Versorgung: Unterschied zwischen den Versionen
Zeile 275: | Zeile 275: | ||
|- | |- | ||
|} | |} | ||
Ist auch als [https://svn.hshl.de/ | Ist auch als [https://svn.hshl.de/usvn/project/MTR_SDE_Praktikum/show/trunk/Teams/PowerPanel/Dokumentation/BOM_SMD%20Layout_SS19.xlsx Excel] Tabelle im SVN hinterlegt. | ||
= Umsetzung = | = Umsetzung = |
Version vom 20. Juni 2019, 08:22 Uhr
Autor: Michael Menke

Einleitung
Auf dieser Seite werden die einzelnen Teilbereiche der Versorgung des Fahrzeugs beschrieben.
Das Fahrzeug wird über insgesamt drei Akkus versorgt.
Ein Akku versorgt die zwei Motoren für die Lenkung und Antrieb und zwei Akkus, die in Reihe geschaltet sind, versorgen den Computer mit Strom.
Diese Akkus sind LiPo Akkus mit zwei Zellen in Reihe und kommen so auf 8,4V.
Der PC wird durch eine Referenzspannung heruntergefahren, wenn die Spannung der Akkus zu gering ist.
Anforderung
Die Anforderungen unterscheiden sich in zwei verschiedene Bereiche und zwar in das Pflichtenheft und das Lastenheft. Dabei wurde die Anforderung im Lastenheft von den Professoren vorgegeben. Diese Anforderung wurde dann im Pflichtenheft erweitert.
Systementwurf
Das PowerPanel beinhaltet drei Funktionen, die Unterspannungs-Schutzschaltung, die Akkustandsanzeige und die Umschaltung der Stromquellen.
Die Unterspannungs-Schutzschaltung verhindert die Tiefenentladung der Akkus.
Akkustandsanzeige gibt eine Angabe über den Ladezustand der Akkus.
Umschaltung der Stromquellen soll zwischen Netzteilbetrieb und Akkubetrieb wechseln.
Akkustandsanzeige
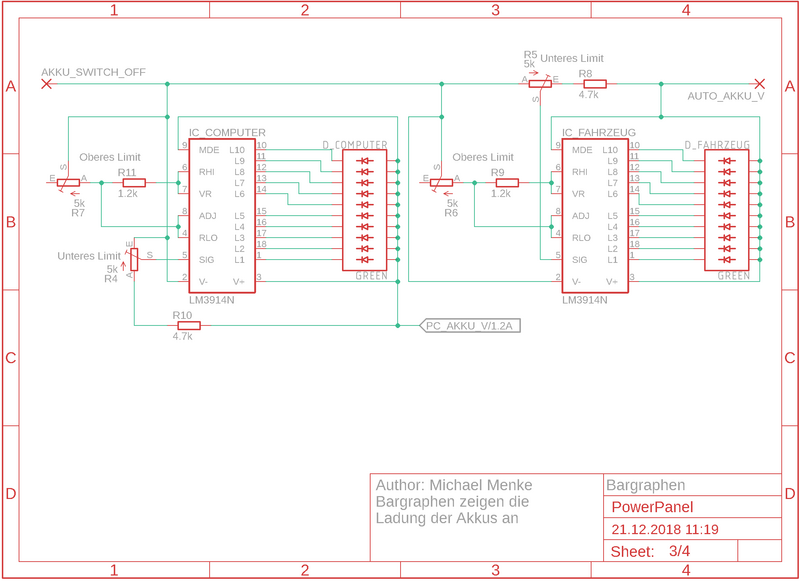
In der Abb. 3 Wird die LED-Bar Ansteuerung für die Anzeige des Akkuzustandes verwendet.
Zur Anzeige des Akkustands wurden LED-Bargraphen verwendet, welche mit dem IC LM3914 betrieben werden. Die Kalibrierung des IC LM3914 erfolgt über zwei Potenziometer. Die Potenziometer sind im Schaltplan R5,R7 für den PC-Akku und R15,R17 für den Fahrzeug Akku.
