Ansteuerung einer Schrittmotor-Achse mit Siemens SIMATIC S7-300 SPS: Unterschied zwischen den Versionen
Zeile 79: | Zeile 79: | ||
Somit müssen die zwischengeschalteten Widerstände zwischen 7,4kΩ und 8,2kΩ liegen. | Somit müssen die zwischengeschalteten Widerstände zwischen 7,4kΩ und 8,2kΩ liegen. | ||
=Versuchsdurchführung= | = Versuchsdurchführung = | ||
Nachdem alle Hardwarekomponenten miteinander verschaltet | Nachdem alle Hardwarekomponenten miteinander verschaltet und die benötigten Ausgangssignale mittels Widerständen dimensioniert wurden, konnte ein Großteil des Programmes zur Steuerung der Achsen geschrieben werden. | ||
[[Datei: rs1.jpg|mini|Beispiel Hardwarekonfiguration]] | [[Datei: rs1.jpg|mini|Beispiel Hardwarekonfiguration]] | ||
== Einbinden der Hardware in die Software == | |||
Um die Kommunikation zwischen der Software und der eingesetzten Hardware zu gewährleisten, ist es nötig diese zunächst über den Hardwarekonfigurator in die Software einzubinden. Hierzu wird die integrierte "HW Konfig" gestartet und alle benötigten Hardwarekomponenten aus der Hardwareauswahl in die Hardwarekonfiguration eingefügt. Anschließend werden diese über den Menüpunkt "Speichern und Laden" in die Software eingebunden. Wie die HW Konfig. nach erfolgreicher Einbindung der Hardware aussehen könnte, zeigt das Bild auf der rechten Seite. | |||
=== Ergänzung der Software durch manuelle Updates === | |||
Die verwendete CPU ist nicht im Standard-Hardwarekonfigurationspaket enthalten und muss manuell hinzugefügt werden. Dieses ist im Download-Bereich von Siemens zu finden und kann dort nach Anmeldung kostenfrei nachinstalliert werden. | |||
== Erstellen einer Symboltabelle == | |||
Im nächsten Schritt wird eine Symboltabelle für die Programmierung angelegt. In dieser Symboltabelle werden sowohl alle Ein - bzw. Ausgänge, als auch benötigte Merker und Zeiten definiert, welche für die Programmierung benötigt werden. Diese stehen symbolisch für die Speicherplätze im Adressspeicher der SPS. Die Symboltabelle kann nachträglich ergänzt und erweitert werden. Ein Beispiel für eine Symboltabelle zeigt nachfolgendes Bild: | |||
Im nächsten Schritt wird eine Symboltabelle für die Programmierung angelegt. In dieser | |||
Ein Beispiel für eine Symboltabelle zeigt nachfolgendes Bild: | |||
[[Datei:symbolled.jpg|large| Symboltabelle]] | [[Datei:symbolled.jpg|large| Symboltabelle]] | ||
====Programmierung==== | ====Programmierung==== | ||
[[Datei:Step_prog.jpg|mini|Schrittbaustein]] | /*[[Datei:Step_prog.jpg|mini|Schrittbaustein]]*/ | ||
Eine Siemens SPS kann in mit der Entwicklungsumgebung Step 7 in verschiedenen Sprachen programmiert werden. Die verfügbaren Programmiersprachen gliedern sich in AWL (Anweisungsliste), KOP (Kontaktplan) und FUP (Funktionsplan). Diese 3 Programmiersprachen richten sich an ganz unterschiedliche Anwendertypen. AWL ähnelt in seiner Anwendung der Assembler-Programmierung und richtet sich an erfahrene Softwareentwickler. Ein KOP-Programm erinnert an einen elektrischen Schaltplan und richtet sich daher an Anwender aus dem Elektrotechnischen Bereich. FUP stellt einen übersichtlichen Funktionsplan dar, wodurch die Programmierung auch für Laien verständlicher ist. | |||
Jedes Programm wird mit Hilfe von Bausteinen erstellt, welche sich wie folgt gliedern: | |||
{| border="1" | |||
!Anwenderbaustein | |||
Der | !Abkürzung | ||
!Erläuterung | |||
|- | |||
|Organisationsbaustein | |||
|OB | |||
|Steuerwerk der Programmbausteine, wird zyklisch aufgerufen | |||
