Aktoren in der Automatisierungstechnik
Einleitung
Die Aktoren, welche auch als Stellglied, Stellsystem oder Steller bezeichnet werden, bilden das Bindeglied zwischen Informationsfluss und Prozess. Dabei setzen sie die meist elektrischen Signale einer Steuerung oder Regelung in eine Kraft oder Bewegung um. Hier kommen verschiedene Hilfsenergien zum Einsatz. Die gängigsten Hilfsenergien sind Elektrizität, Hydraulik und Pneumatik. In der Automatisierungstechnik sind Aktoren weit verbreitet. Bei automatisierten Prozessen bilden sie nach Isermann(2008) die Stellglieder, welche bestimmte Eingangsgrößen von Prozessen ändern können. Die Abbildung 1 zeigt die Abhängigkeit zwischen der Informationsverarbeitung, den Aktor und dem eigentlichen Prozess.
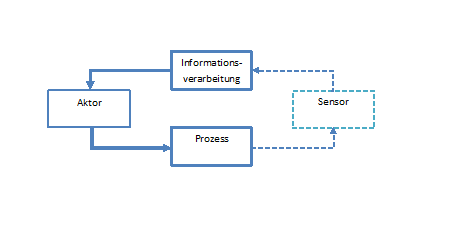
Da an die Automatisierungstechnik unterschiedliche Anforderungen gestellt werden und unterschiedliche Prozesse umsetzbar sind, existieren verschiedene Arten von Aktoren, welche in diesem Bericht kurz dargestellt werden. Die gängigsten Aktoren sind sowohl Elektromechanische Aktoren, welche in den unterschiedlichsten Bauformen und Größen in der Automatisierungstechnik zum Einsatz kommen, als auch pneumatische und hydraulische Aktoren.
Grundstrukturen von Aktoren
Nach Isermann(2008) gibt es zwei unterschiedliche Grundstrukturen von Aktoren, welche in Abbildung 2 und 3 dargestellt sind. Beide Grundstrukturen sind ähnlich aufgebaut. Die elektrisch übertragene Stellgröße Ue wird zuerst mit einem Signalumformer in eine zu dem Stellantrieb passende Steuergröße U1 umgewandelt. Bei elektrischen Antrieben kann das eine veränderte Spannung oder ein Taktsignal sein. Pneumatische Antriebe benötigen einen Luftstrom und hydraulische Antriebe einen Ölstrom. Mit der entstandenen Steuergröße wird mit Hilfe des Stellantriebs und seiner Hilfsenergie ein stärkeres Ausgangssignal U2. Dieses kann eine Kraft, eine Drehmoment oder Geschwindigkeit sein. Somit ist der Stellantrieb nach Isermann(2008) ein aktiver Wandler. Das entstandene Ausgangssignal muss meistens mit einem Stellüberträger verarbeitet werden, um für den Prozess genutzt werden zu können. Dieser kann beispielsweise bei Motoren ein Getriebe oder eine Spindel sein, um lineare Bewegungen zu erzeugen. Heraus kommt die nutzbare Ausgangsgröße U3. U4 bildet den ProzessstromBei dieser beschriebenen Struktur handelt es sich um einen gesteuerten Aktor.

Die zweite Grundstruktur in Abbildung 3 besitzt zusätzlich einen Stellantriebsregler, welcher die Stellgröße für den Prozess verändern kann. Hier handelt es sich um einen geregelten Aktor.
Der geregelte Aktor hat nach Isermann(2008) den Vorteil, bei Verschleiß von Komponenten oder veränderten Umweltbedingungen die Eingangsgröße direkt zu ändern. Hier werden Sensoren benötigt, welche die Ausgangsgrößen des Aktors überwachen. Da auf den einzelnen Komponenten Störungen oder Reibung und Verschleiß einwirken können, muss nach Isermann(2008) ebenfalls die Ausgangsgröße U3 mit einem Stellgliedregler geregelt werden. So können hohe Anforderungen an Präzision in der Automatisierungstechnik erfüllt werden. Hier sind interne Sensoren nötig, welche die einzelnen Komponenten überwachen. Der Stellgliedregler ändert den Sollwert Ue so, dass U3 mit der Führungsgröße U3w übereinstimmt. Das Stellglied selbst bildet einen weiteren Aktor, welcher von dem Signal U3 angesteuert wird und als Verstärker funktionieren soll. So kann das vergleichsweise schwache Signal U3 schwere Lasten, wie zum Beispiel Kräfte und Bewegungen, im Prozess steuern. Nach Isermann(2008) sind in einem Aktorsystem meist mehrere Verstärker vorhanden. Die entstehende Prozesseingangsgröße U4 kann mit einem weiteren Regler mit einer Führungsgröße U4w überwacht werden. So entsteht eine Kaskaden-Regelung.