Einstellung der Bargraphen läuft wie folgt ab:
- Höchste Spannung anlegen
- Potentiometer "oberes Limit" (R7/R17) einstellen, sodass alle LEDs leuchten
- Niedrigste Spannung anlegen
- Potentiometer "unteres Limit" (R5/R15) einstellen, sodass die unterste LED leuchtet
Spannungswerte
- PC 13,5 V - 16,8 V
- Fahrzeug 6,2 V - 8,2 V
Umschaltung der Stromquelle
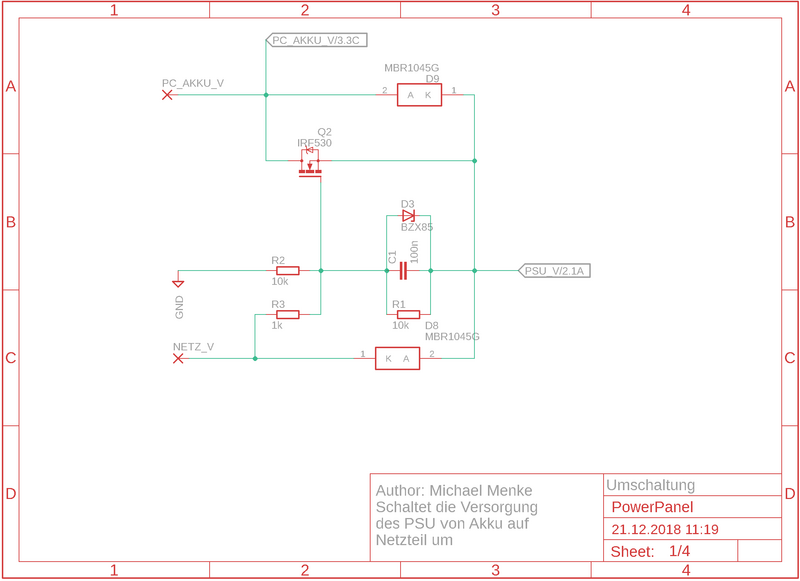
In Abb. 4 wird der Schaltplan der Umschaltung dargestellt.
Die Versorgung via Netzteil wird dem Akku vorgezogen, d. h. immer, wenn das Netzteil angeschlossen ist, wird der Akku nicht mehr belastet. Zur Lagerung des Autos kann der Hauptschalter ausgeschaltet werden, um die PicoPSU spannungslos zu schalten.
Aufbau des PowerPanels
Das PowerPanel ist im Wintersemester 2018/2019 neu gestaltet, getestet und implementiert worden. Das Layout ist überarbeitet worden in der Form, dass der Schalter, welcher den Akku zuschaltet, vor dem Unterspannungsschutz gesetzt wurde und somit das System den Akku nicht weiter entladen kann, wenn dieser Schalter umgelegt wurde. Die Sicherung ist in den Kabelbaum, welcher zur PowerPlatine führt, implementiert worden. Die Designfehler der Vorgänger sind ausgemerzt worden.
In der Abb. 5 wird der Schematische Aufbau des PowerPanels dargestellt.
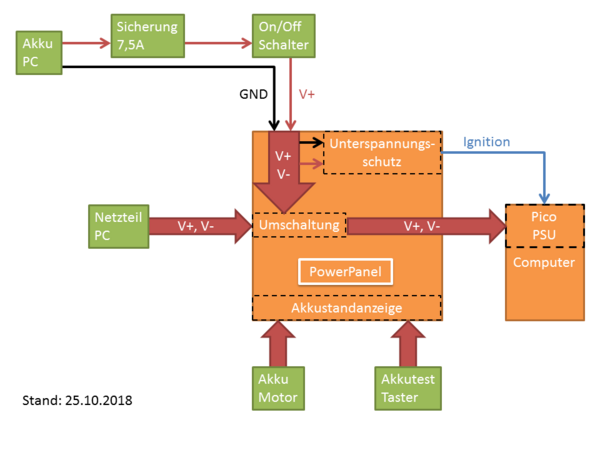
Bill of Materials
Die BOM für die Bestückung der Platine. Da wir in diesem Semester eine Neuentwicklung der PowerPlatine vorgenommen haben sind viele der Bauteile, vor allem die SMD-Bauteile nicht in der Hochschule vorhanden.