|- | |||
|Funktionsbaustein | |||
|FB | |||
|Zugeordneter Speicherbereich, greift auf Daten aus Datenbaustein zu | |||
|- | |||
|Funktion | |||
|FC | |||
|keinen Zugeordneten Speicherbereich, lokale Daten gehen nach Aufruf verloren | |||
|- | |||
|Datenbaustein | |||
|DB | |||
|Stellen Speicherplatz für Datenvariablen bereit, Globale & Instant – DBs | |||
|- | |||
|Systemfunktionsbaustein | |||
|SFB | |||
|Im Betriebssystem der CPU hinterlegt, vom Anwender aufrufbar | |||
|- | |||
|Systemfunktion | |||
|SFC | |||
|Im Betriebssystem der CPU hinterlegt, vom Anwender aufrufbar | |||
|- | |||
|Systemdaten | |||
|SDB | |||
|Datenspeicherung für das Automatisierungssystem | |||
|- | |||
|} | |||
Jede Art von Baustein ist für spezifische Anforderungen geeignet. Der Start eines Programmes erfolgt dabei stets im OB1. | |||
== Zyklischer Ablauf == | |||
Der Programmablauf einer SPS verläuft zyklisch. Das bedeutet, dass der Organisationsbaustein OB1 zyklisch aufgerufen wird. Alle darin enthalten Aufrufe weiterer Funktionen und Funktionsbausteine werden nacheinander ausgeführt. Anschliessend beginnt der Zyklus erneut. | |||
Dabei ist zu beachten, dass Eingänge hardwarebedingt nur vor einem Programmzyklus eingelesen werden können und Ausgänge nur nach Abschluss eines Programmzyklus angesteuert werden können. Innerhalb eines Programmzyklus ist das Einlesen und Ausgeben von digitalen Ein- und Ausgängen nicht möglich. | |||
== Zykluszeit == | |||
Die Zykluszeit ist die Zeit, die das Betriebssystem für die Bearbeitung eines Programmdurchlaufes - d. h. eines OB 1-Durchlaufes - sowie aller in diesem Durchlauf untergebrachten Programmteile und Systemtätigkeiten. Diese Zeit wird überwacht. Die Zykluszeit je Schritt im Programm ist mit 2ms angegeben. | |||
Für folgendes Beispielprogramm wurde eine tatsächliche Zykluszeit von etwa 5,4ms ermittelt. | |||
[[Datei:Step_prog.jpg|mini|Beispielprogramm für einen Schrittbaustein]] | |||
[[Datei:Zykluszeit.jpg|mini|x350px|am Oszilloskop gemessene tatsächliche Zykluszeit]] | |||
Diese Verzögerung wird durch unterschiedliche Einflussfaktoren verursacht. Im Folgenden werden die Wichtigsten genannt: | |||
* Grundlast (K) | |||
* Anzahl Bytes im Baugruppenträger 0 (A) | |||
* Anzahl Bytes im Baugruppenträger 1 bis 3 (B) | |||
* Verlängerung der Anwenderprogramm - Bearbeitungszeit | |||
*Grundlast (K) | |||
*Anzahl Bytes im Baugruppenträger 0 (A) | |||
*Anzahl Bytes im Baugruppenträger 1 bis 3 (B) | |||
*Verlängerung der Anwenderprogramm - Bearbeitungszeit | |||
Im | Das Betriebssystem Ihrer CPU führt neben der eigentlichen Abarbeitung des Anwenderprogramms noch weitere zeitgleiche Prozesse durch (z. B. Timerverwaltung des Kernbetriebssystems). Diese Prozesse verlängern die Bearbeitungszeit des Anwenderprogramms. Daher muss bei der Berechnung der Zykluszeit mit dem Bearbeitungszeit-Faktor multipliziert werden. Für CPU313C beträgt dieser Faktor 1,10. | ||
Im Folgenden sind die Einflussfaktoren, die für die Berechnung der Zykluszeit notwendig sind, aufgelistet: | |||
{| border="1" | {| border="1" | ||
!Konstante | !Konstante | ||
Zeile 132: | Zeile 169: | ||
|} | |} | ||
Die berechnete Zykluszeit ergibt sich aus der Summe aller folgenden Einflussfaktoren: | |||
Zykluszeit_verzögert(Z_ver)=(Z+A+B+K) * 1,10. | |||
In dieser Formel ist A=0, weil im Versuchsaufbau der Baugruppenträger 0 nicht gebraucht wird. Der Faktor B wird mit 4 multipliziert, da man im Baugruppenträger 32 Bit(digitale Input und Output)= 4 Byte hat. Daher lautet die Formel: | |||