Übersicht verschiedener Aktoren
Es existieren unterschiedliche Aktoren, welche unterschiedliche Hilfsenergien nutzen. Die Abbildung 4 zeigt mögliche Hilfsenergien und Prinzipien der Krafterzeugung. Die wichtigsten Hilfsenergien sind hier die Elektrischen Energien, Fluidenenergien, Chemische Energien und Thermische Energien. Das Prinzip der Krafterzeugung mittels elektrischer Energie ist zum Beispiel die Ausnutzung von Feldkräften, welche bei stromdurchflossenen Leitern entstehen.
Elektrische Energie ist fast überall verfügbar. Elektrische Antriebe haben einen hohen Wirkungsgrad und die nötige elektrische Energie lässt sich mit günstigen Bauteilen wie Relais und Spulen leicht steuern und wandeln. Daher kommen vorrangig elektrische Aktoren in der Automatisierungstechnik zum Einsatz. Der Öldruck für hydraulische Aktoren muss nach Isermann(2008) zuerst mit einem Hilfsenergieerzeuger bereitgestellt werden. Die gängigen Arbeitsdrücke sind zwischen 100 Bar und 400 Bar. Vorteilhaft sind nach Isermann(2008) die sehr großen Stellkräfte und robuste, kompakte Stellantriebe. Pneumatische Aktoren arbeiten entweder mit Unterdruck- oder Überdruckabweichung von dem Luftdruck der Atmosphäre. Die gängigsten Arbeitsdrücke sind nach Isermann(2008) in der Automatisierungstechnik auf 1,4 Bar begrenzt. Vorteile sind hier die Robustheit der Stellantriebe und ein sicherer Betrieb. Pneumatische Aktoren lassen sich auch bei hohen Temperaturen einsetzen. Aus diesen drei wichtigen Hilfsenergien bilden sich nach Isermann(2008) folgende Aktorprinzipien: -Elektromechanische Aktoren -Fluidenenergie Aktoren -Unkonventionelle Aktoren Diese Aktorprinzipien lassen sich weiter aufteilen. Die Tabelle 2 zeigt die Aufteilung.
Elektromechanische Aktoren
Es gibt eine große Vielfalt bei elektromechanischen Aktoren. Sie sind in fast allen Anwendungen der Automatisierungstechnik anwendbar. Bei kleinen und mittleren Stellleistungen sind sie nach Isermann(2008) vorherrschend. Mit zunehmender Stellleistung werden die Aktoren größer, da nach Isermann(2008) die physikalisch begrenzte Leistungsdichte von magnetischer Materialien zu großen Bauformen Führt. Elektromechanische Aktoren lassen sich nach Isermann(2008) in translatorische Aktoren ,wie Elektromagneten und Linearmotoren, und in rotatorische Elektromotoren unterteilen. In der Automatisierungstechnik werden spezielle Anforderungen an die Elektromotoren gestellt. Sie müssen nach Isermann(2008) nicht dauerhaft laufen, sondern Positionen bei Bedarf anfahren und halten können. So müssen die Motoren Überlastungen aushalten können und gleichzeitig eine hohe Positionsgenauigkeit besitzen. Für diese Anforderungen wurden Servomotoren entwickelt, welche über interne Sensoren Drehwinkel und Umdrehungen messen können. Sie können so bestimmte Positionen einnehmen und halten. Eine kostengünstige Alternative bildet der Schrittmotor, welcher eine Motorumdrehung in einzelne Schritte unterteilt. Diese Schritte können einzeln ausgeführt und deren Positionen mit Halteströmen gehalten werden. Die Abbildung 4 zeigt Servomotoren für die Automatisierungstechnik.
Außerdem kommen in der Automatisierungstechnik diverse günstige Elektromotoren vor, welche für spanende Fertigungstechniken geeignet sind. Hierzu zählen Gleichstrommotoren, Wechselstrommotoren und Asynchronmotoren. Nach Isermann(2008) eignen sich asynchrone Drehstrommotoren für hohe Drehzahlbereiche. Die Drehzahl kann mit einem Frequenzumrichter gesteuert werden. Die Drehzahl von Gleichstrommotoren und einphasige Wechselstrommotoren kann oft mit einer Pulsweitenmodulation verändert werden. Elektromagnete, welche translatorische Bewegungen erzeugen, funktionieren wie ein Hubelement, welches sich mit elektrischer Hilfsenergie auf kurzer Distanz schnell steuern lässt. Sie werden nach Isermann für die Stellung von pneumatischen und hydraulischen Aktoren benötigt. Hersteller von Elektromechanischen Aktoren sind zum Beispiel K&S Antriebssysteme GmbH, SEW Eurodrive und Baumüller Nürnberg GmbH.