Anzahl | Komponente | Wert |
---|---|---|
4 | Trimmer THT | 5 kOhm |
3 | Stiftleiste gerade | |
2 | Standarddiode S1B DO-214AC | 100 V, 1 A |
1 | Widerstand SMD 1206 | 100 kOhm |
3 | Widerstand SMD 1206 | 47 kOhm |
1 | Widerstand SMD 1206 | 22 kOhm |
1 | Widerstand SMD 1206 | 10 kOhm |
2 | Widerstand SMD 1206 | 4,7 kOhm |
2 | Widerstand SMD 1206 | 1,2 kOhm |
1 | Widerstand SMD 1206 | 1 kOhm |
1 | Widerstand SMD 1206 | 0,5 kOhm (0,47 kOhm) |
2 | Widerstand SMD 1206 | 0,1 kOhm |
2 | Keramik Kondensator | 4,7 nF (radial bedr.) |
1 | Operationsverstärker | TL071CD |
2 | Schottky Diode | 1N5817G |
1 | MOSFET N Kanal | IRF 8010 |
1 | MOSFET P-Kanal | ZVP 2106A |
1 | Bipolartransistor | BC329C |
2 | Sockel | DIP20 |
2 | Sockel | DIP18 |
1 | MOSFET | IRF5305 |
1 | Zener-Diode | BZX85C15 |
2 | Schottky Diode | MBR1045 45 V |
2 | Bargraph | DC-7G3EWA |
2 | Bargraph Treiber | LM3914 |
1 | Keramik Kondensator | 100 nF (radial bedr.) |
1 | Festspannungsregler 3,3 V | LF33CV |
Ist auch als Excel Tabelle im SVN hinterlegt.
Umsetzung
Bei der Umsetzung wurde eine Platine mit EAGLE entworfen und gefertigt. Das Tool der Hochschule ist normalerweise Ultiboard, aber nach Rücksprache mit Herrn Kleine wurde gestattet EAGLE zu verwenden, da dieses dem Studenten schon vorher bekannt war.
Des Weiteren steht für Studenten EAGLE kostenlos zur Verfügung. Durch den geringen Kontakt zu Ultiboard im Studium ist die Einarbeitungszeit identisch. Bei Problemen mit EAGLE findet man im Internet bei Weitem mehr Tutorials und Hilfestellungen als bei Ultiboard. Die benötigten Footprints für die Bauteile gibt es für EAGLE in verschiedenen Bibliotheken, bei Ultiboard müssen diese von Hand erstellt werden.
Es gibt noch eine Vielzahl an weiteren Vorteilen EAGLE gegenüber von Ultiboard.
Falls die zukünftigen Studenten kein Interesse daran haben EAGLE zu benutzen gibt es die Möglichkeit das EAGLE Layout als Grafik zu exportieren und dann in Ultiboard zu importieren.
Dabei müssen dann die Leitungen nachgezeichnet werden.
Aufbau des Platinenlayouts
Nachfolgend ist das Design der neuen PowerPlatine einzusehen. Die Vorderseite ist mit den Treibern der LED Bars und der LED Bars ausgestattet. Auf der Rückseite sind die restlichen Bauteile, wie Widerstände, Kondensatoren und Potenziometer verbaut. Die Abmessungen und Beschriftungen stimmen mit den der alten Platine sowie mit den Maßen des Frontpanels überein.
In Abb. 6 wird das Layout dargestellt.
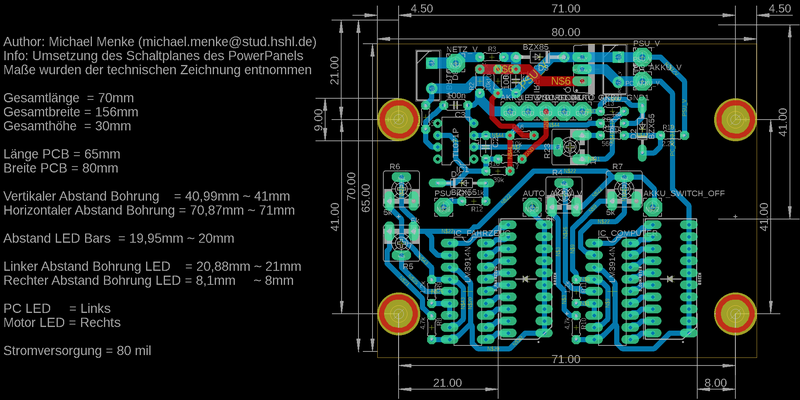
Dieses Layout durchlief zwei Review-Prozesse. Bei dem ersten Review wurde ein Fehler entdeckt. Bei dem zweiten Review wurden keine Fehler mehr entdeckt. Vor der Fertigung wurde das Layout auch auf Papier ausgedruckt und ausgeschnitten. Dieses Vorgehen soll sicherstellen, dass die LED Bargraphen und die Bohrungen an den richtigen Positionen sind.
Nach dem Fräsen der Platine ist bei dem Bestücken ein Fehler aufgefallen. Es wurde ein vertikaler Footprint für die Widerstände verwendet, dieses war nicht in dieser Form geplant. Durch die vertikalen Widerstände wird der benötige Platz für das PowerPanel größer, aber der Bauraum ist ausreichend und daher kann dieser Fehler vernachlässigt werden.