Die berechnete Zykluszeit ergibt sich aus der Summe aller folgenden Einflussfaktoren: | |||
Zykluszeit_verzögert :Z_ver =(Z+B+K) * 1,10. | |||
Z_ver=(2ms+(4 * 0,0043 ms)+100ms) * 1,10 = 5,192 ms | |||
Je nach Programmablauf kann die Zykluszeit variieren. Dies wird verursacht durch: | |||
* bedingte Befehle | |||
* bedingte Bausteinaufrufe | |||
* unterschiedliche Programmpfade | |||
* Schleifen usw. | |||
== Auswahl der Programmiersprache == | |||
Bei der Auswahl der Programmiersprache fiel die Wahl auf AWL. Diese ist zwar schwieriger zu Programmieren, bietet jedoch im Gegensatz zu KOP und FUP mehr Möglichkeiten in der Programmgestaltung. KOP und FUP stellen nur einen Bruchteil der in AWL verfügbaren Funktionen zur Verfügung. | |||
== Programmablaufplan == | |||
Zur Planung der zu programmierenden Software wurde zunächst ein Programmablaufplan erstellt | |||
== Serielle Kommunikation mit CP340 == | |||
Das Modul CP340 ermöglicht eine serielle Kommunikation über einen RS232-Bus. Über diesen Bus werden die Koordinaten vom Steuerungsalgorithmus an die SPS übertragen. Die Datenübertragung erfolgt als String im ASCII-Format. Bei der Konfiguration ist darauf zu achten, dass in den Einstellungen des CP340-Moduls die Datenübertragung auf das ASCII-Format eingestellt ist. | |||
Der übertragene String ist wie folgt aufgebaut: | |||
* Referenzfahrt: U12345V12345W12345; | |||
* Koordinatenpunkt: X12345Y12345Z12345F12345; | |||
Mittels der Referenzfahrt wird der Steuerung ein Referenzkoordinatenpunkt übermittelt, welcher die aktuellen Positionen der Achsen repräsentiert. Dieser muss zu Beginn jedes Fräsvorganges einmalig übermittelt werden um dem System seine Ursprungskoordinaten mitzuteilen. U repräsentiert hierbei die X-Achse, V die Y-Achse und W die Z-Achse. Die darauffolgenden Zahlen stehen für die Koordinaten der jeweiligen Achse in 1/100mm. | |||
Über den Koordinatenpunkt wird der Steuerung die nächste Zielkoordinate übermittelt. X, Y und Z repräsentieren die jeweilige Achse, F steht für den Vorschub. Auch hier beträgt die Maßeinheit 1/100mm. | |||
== Verarbeitung der Koordinaten == | |||
Zu Beginn des Programmes wird überprüft, ob der empfangene String valide ist und es sich hierbei um eine Referenzfahrt oder einen anzusteuernden Koordinatenpunkt handelt. | |||
Anschliessend werden die einzelnen Koordinaten aus dem String extrahiert und in das Format Double-Integer umgewandelt um damit im weiteren Programmablauf rechnen zu können. | |||
Aus der Differenz zwischen Soll- und Ist-Koordinate wird die Verfahrstrecke je Achse ermittelt. Das Vorzeichen der Verfahrstrecke stellt die Richtung der jeweiligen Achse dar. | |||
Am Ende des Programmzyklus werden die Soll-Koordinaten als Ist-Koordinaten für den darauffolgenden Zyklus gespeichert. | |||
= Weblinks und Literatur = | |||
====Aufbau SIMATIC S7-300==== | ====Aufbau SIMATIC S7-300==== | ||
Version vom 12. Januar 2017, 18:08 Uhr
Einleitung
Im Rahmen des Studiengangs Mechatronik der Hochschule Hamm-Lippstadt wird im 7. Fachsemester das Praktikum Produktionstechnik angeboten. Dieses Praktikum ist Teil des Fach-Moduls Global Production Engineering. In diesem Praktikum geht es um die Verwirklichung eines mechatronischen Produktionssystems (MPS) mittels Speicher Programmierbarer Steuerung (SPS), sowie die Ansteuerung von 3 Schrittmotor-Achsen im Rahmen des Hauptprojektes "Aufbau einer 3-D-Bearbeitungsmaschine".