Hydraulische Aktoren
Hydraulische Aktoren sind sehr robust. Nach Isermann(2008) können hydraulische Stellzylinder eine einfache und direkte Linearbewegung erzeugen. Hier sind sehr große Stellkräfte möglich. Die hydraulischen Stellzylinder lassen sich so gestalten, dass sie große Gegenkräfte mit wenig Leistung halten können. Zugleich ist die Bauform solcher Zylinder sehr kompakt, sodass große Stellkräfte in inem kleinen Raum erzeugt werden können. Nachteilig ist der geringere Wirkungsgrad von hydraulischen Aktoren im Vergleich zu elektromechanischen Aktoren und die beschränkte Verfügbarkeit der nötigen Hilfsenergie. Die Versorgung mit der Hilfsenergie erfolgt aus einem Öltank. Die Stellzylinder lassen sich nach Isermann(2008) über Ein- und Auslassventile ansteuern. Diese Ventile können den Ölstrom drosseln und so die Leistung des Stellzylinders beeinflussen. Das Öl kann mit einem elektrischen Antrieb in die hydraulischen Aktoren gepumpt werden. Mit Hilfe von Elektromagneten können die Ventile geöffnet oder geschlossen werden. Der Öldruck bewegt anschließend den im Zylinder befindlichen Kolben. Abbildung 5 zeigt einen einfachen hydraulischen Zylinder.
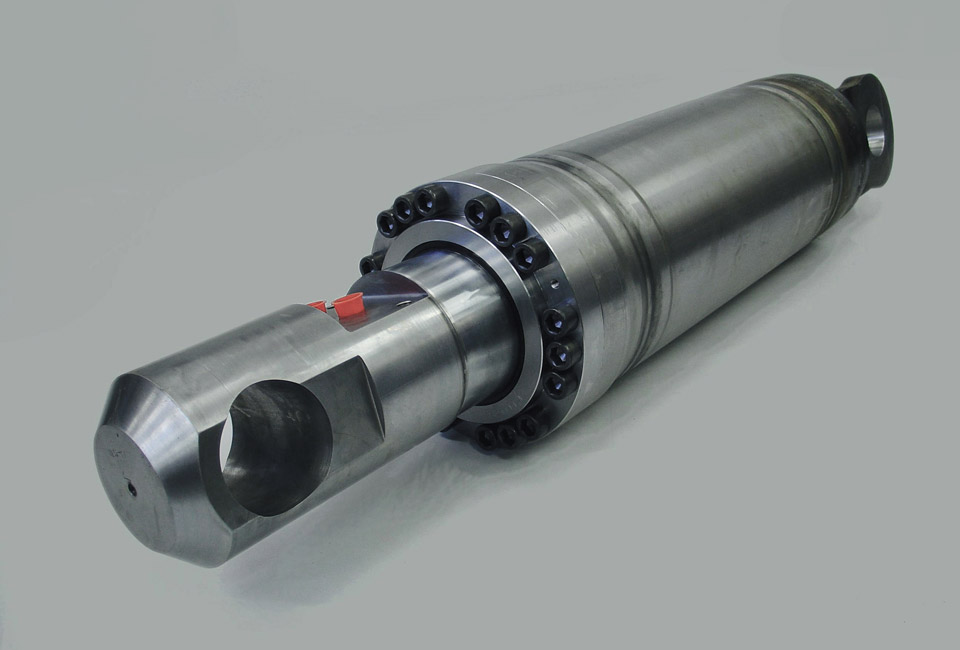
Manche Hydraulische Aktoren besitzen hydraulische Druckspeicher. Sie können auftretende Druckstöße dämpfen oder dazu benutzt werden, um Temperaturschwankungen auszugleichen. Für das Erreichen einer hohen Positioniergenauigkeit in der Automatisierungstechnik wurden nach Isermann(2008) speziell hydraulische Servostellzylinder entwickelt. Der Kolbenstand wird hier von integrierten Sensoren erfasst und kann mit Hilfe eines Reglers in die gewünschte Sollposition gestellt werden. diese Aktoren haben eine Positioniergenauigkeit von 10µm. Mit Hydraulikzylindern lassen sich nach Isermann(2008) auch rotatorische Bewegungen erzeugen. Hersteller von pneumatischen Aktoren sind zum Beispiel Hydropneu GmbH, HEB Hydraulik-Elementebau GmbH und Hydraulikzylinderbau GmbH.