Aufbau der alten Platine
Auf den folgenden Abbildungen ist die Vorder- sowie die Rückseite des Panels zusehen. Signifikante Merkmale sind die Aufdickung der Leiterbahnen für die Plus- und die Groundverteilung. Die Anschlussleitungen werden bei der neuen Platine nicht mehr gesteckt, sondern sind fest angelötet. Aufgrund doppelseitiger Auftragung des Lötzinns ist die Haltbarkeit und Festigkeit gesichert. An die verlöteten Leitungen werden Stecker befestigt um ein Ausbau der Platine weiterhin zuermöglichen.
In der Abb. 7 und 8 wird die Bestückte Platine dargestellt.
-
Abb. 7: Vorne
-
Abb. 8: Hinten
Anschlüsse
Die Anschlussleitungen sind angelötet. Die Kabel werden vorkonfektioniert mit neuen Steckern bzw. Buchsen. Nach eingehender Recherche ist der Entschluss gefasst worden, dass bestimmte Leitungen zu einem Stecker zusammengefasst werden können. Die zu verwendenden Stecker sind AMP Superseal von TE Connectivity. Diese sind steckbar, flexibel und haltbar, somit ist die nachträgliche Bearbeitung und das Abbauen der Powerplatine ohne Bedenken möglich. Die Kurzschlussgefahr ist signifikant gemildert worden. Es werden zweipolige und dreipolige Stecker verwendet.
Komponentest
!!! Test von PowerPanel verlinken
Die Funkionen wurden sparte getestet vor und nach dem Einbau. Für jede Funktion wurde ein Test entworfen und durchgeführt.
Für die Durchführung der Tests wird ein Funktionsgenerator, ein Labornetzteil und ein zwei Kanal Oszilloskop benötigt. Die Tests sollten nur an einem ausgebauten PowerPanels durchgeführt werden.
Umschaltung
Die Umschaltung zwischen Akkubetrieb und Netzbetrieb. Das folgende Schaubild in Abb. 9 zeigt den schematischen Aufbau des ersten Tests.
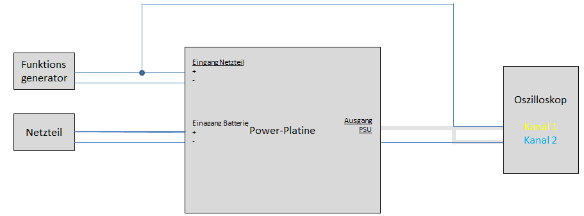
Das PC-Netzteil wird durch den Funktionsgenerator simuliert. Die Batterie wird durch eine konstante Spannung des Labornetzteils dargestellt. Der Ausgang, welcher normalerweise an das PicoPSU angeschlossen wird, wird an einen Kanal des Oszilloskops angeschlossen. Der zweite Kanal dient als Referenz und wird mit dem Funktionsgenerator verbunden. Der Funktionsgenerator wird auf eine periodische Dreiecksspannung eingestellt, welche eine Hysterese von 18 V aufweist. Das Labornetzteil steht auf einer konstanten Spannung von 12 V. Die in Abb. 10 zusehende Auswertung des Oszilloskops zeigt, dass wenn die Spannung des Netzteils unter 12 V liegt, dann der Ausgang die „Batteriespannung“ liefert. Sobald die Dreiecksspannung wieder über die 12 V der „Batterie“ steigt, schaltet der Ausgang um auf die Spannung des Funktionsgenerators bzw. des „PC-Netzteils“.
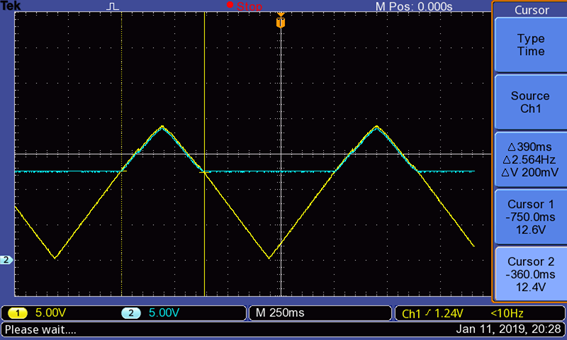
Bargraphen
Der Akkutest bezieht sich auf die beiden LED-Bars. Es wird getestet, ob die LED-Bars bei vorgegebener Spannung leuchten, bzw. wie viele LEDs bei welcher Spannung leuchten. Die Kalibrierung der LED-Bars ist im Test mit inbegriffen und wird im Verlauf erläutert. Der Test wird mit einem Labornetzteil simuliert, welches zuerst den PC-Akku simuliert und anschließend den Fahrzeugakku. Das folgende Schema zeigt den Aufbau des Tests der LED-Bars für den PC-Akku. Der Test des Fahrzeugakkus ist genauso aufgebaut.