Das Thema Ansteuerung einer Schrittmotor-Achse mit Siemens SIMATIC S7-300-CPU313C ist ein Teilthemengebiet des Projekts 3-D-Bearbeitungsmaschine und wurde von Stefan Schweins, Jonas Rüschenschmidt, sowie im darauffolgenden Jahr von Hendrik Pabst und Ziad Abuelkhair bearbeitet. Im Anschluss haben Pascal Siekmann und Gerhard Dick das Projekt fortgeführt.
Aufgabenstellung
Die Aufgabe des Praktikums war es, eine 3-D Bearbeitungsmaschine zu konstruieren und drei Achsen mit verschiedener Steuerungshardware anzusteuern. Ebenfalls sollten Bearbeitungskoordinaten für Werkstücke übermittelt werden können.
Die Aufgabe bestand darin, die Ansteuerung einer Zahnriemenachse mit Schrittmotor durch den Einsatz von einer speicherprogrammierbaren Steuerung, - kurz SPS, SIMATIC S7-CPU300-313C des Unternehmens Siemens zu realisieren.
Zur Ansteuerung der Schrittmotoren kommen GeckoDrive-Schrittmotortreiber zum Einsatz. Die Aufgabenstellung gliedert sich in folgende Teilaufgaben:
Aufbau
- Einlesen und Einregeln der Soll-Position mittels RS232-Schnittstelle
- Hardwareanalyse und Hardwareaufbau sowie Hinzunahme von Pulldown-Widerständen für die Endschaltersteuerung
Kabelfertigung
Test der Ansteuerung
- Ausgabe eines digitalen Signals am Ausgang der SPS
Leistungsstufe ansteuern
- Programmierung
- Test mit abgeschraubter Verfahreinheit
- Test und Inbetriebnahme der Endschalter
- Dateneingabe über Arduino-Monitor
- Achsenansteuerung für mehrere Achsen duplizieren und einlesen einer definierten Stringfolge
Test mit Steuerungsalgorithmus
- Kommunikation mit Matlab-Steuerungsalgorithmus testen
- Programmier-Review
Vewendete Hardware
- SIEMENS Hutschiene
- SIMATIC PS307
- SIMATIC S7-300-CPU313C
- SIMATIC CP340
- GeckoDrive G201x
- Leitung 25-polig
- Stecker Sub-D 25-polig
- Endschalter
- Widerstände 7,2 kOhm – 8,4 kOhm
- Pulldown-Widerstände
Verwendete Software
Siemens Simatic Step7 Manager
Eine Entwicklungsumgebung von Siemens zur Programmierung von Siemens SPS-Steuerungen.
Siemens Lizenzmanager
Die Verwendung von Siemens Step 7 ist nur unter Nutzung eines aktuellen Lizenzkeys möglich. Dieser muss zunächst über den Siemens Lizenzmanager in das Softwarepaket eingebunden werden.
HTerm
Die kostenfreie Software HTerm ermöglicht eine serielle Kommunikation über den RS232-Bus. Mit dieser wurde die serielle Schnittstelle eingerichtet und auf Ihre Funktion geprüft.
