2017): Technische Daten, http://www.igus.de/wpck/7663/N11_6_14_2_Schrittmotor_NEMA23?C=DE&L=de, Zugriff am 04.01.2017, 17:34 Uhr
- ↑ vgl. Igus GmbH (2017): Technische Daten, http://www.igus.de/wpck/7663/N11_6_14_2_Schrittmotor_NEMA23?C=DE&L=de, Zugriff am 04.01.2017, 17:34 Uhr
Sonstiges
Autoren: Hendrik Buchheister, Kai Jacobs
Betreuer: Prof. Dr.-Ing. Göbel
Sprungmarke zur Projektübersicht 3-D-Bearbeitungsmaschine (Projekt des Schwerpunkts GPE im Studiengang MTR).