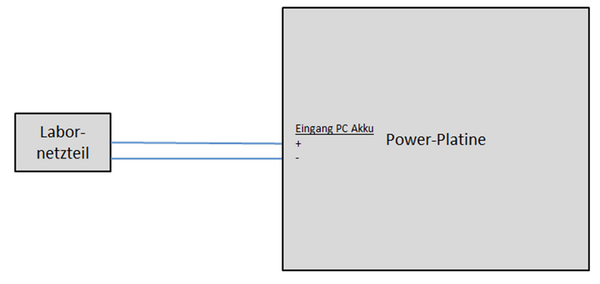
Das Labornetzteil wird auf die höchstmögliche Spannung, welche die Batterien annehmen können, eingestellt. Die maximale Spannung liegt bei 16,5 V, wenn alle Akkus komplett vollgeladen sind. Wenn dieser Zustand erreicht ist (im Testfall: Labornetzteil auf 16,5 V) dann müssen alle LEDs der Bar aufleuchten. Um dieses obere Limit zu konfigurieren, muss das Poti „oberes Limit“ justiert werden. Der Widerstand muss so eingestellt werden, dass bei 16,5 V die LEDs aufleuchten. Wenn dieser Zustand hergestellt ist, muss das untere Limit durch das Poti „unteres Limit“ eingestellt werden. Die Spannung des Netzteils wird auf den niedrigsten Wert, welchen der Akku annehmen kann, eingestellt. Dieser liegt bei 13,5 V. Das Poti muss bei dieser Spannung so eingestellt werden, dass nur noch eine LED der Bar leuchtet. Die Kalibrierung des Fahrzeugakkus verläuft genauso, jedoch müssen das obere Limit bei 8,2 V und das untere Limit bei 6,2 V liegen.
Test nach Einbau
Testverfahren identisch mit den Tests vor dem Einbau. Ergebnisse, wie erwartet, identisch mit Tests vor dem Einbau.
Das PowerPanel ist vollständig funktionstüchtig.
Ergebnis
REQ10.2020 wurde erfolgreich erfüllt. Das Fahrzeug wird mit Akkus versorgt, welche sich auf dem Fahrzeug befinden.
Die Akkus werden vor Tiefenentladung geschützt durch das PowerPanel, dieses wurde auch mit Tests nachgewiesen. Das PowerPanel verfügt noch über weitere Funktionen zur Verwaltung der Akkus.
Des Weiteren wurde neben dem PowerPanel noch ein Template für Neuentwicklungen angelegt und ein Design Rule Check. Mit diesen Hilfsmitteln wird eine Erweiterung des Panels beschleunigt.
Das Ergebnis ist in Abb. 7 und 8 zu sehen. Dies ist die gefertigte Platine. In der Abb. 0 wird die fertige Platine eingebaut dargestellt.
-
Abb. 0: Eingebautes PowerPanel]]
-
Abb. 7: Vorne
-
Abb. 8: Hinten
Zusammenfassung
Die Anforderungen wurden erfolgreich umgesetzt, aber die Schaltung kann noch erweitert werden.
Es wurde umfangreiches Wissen im Bereich der Hardware Entwicklung erlangt. Dieses Wissen war vor allem im Bereich des Layoutentwurfs.
Die Anforderungen sollten noch erweitert werden, und zwar sollte der Schutz des Akkus erweitert werden. Ein durchgehender Tiefenentladungsschutz sollte eine Anforderung sein.
Lesson Learned
Diese Fehler wurden bei dem PowerPanel vom Tag "20181118_PowerPanel" festgestellt.
Es wurde ein neuer Stand erstellt, welcher der aktuelle Stand ist. Bei weiteren "Lesson Learned" Momenten wird dieser Artikel mit einem neuen Abschnitt erweitert.
Alte Fehlerliste
Ausblick
Literatur
Anleitungen
→ zum Artikel Optimierung PowerPanel Optimierung der Power-Platine
→ zurück zum Hauptartikel: Fahrzeughardware