Versuchsaufbau
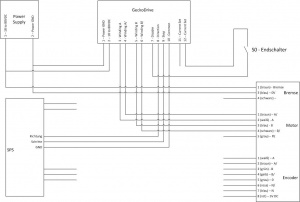
Verschaltung der Bauelemente
Um alle Hardwarekomponenten miteinander verbinden zu können, wurde ein Schaltplan erstellt, welcher die Verschaltung aller Bauteile veranschaulicht.
Dimensionierung der Ausgangssignale
Um ein Schritt - bzw. Richtungs - Signal an eine Achse zu übertragen ist es notwendig die Signale an den Schrittmotortreiber zu senden, welcher den Schrittmotor ansteuert. Die Signale des SPS Moduls werden mit 24V ausgegeben, diese Spannung ist jedoch als Eingangsspannung für das GeckoDrive nicht geeignet, da dieser mit einer Spannung von 3.3V bis 5.5V arbeitet. Um zu gewährleisten, dass das GeckoDrive nicht beschädigt wird und die Signale richtig verarbeitet werden können, mussten die ensprechenden Ausgangssignale der S7 -300 neu dimensioniert werden. Hierfür wurden Widerstände zwischen den digitalen Ausgang des Step - bzw. Direction - Pins und den Eingang der jeweiligen Pins am GeckoDrive geschaltet. Um die Widerstande richtig bestimmen zu können, wurden Sie durch folgende Berechnung festgelegt:
- Spannung der digitalen Ausgänge = 24V
- Benötigte Spannung des Direction - Pins = 3,3V bis 5,5V
- Benötigte Spannung des Step - Pins = 3,3V bis 5,5V
R= U/I Ohmsches Gesetzt
R = (24V - 3,3V)/2,5mA = 8,2kΩ
R = (24V - 5,5V)/2,5mA = 7,4kΩ
Somit müssen die zwischengeschalteten Widerstände zwischen 7,4kΩ und 8,2kΩ liegen.
Versuchsdurchführung
Nachdem alle Hardwarekomponenten miteinander verschaltet und die benötigten Ausgangssignale mittels Widerständen dimensioniert wurden, konnte ein Großteil des Programmes zur Steuerung der Achsen geschrieben werden.
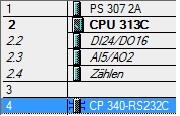
Einbinden der Hardware in die Software
Um die Kommunikation zwischen der Software und der eingesetzten Hardware zu gewährleisten, ist es nötig diese zunächst über den Hardwarekonfigurator in die Software einzubinden. Hierzu wird die integrierte "HW Konfig" gestartet und alle benötigten Hardwarekomponenten aus der Hardwareauswahl in die Hardwarekonfiguration eingefügt. Anschließend werden diese über den Menüpunkt "Speichern und Laden" in die Software eingebunden. Wie die HW Konfig. nach erfolgreicher Einbindung der Hardware aussehen könnte, zeigt das Bild auf der rechten Seite.
Ergänzung der Software durch manuelle Updates
Die verwendete CPU ist nicht im Standard-Hardwarekonfigurationspaket enthalten und muss manuell hinzugefügt werden. Dieses ist im Download-Bereich von Siemens zu finden und kann dort nach Anmeldung kostenfrei nachinstalliert werden.