Pneumatische Aktoren
Pneumatische Aktoren nutzen zuvor komprimierte Druckluft für die Krafterzeugung. Nach Isermann(2008) können einfach und robust aufgebaute pneumatische Antriebe mittlere Kräfte von mehreren 1000N. Pneumatische Aktoren reagieren schnell und die komprimierte Luft lässt sich über weite Distanzen mit Druckluftschläuchen transportieren. Solche pneumatischen Systeme können auch bei hohen Umgebungstemperaturen eingesetzt werden, wo Elektromotoren ungeeignet sind. Pneumatische Aktoren bestehen nach Isermann(2008) aus einem Stellventil und einem pneumatischen Stellmotor. Die Energie, welche in der Druckluft gespeichert ist, kann einen Druckluftmotor antreiben oder einen Stellzylinder bewegen und wird so in mechanische Energie umgeformt. So können translatorische und rotatorische Bewegungen erzeugt werden. In der Automatisierunstechnik wird die Luftzufuhr mit einem Kompressor erzeugt, welcher geregelt werden kann. Druckluftschläuche leiten die Luft zu dem Stellventil. Eine Rückführung der Luft ist nicht nötig, da sie nach Gebrauch in die Umgebung entweichen kann. Wie bei hydraulischen Aktoren werden die Ventile Pneumatischer Aktoren mit Elektromagneten gesteuert. Die Abbildung 6 zeigt die Bauform eines Pneumatischen Stellzylinders.
Pneumatische Aktoren kommen nach Isermann(2008) in der Automatisierunstechnik weitgehend bei dem Transport von Material und Montageaufgaben vor. Hersteller von pneumatischen Aktoren sind beispielsweise Riegler und Co. KG und Timmer-Pneumatik GmbH.
Unkonventionelle Aktoren
Die Entwicklung neuer Konzepte für Aktoren schreitet mit der Zeit weiter voran. Isermann bezeichnet diese Aktoren als Unkonventionelle Aktoren. Diese Aktoren sind in der Automatisierungstechnik noch nicht weit verbreitet, da neue Technologien anfangs zu teuer für die Industrie sind. Zum Beispiel sind Memory-Metalle nach Isermann(2008) spezielle Legierungen, welche bei einer bestimmten Temperatur eine bestimmte Form annehmen können. Bei Temperaturänderungen kann sich die Gitterstruktur der Legierung verändern und so die Form des Metalls ändern. Dabei können die Metalle Kräfte und Bewegungen erzeugen. Die Temperaturspanne bei Nickel-Titanium-Legierungen und bei Kupfer-Zink-Legierungen reicht hier von -100°c bis zu 100°c. Diese Metalle können mit einer elektrischen Heizung geregelt werden.
Fazit
In der Automatisierungstechnik kommen viele verschiedene Aktoren zum Einsatz. Dabei gibt es für jede Anwendung einen passenden Aktor. Es gibt zwei Grundstrukturen von Aktoren. Diese sind die gesteuerten Aktoren und die geregelten Aktoren. Der Vorteil der geregelten Aktoren besteht in der automatischen Anpassung der Sollgrößen bei auftretenden Störungen oder Änderungen in der Umgebung. Aktoren funktionieren wie Verstärker, welche Signale von einer Steuerung oder Regelung mit einer Hilfsenergie umwandeln und anschließend weiterleiten. Die wichtigsten Hilfsenergien sind in der Automatisierungstechnik die Elektrizität, Hydraulik und Pneumatik. Mit diesen Hilfsenergien können elektromechanische Aktoren, wie Elektromagneten und Elektromotoren, sowie hydraulische und pneumatische Aktoren angesteuert und angetrieben werden. Zu den hydraulischen Aktoren gehören hydraulische Stellzylinder. Pneumatische Aktoren können sowohl pneumatische Stellzylinder als auch Druckluftmotoren sein. Pneumatische und hydraulische Aktoren werden meist mit Elektromagneten gesteuerten Ventilen angesteuert.
Quellen
Literatur:
Isermann, Rolf: Mechatronische Systeme - Grundlagen: Springer Verlag Berlin Heidelberg New York, 2008
Internetquellen:
http://www.moog.de/produkte/servomotoren/cd-servomotoren/
http://www.okhydraulik.cz/de/produkte/zylinder_stahlwerke.html