Erstellen einer Symboltabelle
Im nächsten Schritt wird eine Symboltabelle für die Programmierung angelegt. In dieser Symboltabelle werden sowohl alle Ein - bzw. Ausgänge, als auch benötigte Merker und Zeiten definiert, welche für die Programmierung benötigt werden. Diese stehen symbolisch für die Speicherplätze im Adressspeicher der SPS. Die Symboltabelle kann nachträglich ergänzt und erweitert werden. Ein Beispiel für eine Symboltabelle zeigt nachfolgendes Bild:
Programmierung
/*
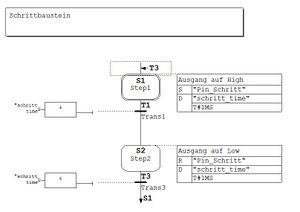
*/
Eine Siemens SPS kann in mit der Entwicklungsumgebung Step 7 in verschiedenen Sprachen programmiert werden. Die verfügbaren Programmiersprachen gliedern sich in AWL (Anweisungsliste), KOP (Kontaktplan) und FUP (Funktionsplan). Diese 3 Programmiersprachen richten sich an ganz unterschiedliche Anwendertypen. AWL ähnelt in seiner Anwendung der Assembler-Programmierung und richtet sich an erfahrene Softwareentwickler. Ein KOP-Programm erinnert an einen elektrischen Schaltplan und richtet sich daher an Anwender aus dem Elektrotechnischen Bereich. FUP stellt einen übersichtlichen Funktionsplan dar, wodurch die Programmierung auch für Laien verständlicher ist. Jedes Programm wird mit Hilfe von Bausteinen erstellt, welche sich wie folgt gliedern:
Anwenderbaustein | Abkürzung | Erläuterung |
---|---|---|
Organisationsbaustein | OB | Steuerwerk der Programmbausteine, wird zyklisch aufgerufen |
Funktionsbaustein | FB | Zugeordneter Speicherbereich, greift auf Daten aus Datenbaustein zu |
Funktion | FC | keinen Zugeordneten Speicherbereich, lokale Daten gehen nach Aufruf verloren |
Datenbaustein | DB | Stellen Speicherplatz für Datenvariablen bereit, Globale & Instant – DBs |
Systemfunktionsbaustein | SFB | Im Betriebssystem der CPU hinterlegt, vom Anwender aufrufbar |
Systemfunktion | SFC | Im Betriebssystem der CPU hinterlegt, vom Anwender aufrufbar |
Systemdaten | SDB | Datenspeicherung für das Automatisierungssystem |
Jede Art von Baustein ist für spezifische Anforderungen geeignet. Der Start eines Programmes erfolgt dabei stets im OB1.
Zyklischer Ablauf
Der Programmablauf einer SPS verläuft zyklisch. Das bedeutet, dass der Organisationsbaustein OB1 zyklisch aufgerufen wird. Alle darin enthalten Aufrufe weiterer Funktionen und Funktionsbausteine werden nacheinander ausgeführt. Anschliessend beginnt der Zyklus erneut. Dabei ist zu beachten, dass Eingänge hardwarebedingt nur vor einem Programmzyklus eingelesen werden können und Ausgänge nur nach Abschluss eines Programmzyklus angesteuert werden können. Innerhalb eines Programmzyklus ist das Einlesen und Ausgeben von digitalen Ein- und Ausgängen nicht möglich.
Zykluszeit
Die Zykluszeit ist die Zeit, die das Betriebssystem für die Bearbeitung eines Programmdurchlaufes - d. h. eines OB 1-Durchlaufes - sowie aller in diesem Durchlauf untergebrachten Programmteile und Systemtätigkeiten. Diese Zeit wird überwacht. Die Zykluszeit je Schritt im Programm ist mit 2ms angegeben. Für folgendes Beispielprogramm wurde eine tatsächliche Zykluszeit von etwa 5,4ms ermittelt.
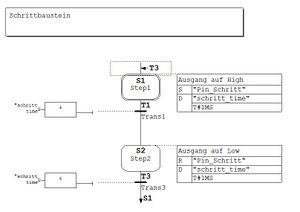
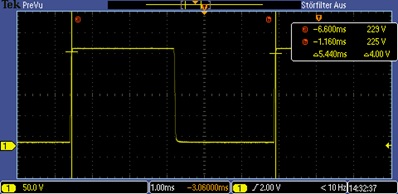
Diese Verzögerung wird durch unterschiedliche Einflussfaktoren verursacht. Im Folgenden werden die Wichtigsten genannt:
- Grundlast (K)
- Anzahl Bytes im Baugruppenträger 0 (A)
- Anzahl Bytes im Baugruppenträger 1 bis 3 (B)
- Verlängerung der Anwenderprogramm - Bearbeitungszeit
Das Betriebssystem Ihrer CPU führt neben der eigentlichen Abarbeitung des Anwenderprogramms noch weitere zeitgleiche Prozesse durch (z. B. Timerverwaltung des Kernbetriebssystems). Diese Prozesse verlängern die Bearbeitungszeit des Anwenderprogramms. Daher muss bei der Berechnung der Zykluszeit mit dem Bearbeitungszeit-Faktor multipliziert werden. Für CPU313C beträgt dieser Faktor 1,10.
Im Folgenden sind die Einflussfaktoren, die für die Berechnung der Zykluszeit notwendig sind, aufgelistet:
Konstante | Anteile | CPU313C_Bearbeitungszeit |
---|---|---|
K | Grundlast | 100µS |
A | je Byte in Baugruppenträger 0 | 35µS |
B | je Byte in Baugruppenträger1 bis 3 | 43µs |
Die berechnete Zykluszeit ergibt sich aus der Summe aller folgenden Einflussfaktoren: Zykluszeit_verzögert(Z_ver)=(Z+A+B+K) * 1,10. In dieser Formel ist A=0, weil im Versuchsaufbau der Baugruppenträger 0 nicht gebraucht wird. Der Faktor B wird mit 4 multipliziert, da man im Baugruppenträger 32 Bit(digitale Input und Output)= 4 Byte hat. Daher lautet die Formel:
Zykluszeit_verzögert :Z_ver =(Z+B+K) * 1,10.
Z_ver=(2ms+(4 * 0,0043 ms)+100ms) * 1,10 = 5,192 ms
Je nach Programmablauf kann die Zykluszeit variieren. Dies wird verursacht durch:
- bedingte Befehle
- bedingte Bausteinaufrufe
- unterschiedliche Programmpfade
- Schleifen usw.
Auswahl der Programmiersprache
Bei der Auswahl der Programmiersprache fiel die Wahl auf AWL. Diese ist zwar schwieriger zu Programmieren, bietet jedoch im Gegensatz zu KOP und FUP mehr Möglichkeiten in der Programmgestaltung. KOP und FUP stellen nur einen Bruchteil der in AWL verfügbaren Funktionen zur Verfügung.
Programmablaufplan
Zur Planung der zu programmierenden Software wurde zunächst ein Programmablaufplan erstellt
Serielle Kommunikation mit CP340
Das Modul CP340 ermöglicht eine serielle Kommunikation über einen RS232-Bus. Über diesen Bus werden die Koordinaten vom Steuerungsalgorithmus an die SPS übertragen. Die Datenübertragung erfolgt als String im ASCII-Format. Bei der Konfiguration ist darauf zu achten, dass in den Einstellungen des CP340-Moduls die Datenübertragung auf das ASCII-Format eingestellt ist.
Der übertragene String ist wie folgt aufgebaut:
- Referenzfahrt: U12345V12345W12345;
- Koordinatenpunkt: X12345Y12345Z12345F12345;
Mittels der Referenzfahrt wird der Steuerung ein Referenzkoordinatenpunkt übermittelt, welcher die aktuellen Positionen der Achsen repräsentiert. Dieser muss zu Beginn jedes Fräsvorganges einmalig übermittelt werden um dem System seine Ursprungskoordinaten mitzuteilen. U repräsentiert hierbei die X-Achse, V die Y-Achse und W die Z-Achse. Die darauffolgenden Zahlen stehen für die Koordinaten der jeweiligen Achse in 1/100mm. Über den Koordinatenpunkt wird der Steuerung die nächste Zielkoordinate übermittelt. X, Y und Z repräsentieren die jeweilige Achse, F steht für den Vorschub. Auch hier beträgt die Maßeinheit 1/100mm.
Verarbeitung der Koordinaten
Zu Beginn des Programmes wird überprüft, ob der empfangene String valide ist und es sich hierbei um eine Referenzfahrt oder einen anzusteuernden Koordinatenpunkt handelt.
Anschliessend werden die einzelnen Koordinaten aus dem String extrahiert und in das Format Double-Integer umgewandelt um damit im weiteren Programmablauf rechnen zu können.
Aus der Differenz zwischen Soll- und Ist-Koordinate wird die Verfahrstrecke je Achse ermittelt. Das Vorzeichen der Verfahrstrecke stellt die Richtung der jeweiligen Achse dar.
Am Ende des Programmzyklus werden die Soll-Koordinaten als Ist-Koordinaten für den darauffolgenden Zyklus gespeichert.